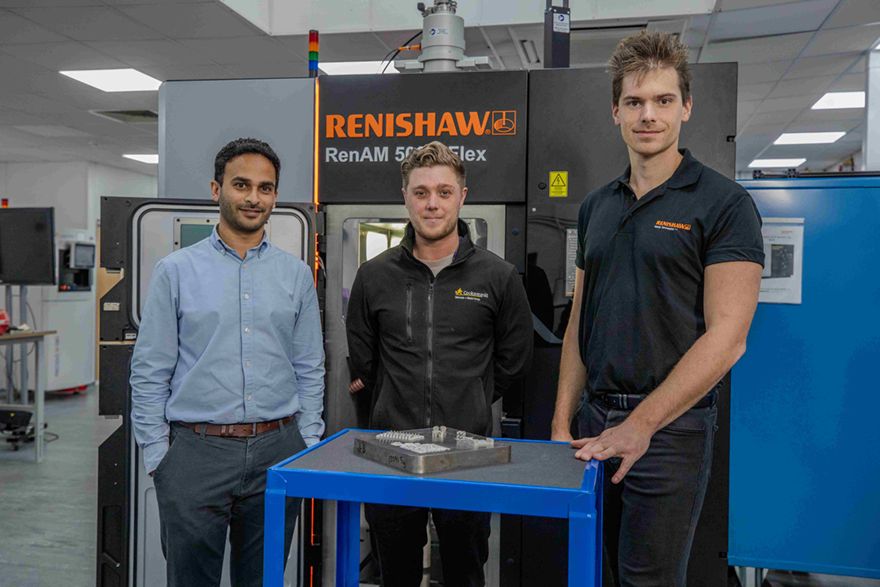
Using precious metals in additive manufacturing (AM) provides new ways to utilise these materials’ unique properties. However, the high cost of these metals means that large-scale production is often beyond the reach of many manufacturers. To address this challenge,
Renishaw helped
Cookson Industrial, a precious metal AM pioneer, succeed in making the production of platinum rhodium parts for industry commercially viable.
Based in Birmingham, Cookson Industrial is part of
Cooksongold, one of the largest suppliers of precious metals, jewellery components and tools to the global jewellery trade. Their parent company is
HM Precious Metals, one of Europe’s leading refiners and processors of precious metals, with over 950 employees across seven countries.
Cookson Industrial is on a mission to support businesses to redefine the use of precious metals in industry. The company provides an end-to-end service, including consultancy, R&D, NPD and production, helping revolutionise the industrial use of precious metals such as gold, silver and platinum. The company’s metallurgists and engineers design and develop wire, sheet, grain, sputtering targets, brazing alloys and atomised powder for industries ranging from aerospace and automotive to medical and glass fibre manufacturing.
Highly resistant alloyWhen rhodium is used as an alloying agent for hardening and improving the corrosion resistance of platinum, the outcome is a new material known as platinum rhodium. This highly resistant alloy is used in some of the most demanding applications, including furnace windings and bushings for glass fibre production. This material is the only commercially available metal that can withstand the high temperature and corrosive environment of molten glass.
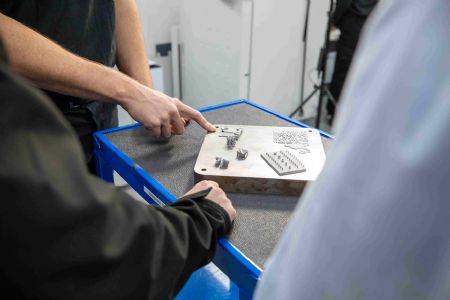
For this reason, Cookson Industrial intended to use platinum rhodium to 3-D print an extrusion mould designed for glass fibre manufacturing. However, platinum rhodium is one of the world’s most expensive metals, with prices averaging £80,000 per kg.
Given the high cost of the material, the company needed to keep waste to a minimum by retrieving and re-using as much powder as possible. This is where a
RenAM 500S Flex AM system from Renishaw provided a solution.
Part of the RenAM 500 series of high-productivity laser powder bed fusion (LPBF) systems, the RenAM 500S Flex is optimised for R&D applications. Equipped with an open-loop powder system enabling quick and easy powder swapping, this AM system speeds up the qualification of material properties, part design and process parameters. The powder management system is designed for external sieving, which allows for greater flexibility in selecting powders.
Cookson Industrial tasked Renishaw’s AM engineering team with customising the RenAM 500S Flex to maximise powder retrieval. Initial tests showed the system was already capable of achieving a low powder loss of less than 1.5%. However, Cookson Industrial needed to reduce these losses even further to less than 0.5% to minimise platinum rhodium wastage and the associated costs.
Maximise powder retrievalJason Morgan, senior applications engineer at Renishaw, said: “Achieving near-zero wastage of its precious platinum rhodium powder was a top priority for Cookson Industrial. We worked with the company’s engineers to identify ‘powder traps' and then embarked on a fast-paced schedule of re-designing and re-testing system components to maximise powder retrieval, without impacting the overall system performance.”
The customisation process included removing parts where small amounts of powder can accumulate, including overflow bellows and the rear overflow vent system. Renishaw further optimised chamber design to prevent any powder loss during the depowdering process. In addition, the company’s AM team designed special casings and covers for the lower chamber, powder flask chamber and filter cabinet, to eliminate any other potential powder traps.
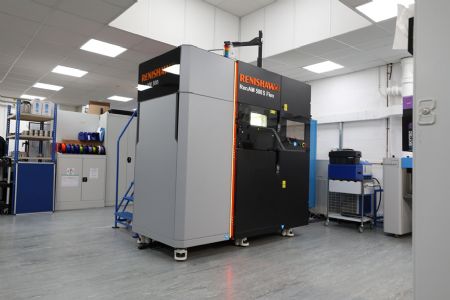
Renishaw’s customisation process was a success, enabling the RenAM 500S Flex to reduce the wastage of platinum rhodium powder beyond expectations. The AM machine saw a staggering 95% reduction in trapped powder, allowing Cookson Industrial to minimise losses and retrieve the equivalent of a teaspoon of powder per cycle (a saving of around £1,000).
Nikesh Patel, head of Cookson Industrial, said: “Renishaw’s technology and expertise were critical to the success of this important R&D project, paving the way for scalable production of high-value platinum rhodium parts across a range of applications. The ability to minimise powder loss will allow our company to save hundreds of thousands of pounds over the machine’s lifetime, which makes the difference between the application being commercially viable or not.”
Building on the RenAM 500S Flex’s outstanding results, Cookson Industrial is now planning to use platinum rhodium in other applications such as catalysts and aerospace engine nozzles.
Mr Morgan concluded: “Our successful collaboration with Cookson Industrial goes to show how Renishaw supports its customers right from the start of their AM journey, which can be especially valuable when using novel materials. The production of platinum rhodium components demonstrates that precious metals can be a commercially viable field of AM. I am excited to see what Cookson Industrial does next.”