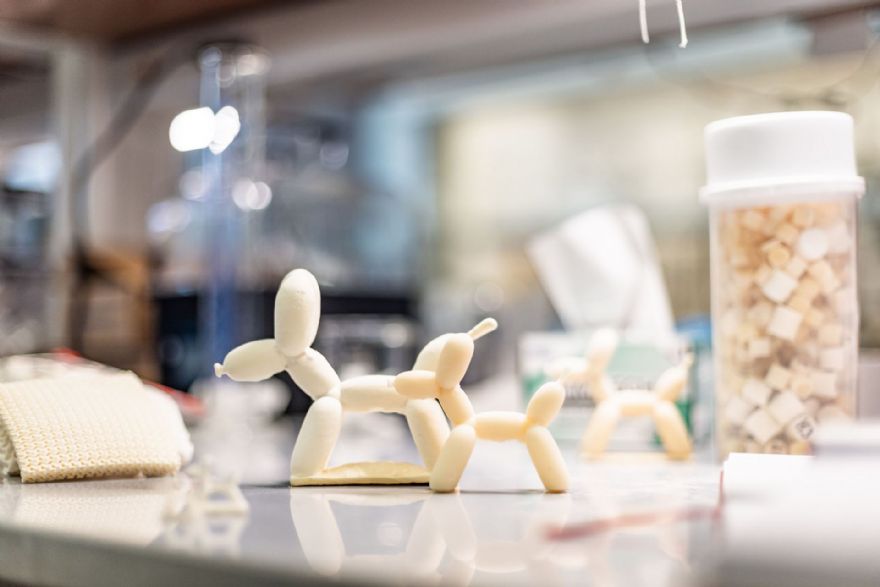
Researchers at the
www.utexas.edu University of Texas in Dallas, who created a 3-D printed foam that is more durable and more recyclable than the polymer foam found in many everyday products, have had their research published in the Royal Society of Chemistry journal
RSC Applied Polymers. Their work focused on creating a sturdy but lightweight foam that could be 3-D printed.
Rebecca Johnson, a UT Dallas doctoral student and the study’s co-lead author, said: “This is probably the longest project I have ever taken part in. From start to finish it was a little over two years, with a lot of time spent trying to get the polymer formulation correct to be compatible with the 3-D printer; and although making new materials that are compatible with 3-D technology is challenging, the 3-D printing process allowed our research team to create complex shapes that could be customised in manufacturing applications.”
Dr Ron Smaldone, associate professor of chemistry and biochemistry in the School of Natural Sciences and Mathematics and the corresponding author of the study, said: “The goal of the project was to address some limitations in 3-D printing in terms of making polymer foam. One of the main uses, or interests, for 3D-printable foams is insulation and shock absorption; and with more research and experimentation, this type of foam and process could be used for high-impact absorption items such as motorcycle or football helmets, car bumpers or armour.
“Moreover, 3-D printing enables the creation of more complex structures, such as fine lattices, which can increase the physical flexibility of the material and provide more versatility for applications.”
The researchers also examined how to make a material that could be 3-D printed into a consistent final product without a lot of defects. “Most commercial foam is thermoset, meaning it undergoes a chemical reaction during moulding, one that permanently locks its structure in place, preventing it from being reshaped, melted or dissolved.
“As a result, most polymer foam cannot be recycled and ultimately ends up in landfill. Our team developed their durable foam using special reversible bonds called dynamic covalent chemistry. Although the foam cannot be completely melted and reshaped like plastic, these bonds allow the material to repair itself when damaged, making it more versatile and longer lasting.”