The HG500 ultra-high-performance helical profile grinding machineRochdale-based
PTG Holroyd Precision has launched what it describes as ‘the world’s most versatile, ultra-high-performance machine for precision grinding the helical profiles that are used across the air and refrigeration compressor industry’.
Called the HG500, the machine has been developed to meet the needs of manufacturers with varying production requirements, including some of the largest helical rotors used in refrigeration and air-compressor manufacturing. The machine can rough- and finish-grind rotors down to 50mm in diameter, right up to a maximum 510mm in diameter, 130mm profile depth and 1,500kg in weight.
Mark Curran, PTG Holroyd’s sales director, said: “Talking to customers following the recent upgrade to our highly successful TG Series of thread grinding machines, we realised that a very real demand also existed for a new large-capacity helical rotor grinding machine. Through the HG500, we have not only built a machine that is able to produce a wide variety of rotor sizes but, more importantly, one that can also accommodate the largest, most energy efficient helical profiles.”
When specified in standard form, the HG500 can utilise either a 500mm vitrified dressable aluminium oxide grinding wheel for maximum flexibility in production strategies and product development, or use plated CBN roughing and finishing wheels for cost-effective volume production. Alternatively, for manufacturers who precision-grind the largest of helical components, a 600mm vitrified dressable aluminium oxide grinding wheel option is also available for maximum wheel life.
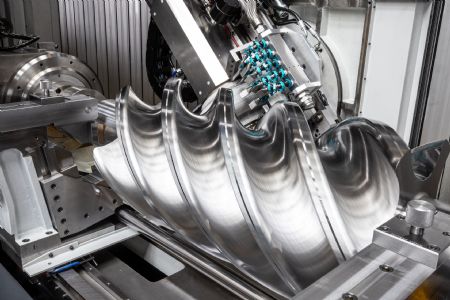
As well as ensuring considerable flexibility in the HG500’s rotor production capability, providing powerful, intuitive programming was also a key objective of PTG Holroyd’s design team – something that was achieved through the use of a Siemens Sinumerik One CNC. PTG Holroyd was the first machine tool manufacturer in the UK to embrace the features of the new Siemens CNC, having integrated it into its HG350 machines and, more recently, into its well-established TG Series of rotor and thread grinding machines.
Mark Curran continued: “Being first to use the Sinumerik One also gave us the unrivalled opportunity to work in close collaboration with Siemens to tailor the CNC’s capability to our precise needs. The result is class-leading integrated safety and failsafe features, enhanced reporting of machine health and performance data, and uncompromising levels of industrial security. Enhanced connectivity and performance are provided via additional Profinet interfaces and OPC/UA interfaces – all made possible thanks to a PLC that is up to 10-times faster than earlier Siemens controls.”
Renishaw probe and innovative featuresTo enable maximum probing strategies on even the longest of components from the onboard Renishaw OSP60 scanning probe with SPRINT technology, the HG500 uses a travelling grinding head instead of a conventional grinding table. Variable-frequency cooling from a high-pressure unit with wheel scrub ensures highly efficient coolant usage, while intelligent, programmable eco modes minimise energy consumption between manufacturing cycles.
Mr Curran explained: “In addition to developing what we believe is the most flexible, highly efficient machine for ultra-precise large and small rotor production, in keeping with the Holroyd mantra of ‘making the complex simple’, we have also ensured that the HG500 is extremely intuitive to setup and run. Rapid set-up of same component batches is delivered via the HG500’s data and program files, while the machine’s CNC-controlled dressing system provides automatic wheel profile correction for each dress cycle, along with programmable dressing feed rates for roughing and finishing.”
Integrated as standard with the HG500, is PTG Holroyd’s industry-leading profile development tool, the Holroyd Profile Management System (HPMS), which comprises a suite of advanced programs that enable the straightforward manipulation and analysis of profiles. HPMS is used in the development and control of a wide range of helical profiles for screw rotors, vacuum and pump screws. HPMS can also be used to assist the control of a profile during production and provides automatic, in-cycle profile updates and dresser path corrections, in-process lead and profile measurement and CBN wheel adjustment and correction.
HG500 key features include: 50 to 510mm maximum diameter grinding capability; 1,500kg maximum component weight; grinding wheel options — vitrified dressable Al2O3 or plated CBN; optional vitrified dressable Al2O3 600mm grinding wheel for larger components; Siemens Sinumerik One CNC integrated profile management system; accelerated, simplified setup, with automatic wheel profile correction; integrated Renishaw OSP60 scanning probe with SPRINT technology; Holroyd Profile Management System (HPMS); intelligent, variable frequency, high-pressure cooling system; and programmable ‘eco’ modes to minimise energy consumption.