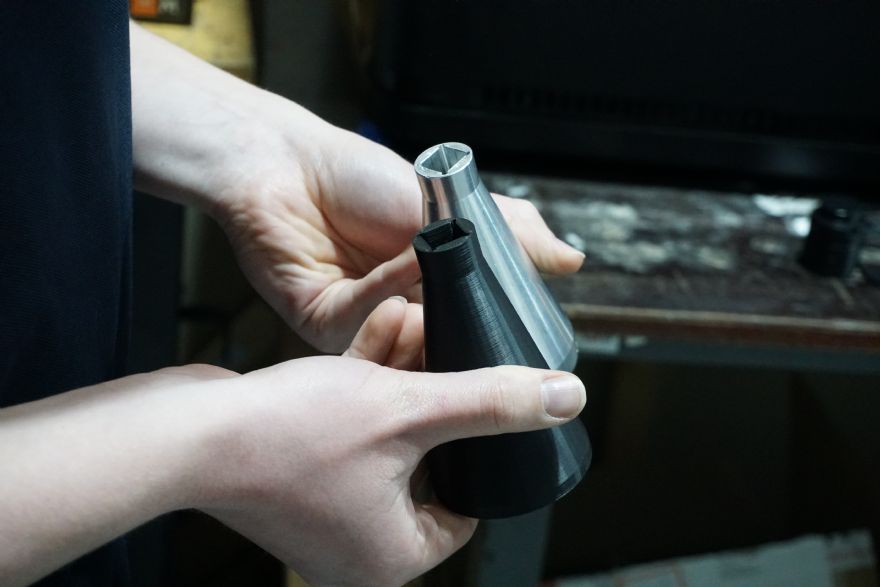
Run by 45 student volunteers and focused on developing the Forze 9 hydrogen-powered Le Mans prototype racing car, the Forze racing team is competing in the Supercar Challenge in the Benelux and ‘committed to advancing clean energy in motorsport’ with a specific focus on hydrogen-powered vehicles.
With limited resources and tight deadlines, the team has embraced 3-D printing as a key technology for fast-tracking their prototyping, manufacturing, and iterative design processes. Forze says the integration of additive manufacturing (AM) has allowed the team to quickly create and refine parts, optimise its designs, and adapt to ‘the unique challenges of creating a hydrogen-powered racing vehicle’. These include not only speeding up the engineering cycle but also enabling the team to experiment with designs.
“Being a student-run team, Forze faces numerous challenges, including limited budgets and access to external manufacturing services. Traditional methods, such as CNC machining, would have meant long lead times and high costs; and given the complexity of developing a hydrogen-powered vehicle, rapid prototyping was essential to test, iterate, and refine key parts on the fly, particularly to ensure proper fit and function.”
The Ultimaker Method XL 3-D printer has become central to the Forze team’s workflow. It features a dual-extruder system, 305 x 305 x 320mm build volume, user-friendly features, and allows the team to print prototypes quickly and efficiently. Furthermore, the printer has improved integration between different components of the vehicle, allowing the team to quickly test parts, check the fit, and even identify potential issues before they affect the larger assembly; it can produce parts using materials that include ABS, carbon fibre, and the Rapid Rinse water soluble material.
For prototyping, the team primarily uses ABS due to its durability and ease of use, while carbon fibre is used for high-strength applications like structural parts. The Rapid Rinse support material is used when making complex parts that require intricate geometries without support structures; and although the team has PLA available, this is typically reserved for smaller, non-critical parts.
A team representative concluded: “Having access to 3-D printing in an academic setting provides students with the opportunity to work with advanced manufacturing techniques that are increasingly common in industry. Many engineers are now expected to know how to use 3-D printing in product development, and teams like Forze offer students a chance to build these skills in a real-world setting, even before graduation.”