GF Machining Solutions’ laser ablation technologies are providing car manufacturers with new and innovative ways to achieve product and market differentiation, and this is particularly important with electric vehicles (EVs), where aesthetics as well as eco-friendly imperatives, are big business.
In this developing landscape it is understandable why a growing number of car manufacturers, throughout the supply chain, are looking closely at laser ablation, and the competitive advantage it can provide. The technology provides manufacturers with the ability to create complex patterns and other functional characteristics on injection mould cavities and inserts – allowing them to be replicated on finished products. Textured surfaces can have an aesthetic and functional appeal and purpose. For example, grainy textures and streamlined shapes of car interior and exterior components, can add to the impression of quality, and even luxury, without incurring a significant on-cost.
Through laser texturing, product designers are developing precise and complex textures through five-axis laser texturing driven by digital imaging and CNC technology. The speed and convenience of laser technology facilitates a rapid response to changing demands for product customisation and helps speed up time-to-market. Moulds for automotive components as large as door panels, bumpers, and even entire interiors can be laser-textured directly, quickly and accurately.
Innovative pattern choicesNow, textures generated with 3-D CNC laser technology offer designers a dramatically expanded range of innovative and different pattern choices, many of which were not possible or viable to create with previous texturing technologies.
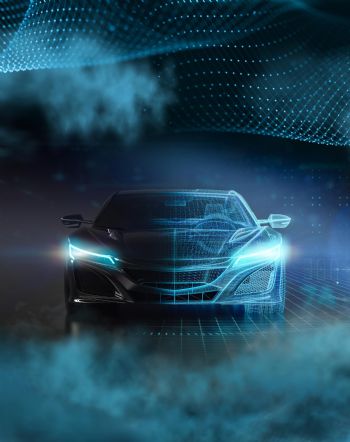
In addition to stylistic choices, lighting designers are now able to incorporate more advanced textures due to recent advancements in efficient light illumination technologies. These technologies are also deployed inside lights and interior ambient lighting. Not only does every car manufacturer want to have a different pattern than its competitors, but each manufacturer also wants consumers to be able to distinguish different styles from one another.
GF Machining Solutions’ laser texturing technology allows complete control of lens mould features. It provides distinct demarcation between textured and unaffected areas, something that can be difficult or impossible to achieve when using chemical etching methods.
Tyre OEMs and mould makers need to achieve distinctive and contrasted branding with the side walls of tyres providing the optimum position. However, traditional manufacturing processes are currently limited making them unable to hit production targets while introducing new design features. To overcome this issue, many tyre manufacturers and companies in the supply chain are turning to GF Machining Solutions’ laser technology.
Benefits of laser texturingCar manufacturers have been early adopters of laser texturing recognising its ability to help them respond quickly to market trends and to keep the ahead of their competitors. It has helped them in the following ways:
Aesthetic and functional textures — traditional technologies prevent designers from using all their creative ability. They act as a limiting factor to the development of new designs for both exterior and interior car parts. In addition, the emergence of functional surfaces, for example, with anti-scratching capabilities and water repellent properties, are pushing non-laser techniques to their limits. When using traditional design and aesthetic technologies, such as chemical etching, designers are not able to fully, or easily, transfer the complete design pattern required inside the mould. This is down to the etching process itself and how the acid reacts with the mould. In addition, the process makes it difficult to achieve very low gloss or high gloss levels on certain plastics.
Complex manufacturing processes — today, creating textures requires complex production lines with only limited flexibility. Traditional manufacturing processes can involve a multitude of different steps – with each requiring a different skill set to achieve. Applying, for example, an acid film on a mould can take many hours and is labour intensive. This can add time and cost to a job.
Repeatability of results — one of the most important challenges when creating textures is design repeatability. With conventional techniques, this is difficult to achieve and almost impossible to replicate, from mould to mould, even when manufacturing occurs in the same factory setting. Repeatability and consistency is also difficult when different polymers (including recycled plastics) and injection technologies are employed.
Environmental consideration — one of the major problems when using chemical etching is chemical waste and its treatment which, from an environmental and economic perspective, is a growing issue for etchers, contractors and communities, and economic and social institutions and political organisations too.
Skilled workforce — traditional technologies often still involve many manual steps and interventions. This leads to longer manufacturing times and can impact on repeatability. In addition, many companies face difficulties in attracting skilled employees and experts in manual texture creation.
Material selection — chemical etching processes involves the use of specific steels which limits the choice of materials that can be used.
Environmentally friendly process
GF Machining Solutions laser texturing systems offer fully digitalised manufacturing processes for generating detailed and nuanced texturing, micro-structuring and marking. The technology is faster, more accurate and more repeatable than mechanical and chemical processes, in addition to being environmentally friendly.
Multiple textures can be applied on the same component, with no need for masking that is required in chemical etching. The laser systems use high-quality digital images and CAD data, allowing for completely reproducible results in both large and small job batch sizes.
GF Machining Solutions systems’ dedicated workstation software enables in-depth job preparation control (CAD/CAM), including UV mapping for applying textures and 3D simulation. Digital images can be bitmap/grayscale files created in Photoshop or STL files derived from a natural surface via reverse engineering with a 3-D scanner. Different machine models can handle workpieces up to 4m x 3m in size.
After the machine’s workstation software merges a virtual workpiece with a virtual texture, the application engineer can preview the final design results. Programming of laser texturing operation basically requires only the same programming skills required to machine a simple component on a conventional CNC machine tool.
The machines use a pulsed fibre laser to render the desired patterns or textures. Fibre lasers are extremely precise and can remove several microns of material at a time. Machines can make very light and shallow cuts or no cut at all, sometimes using the laser to only change the visual aspect of a part’s surface for strictly aesthetic reasons. The choice of laser texturing technology (laser pulse duration, power, texturing pattern) is driven by the surface that is required.
While these machines employ nanosecond lasers, GF Machining Solutions also offers machines that use femtosecond or a combination of the two. Nano-pulse duration lasers will both ionize metal and locally heat the surface being treated, while the ultra- short pulse duration of femtosecond lasers prevents materials from entering a fusion state during texturing, making them ideal for use on heat-sensitive parts.