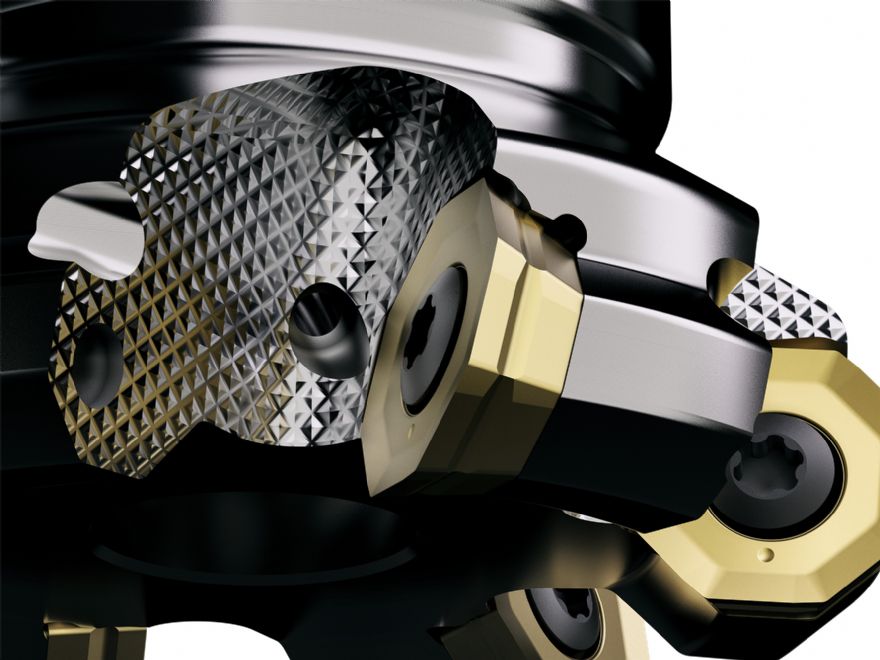
A new generation of the Octomill 06 face-milling cutters from
Seco Tools (UK) Ltd, have been developed to provide significant improvements to ease-of-use, flexibility, and stability. Moreover, Seco says the cutters ensure self-centring of inserts for reliable, error-free positioning and incorporate a multi-insert pocket design that accommodates a variety of insert types for a range of applications.
Tobias Jakobi, a Seco product manager, said: “Self-centring inserts allow operators to quickly and securely position inserts with high repeatability, while the use of a long insert screw enables indexing of an insert without having to remove the screw from the cutter body. Moreover, the cutter-insert interface design disconnects cutting edges from support surfaces and mimics the design of a double-sided insert while keeping the positive setting approach of a single-sided solution.
“This separation of cutting edges and support surfaces keeps worn portions of the insert from damaging or negatively impacting the performance of unused edges — and the self-centring feature prevents an incorrect positioning of inserts, a fault that can cause instability, edge and tool breakage, costly work interruptions, and the need for rework.
“Octomill 06 is a top choice for applications featuring unstable setups or thin-walled parts, featuring a right-handed design with a straight cutting edge, and a high helix angle of +16deg that reduces radial and axial forces. Furthermore, these cutters not only achieve smooth entry and exit but also reduce back-cutting effects while providing consistent wear along the entire cutting edge.”
The multi-insert pocket design of Octomill 06 accommodates face milling, round and moderate high feed inserts, and allows a single cutter body to effectively perform a variety of applications — including face milling, ramping, helical interpolation and profiling. A diverse range of insert grades and geometries provides optimal performance in materials spanning the P, M, K, N, S and H ‘Seco Materials Groups’.