Two Ibarmia machines at Cutting and Wear Resistant Developments LtdCutting and Wear Resistant Developments Ltd, a leading UK manufacturer of specialised downhole tools for the oil and gas industry, has undergone a transformative shift in its production capabilities after investing in a second Ibarmia machine supplied by
C Dugard Ltd. The company, led by managing director Matthew Cooper, has followed a successful growth trajectory over the past 12 years, and the introduction of this latest advanced CNC machine is playing a pivotal role in supporting further expansion.
Cutting and Wear’s unique selling proposition lies in its ability to manufacture tools with a hard-facing aspect and integrate innovative machining processes to deliver comprehensive solutions for its customers. Prior to the arrival of the Ibarmia ZVH 45 L3000 machining centre, the company encountered challenges related to the complexity of its tools, lead time constraints, and the efficiency of its manufacturing methods. However, the implementation of the new Ibarmia machine has revolutionised the company’s operations.
Mr Cooper explained: “In the 12 years I have been here, I have seen many changes, both in the company and the industry, but pleasingly, we have adhered to a successful growth plan, leading us to where we are today — continuing that growth and progressing in the right direction with new machine investments.”
Pictured right: An offshore downhole tool machined on the Ibarmia from DugardThe new Ibarmia machine, equipped with a high-performance spindle capable of reaching speeds of up to 12,000rev/min, has enabled Cutting and Wear to reduce lead times and machining times significantly. Mark Taylor, a CNC programmer at Cutting and Wear, said: “We had one tool that previously took us 11hr to mill, but on the new machine, it has been reduced to just 2hr — a massive improvement.”
One of the standout features of the latest Ibarmia machine is its advanced probing capabilities. By integrating this feature into the machine’s programming cycle, Cutting and Wear have eliminated the need for manual programming, further streamlining the manufacturing process. Mr Taylor explained: “We can execute everything on the machine as it is built into the programme, so there is no need to remove it from the machining centre for inspection, and that is also a time-saver.”
The Ibarmia ZVH 45 L3000 is a five-axis travelling column machine with X-, Y- and Z-axis travels of 3m x 1.2m x 800mm with a B-axis head range of +/-105 degrees. Supplied with an SK40 head as standard or HSK A-63 as an option, the ZVH 45 has a powerful 45kW spindle with 200Nm of torque. Provided with a Fanuc or Heidenhain TNC control, the ZVH 45 L3000 is available with a wide range of options to maximise productivity for the end user.
Offline programmingThe machine’s ‘state of the art’ graphics function has also significantly enhanced the programming experience. Mr Taylor explained: “The graphics have been tremendously improved on these machines. A lot of the programming, I would say 90%, is done through offline programming, and then we have to prove it out here, but with the graphics function on this machine, it makes everything so much easier and reduces errors.”
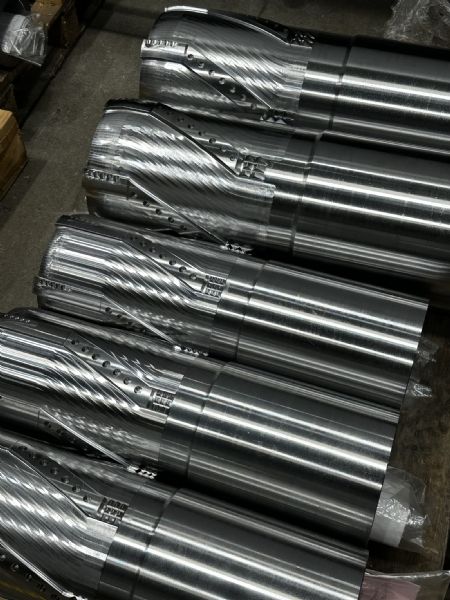
Pictured left: A selection of downhole tools for the oil and gas industry machined at Cutting and Wear
The advanced simultaneous five-axis machining capabilities of the new Ibarmia machine have been a game-changer for Cutting and Wear. This technology allows the machining centre to perform complex, multi-dimensional operations with a single set-up, significantly reducing the need for manual intervention and enhancing overall efficiency. Mr Taylor, highlighting the initial challenges faced by the team in adapting to new technology, added: “It was a learning curve because it has a simultaneous head. We do have machines quite similar to it, but this one is a lot quicker.”
Mr Cooper continued: “Not only has the new Ibarmia machine changed our manufacturing methods, but it has also shifted the mindset of our machinists who have completely embraced the new technology, flipping their approach to the manufacture of downhole tools. The machine’s advanced features — including its high-speed spindle, integrated probing, and ‘state of the art’ graphics — have allowed Cutting and Wear to achieve notable improvements in accuracy, speed, and programming efficiency.” These enhancements have directly contributed to the company's ability to meet the growing demands of the oil and gas industry.
In addition to its technical capabilities, the strong partnership between Cutting and Wear and Dugard has been instrumental in the success of this investment. Mr Cooper concluded: “Dugard came in, worked with us very closely, understood the tools we wanted to produce, and from then on, simply matched us with the appropriate machine. So it is a well-suited relationship, and the machine is doing precisely what Dugard promised it would.”