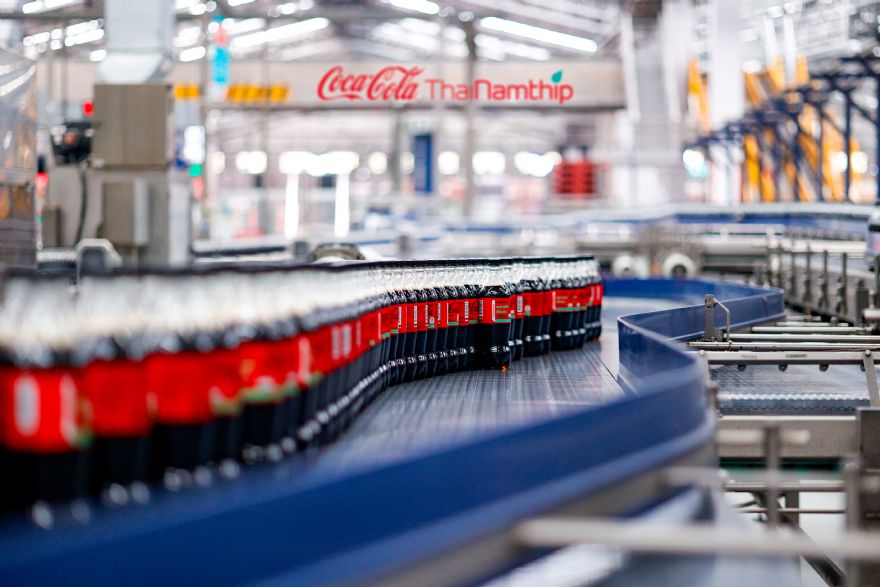
As 2024 draws to a close, it is only natural to reflect on the past and anticipate what lies ahead. What lessons can be carried forward and which trends will shape the manufacturing industry in the future. Ian Rowledge, founder of the manufacturing optimisation software
LineView, suggests that manufacturers must take a broader, long-term perspective. He says one year is a short timeframe in which much can happen and that true transformation requires thinking beyond annual cycles to re-imagine the factory of the future.
Mr Rowledge said: “The manufacturing sector now stands at a crossroads. After a year defined by energy price volatility and evolving global dynamics, manufacturers are navigating workforce instability, rising costs, and the gradual integration of emerging technologies. In an environment where uncertainty has become the norm, resilience demands strategic investments that address immediate challenges while paving the way for long-term growth.”
For example, a report by the Food and Drink Federation underscores both the scale of the challenge and the opportunity, highlighting a £14 billion growth gap for the UK’s food and drink manufacturing sector alone. Operational efficiencies hold the key to closing this gap, unlocking significant productivity gains and cementing the industry’s role.
Mr Rowledge says that as we enter 2025, manufacturers should look to recalibrating their strategies, focusing on resilience, innovation and growth that extends far beyond the coming year.
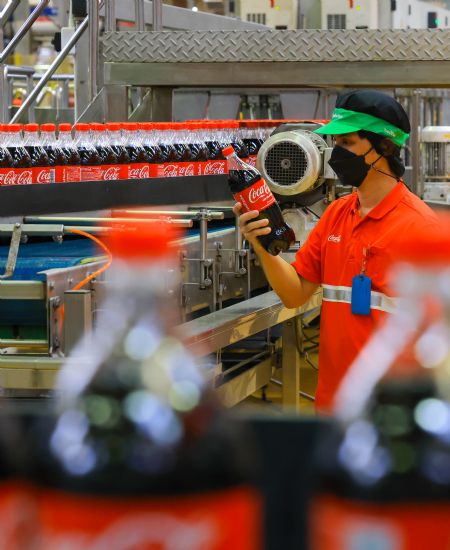
He continued: “Energy prices are a key concern for many manufacturers. As the volatility of global energy markets grabs headlines, manufacturers must look beyond the noise. Energy price fluctuations have become a constant; rather than focusing on the unpredictable, the key is to optimise what is within their control.
“Efficiency gains are essential for modern manufacturing. Streamlining operations and optimising production lines directly influence energy consumption, reducing waste and boosting productivity. By focusing on efficiency, manufacturers can take proactive steps to counter rising energy costs, safeguarding both the sustainability and resilience of their operations in an increasingly volatile market.”
He urges manufacturers to turn their attention to the ‘low-hanging fruit’ of process optimisation. Simple yet impactful improvements, for example, boosting production line efficiency by just a few per cent can significantly cut energy waste and reduce costs. This approach enables manufacturers to minimise their energy footprint without becoming overly reliant on external factors like market stability.
Moreover, shareholder pressure to meet ESG (environmental, social and governance) criteria means manufacturers will need to demonstrate tangible progress towards sustainability. This will likely accelerate investments in energy-efficient equipment and digital solutions that track and optimise energy usage across operations.
Future-proofing skills Mr Rowledge added: “As automation reshapes manufacturing, the sector continues to face a persistent skills gap. Equipping workers with the knowledge and tools to adapt to increasingly advanced environments will be a defining challenge of 2025 and beyond. Rather than displacing workers, the focus for manufacturers is shifting to enablement - using technology to enhance decision-making and productivity on the factory floor. A 2024 report from Epicor underscores this trend, revealing that 91% of managers are prioritising upskilling initiatives, a sentiment supported by 70% of workers.
“By integrating digital tools that streamline processes and provide actionable insights, manufacturers can empower teams to address inefficiencies, reduce downtime and boost output. These solutions not only help close the skills gap but also ensure that workers remain at the heart of the industry’s progress toward a more automated future.”
Artificial intelligence (AI) is often heralded as manufacturing’s silver bullet, but its current contributions are incremental rather than revolutionary. Rather than replacing human expertise, AI acts as a co-pilot, enhancing decision-making and boosting productivity by predicting inefficiencies and recommending actions to prevent disruptions.
Mr Rowledge explained: “Despite its potential, AI faces hurdles. High implementation costs, the need for clean and structured data, and energy-intensive processing limit its widespread application. Additionally, AI cannot replicate human creativity and nuanced problem-solving, leaving essential tasks firmly in human hands. However, as we have seen with other groundbreaking technologies - like electric vehicles - these barriers are diminishing. Over the next few years, AI tools will become more affordable, efficient, and accessible, creating opportunities for SME manufacturers to harness their potential.”
He explained that while AI is not a universal remedy, it is a critical step forward for manufacturers looking to remain competitive. Embracing AI and other emerging technologies allows businesses to build familiarity and refine their use cases, positioning themselves to reap the benefits as these tools become more advanced and cost-effective.
Shaping the future He said: “The challenges of 2025 demand more than short-term fixes. Efficiency isn’t just a ‘buzzword’, it is the bedrock of sustainable and resilient manufacturing. To stay competitive amid intensifying global pressures, manufacturers must invest strategically. By optimising energy use, enabling workforce adaptability, and integrating AI as a decision-making tool, they can not only close the productivity gap but also enhance their global standing.”
Mr Rowledge concluded: “The factories of the future will not be defined by what they produce but by how they produce it. Prioritising innovation, sustainability, and long-term thinking will ensure the manufacturing sector remains a pillar of national economies. In a rapidly evolving landscape, these actions will secure its leadership for decades to come.”