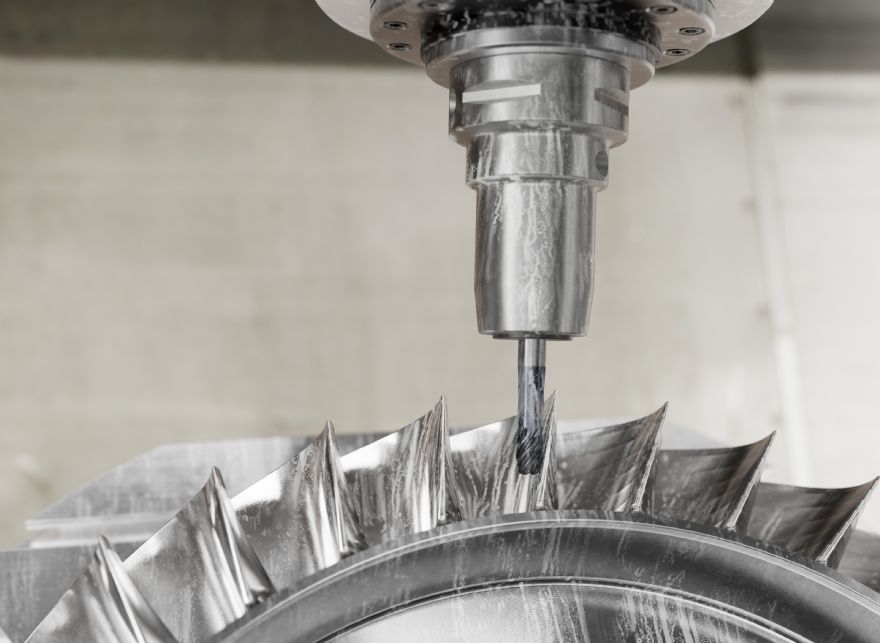
Cutting tool specialist
Sandvik Coromant has launched the CoroMill Plura barrel, a new family of optimised solid end mills designed specifically for profiling applications. This new solution provides high-process security, significant productivity gains and cycle time reductions of up to 90%, making it particularly suitable for the aerospace industry and other high-demand sectors.
Marking a unique addition to a comprehensive range of end mill solutions for ISO S profiling applications, including CoroMill Plura ball nose, CoroMill Plura lollipop and CoroMill Plura conical ball nose, CoroMill Plura barrel offers a new machining principal for profiling tools. Several key features make it the ideal complement to the range, such as a unique one-radius barrel form with up to six optimised flutes.
The CoroMill Plura barrel offers substantial advantages over traditional ball nose machining strategies by using an increased contact radius. This design enables up to a 90% reduction in cycle times by increasing the step-over, which not only enhances machining efficiency by significantly increasing the surface removal rate (SRR) but also ensures exceptional surface quality.
Process reliabilityThe optimised barrel design results in a reduced cusp height between passes, leading to superior surface finishes and lower surface roughness. Despite generating higher forces, the stability and process reliability of barrel end mills make them an ideal choice for achieving precise finishes in demanding profiling applications.
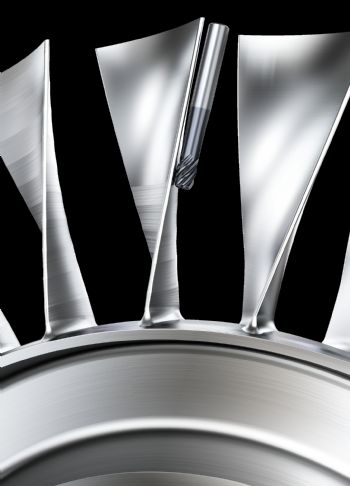
Liam Haglington, Sandvik Coromant’s product manager for solid carbide milling tools, said: “CoroMill Plura barrel excels in applications requiring precision and superior surface quality. Its large cutting edge radius enables increased step-over and reduced cycle times, boosting productivity during high-volume material removal. The large barrel radius makes it ideal for machining large, complex contours and 3-D shapes, while minimising scalloping for shallow depths of cut.
“This tool is particularly suited to demanding applications like aerospace, where parts such as engine blisks involve complex geometries and challenging materials. It also enhances profiling in other high-demand sectors like medical, oil and gas and power generation.”
The tool is available with Sandvik Coromant’s internally developed material-specific grades, including T2CH for titanium alloys and R2AH for heat-resistant superalloys (HRSA), both delivered by Sandvik Coromant’s Zertivo 2.0 PVD coating for improved durability and wear resistance. For customers with specific size and diameter requirements, the tool can be customised through Sandvik Coromant’s Tailor Made service, while the CoroPlus Tool Guide platform can further aid application needs with expert tooling advice.
Mr Haglington added: “Results achieved thus far demonstrate the tool’s reliability and productivity. For a customer machining an inconel engine blisk, a machining strategy with CoroMill® Plura barrel resulted in a cycle-time reduction of greater than 40%. Here, reaching 88min of operation, a 50% increase in tool life was achieved compared to the customer’s existing solution. In another case, this time with a titanium blisk, a customer saved over 90min of machining time when using this product over a competitor’s conical ball nose solution.”
In line with its commitment to sustainability, Sandvik Coromant also offers a comprehensive recycling program for worn-out carbide tools, including CoroMill Plura barrel and other advanced milling solutions. This service allows customers to return used tools for responsible recycling, reducing industrial waste and conserving critical materials like tungsten and cobalt. By participating, manufacturers not only contribute to environmental sustainability but also benefit from a more resource-efficient and cost-effective production process.