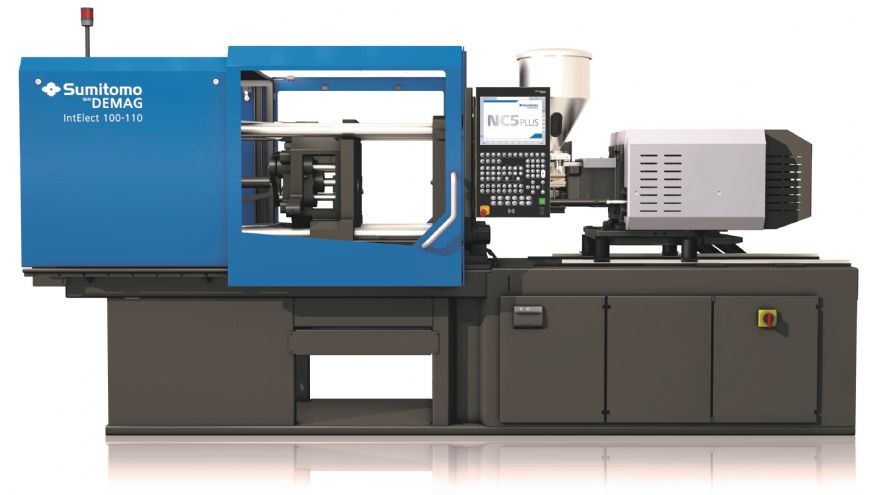
Recently unveiled at
Sumitomo (SHI) Demag’s European roadshow, ActiveMeltControl (AMC) automatically adapts the injection moulding process by continually monitoring variations in holding pressure and switch over position; and once a parameter is identified as drifting towards the tolerance limits that have been set by the user, AMC automatically amends the set parameters to compensate for the variation. The adjustment bandwidth is also defined by the processor.
This development has been driven by the changing quality of plastics due to fewer virgin materials and more recyclable content. Thomas Schilling, the company’s product manager for digital solutions, said: “Many customers have requested a digital solution to compensate for these variations when manufacturing precision parts using our all-electric machines. That is why we introduced AMC as a completely independent software module that complements our established active modules.”
Area sales manager Ashlee Gough added: “With AMC, we can now automatically adapt to melt viscosity variations in nearly all applications and materials. These variations may be due to batch fluctuations, recyclables, regrind, drying differences, dosing variations, or the use of additional additives. Indeed, variations in the melt flow index (MFI) in 100% recycled material can now be corrected by the software, which means process stability is now comparable to a process that uses virgin material.
“This capability offers processors greater manufacturing flexibility, allowing for the use of a broader range of post-consumer and post-industrial recycled material types. Even customers with defined processing references benefit, as AMC instantly addresses any variability to maintain absolute processing precision and stability; and because AMC only sets the limits for holding pressure and switch over position it can be used in all industries, including those where there are defined tolerances for validated process parameters that cannot be exceeded or overridden by machine operators.”
Mr Gough concluded: “Achieving more consistent part weights within a processing batch means that the ROI can be exceptionally fast. Additional benefits include better process consistency, longer machine uptime, and reduced scrap. All of which contribute to greater productivity and sustainability. Moreover, while available as an optional extra on our newest IntElect 2 machine series, it can also be retrofitted to older IntElect 2 machines.”