Peter Atkins, Matt Harwood, Rob Andrews, Steve Smith, Mark Harwood and Caswell Fray. Photo: Barkley PlasticsBarkley Plastics, a plastic injection moulding and toolmaking specialist, is celebrating a big birthday in style after securing a string of exciting new projects. The company, which marks 60 years of business later this month, has won work to produce controller parts and ambient lighting for a luxury high-end shower manufacturer, as well as car charger components for Fast Amps and environmentally-friendly plumbing fittings for Ecoclip.
These latest ‘wins’ - combined with its own ‘PlasFloor’ flooring tile range and ongoing interior trim and specialist lighting products orders from Nissan, Toyota, JLR and several supercar manufacturers — have helped the company bounce back from a difficult two years, with the firm now on course for to eclipse a £4 million turnover amid exciting developments to further increase revenues by 2026. Expansion plans have been boosted by the £100,000 modernisation and streamlining of its Highgate facility to include several collaborative robots (cobots) for increased automation and a new temperature-controlled quality control room that houses two coordinate measurement machines and a vision scope system.
Pictured left: Barkley Plastics in the early daysMatt Harwood, who took over as managing director from his father Mark in 2022, said: “Since Covid-19 there has been a lot of supply chain disruption and the automotive sector has been extremely volatile in terms of volumes. Like before in our 60-year history, we have chosen to face these challenges head-on and are now in a position to target a significant amount of reshoring work that directly suits our technical plastic moulding expertise and the fact we have our own on-site toolroom.”
He continued: “It is a great achievement to last six decades in manufacturing and we have seen some interesting times. What has stood out throughout has been the passion from our staff to deliver the very best service to customers - this is typified by the fact we have six members of our 53-strong workforce who have been with us for more than 30 years. Now that we have refined our factory and increased efficiency, we are in a perfect position to offer competitive prices and are determined to help bring more production back to the UK.”
High-precision toolsBarkley Plastics, which holds ISO:9001 quality and ISO:14001 environmental accreditations, produces high-precision tools capable of delivering millions of mouldings for distribution throughout the UK, Europe and across the world. With a fully equipped toolmaking facility within its moulding plant, the company can support its customers with initial design and product development, right through to manufacture and assembly, with over 30 modern moulding presses — ranging from 5 to 650 tonnes — able to produce the most intricate of components weighing less than a gram right up to parts that are a metre squared and 2.5kg in weight.
There have been some real landmark and unusual projects over the years, including the 1970s ‘Homepride Flour Men’, the Big Yellow Teapot for bluebird toys and making 20,000 plastic baubles for the world’s largest chandelier — first used at the 2014 Winter Olympics closing ceremony in Sochi, Russia.
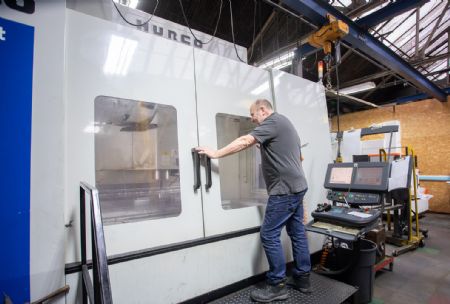
Steve Smith, operations director at Barkley Plastics, said: “The new contract with the luxury shower manufacturer is a perfect example of where we come into our own. We breathed new life into some of its near obsolete tooling, which gave them the confidence to give us the challenge of developing technical components and ambient lighting for their new product ranges. We quickly proved we could manufacture it to the quality and aesthetic finish required and, importantly, at a cost point that worked for them. I’m sure this would have gone overseas before we stepped in.”
Barkley Plastics is keen to reduce its carbon footprint and is working with partners on developing new moulding technologies that reduce energy usage and cycle times, not to mention a Net Zero project with WMG that helped it insulate some of its larger moulding machines.
Matt concluded: “We are always looking at ways where we can innovate processes and technologies, but it always seems to be that manufacturing has to do it on its own without any real support. Locally, the introduction of Birmingham’s Clean Air Zone in recent years has negatively impacted the way we operate and the Government, despite calling for growth, is introducing measures that makes it increasingly difficult for UK companies to remain competitive and in a position to take advantage of the reshoring opportunity.”