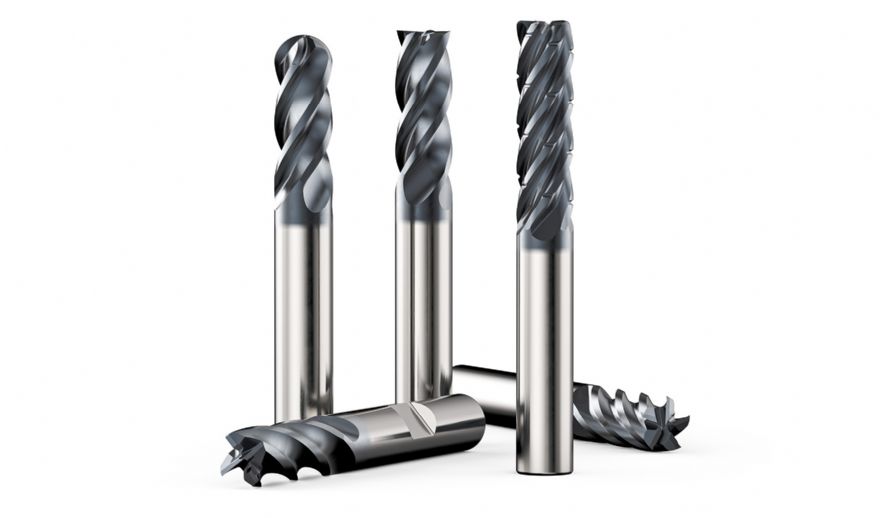
The new
Seco Stabilizer end mills supplied by Alcester-based Seco Tools feature unique flute geometries that achieve the lowest material removal costs in 2-D applications such as slot, pocket and side milling. These geometries also facilitate effective chip evacuation during high-performance machining, while a wear-resistant SIRON-A coating boosts flexibility and tool life.
Seco Stabilizer end mills incorporate geometries that provide unparalleled performance. The series includes four-flute end mills that integrate a continuously varying assymetrical flute geometry, as well as five-flute variants that apply a different helix and rake angle on each flute.
Seco global product manager Rob Mulders said: “The advanced design of these end mills provides exceptional stability in aggressive milling operations. By eliminating harmonics and chatter, Stabilizer end mills work exceptionally well at very high feeds and speeds, resulting in the lowest cost per volume for material removal.”
Created with shaped grinding wheels, the specially designed flute shape on Stabilizer end mills optimises chip evacuation in high-performance machining applications. This boosts process security and enables the use of highly productive material-removal strategies.
Stabilizer end mills also use a versatile SIRON-A wear-resistant coating that allows the tools to be applied across a wide range of applications and materials. The four-flute tools excel in steels and cast iron, while the five-flute variants also provide strong performance in stainless steels, titanium and super alloys. Furthermore, the SIRON-A coating reduces tooling costs by maximising tool life.