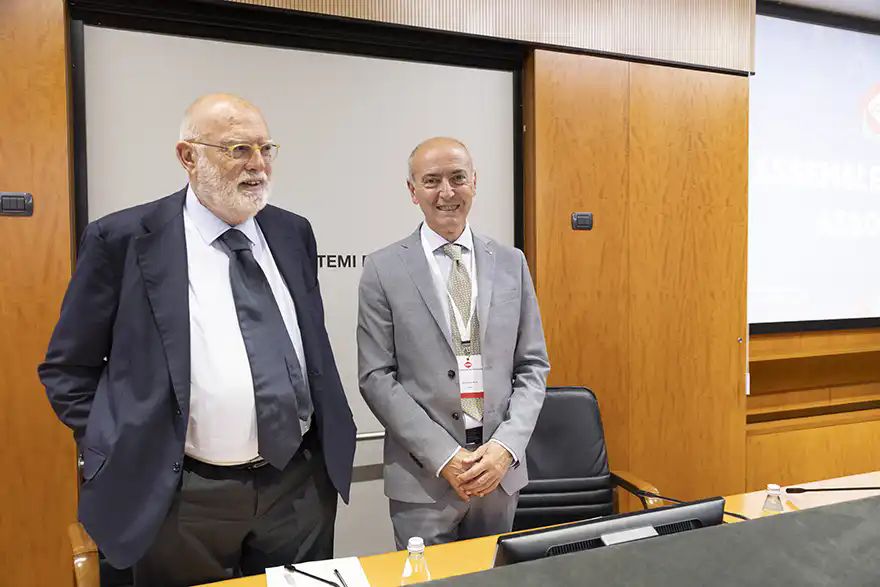
Last year turned out to be extremely challenging for the Italian machine tool companies and providers of robots and automation systems, which experienced a big drop across all economic indicators. The only bright spot was the export market which recorded a moderate increase. Nevertheless, Italy remained as one of the main players on the international stage, where it ranked fifth in the world for machine tool production and fourth for exports.
Forecasts for 2025 indicate a slight improvement compared to 2024, although the expected results are not great. This is, in brief, the picture illustrated by the president of
Ucimu-Sistemi Per Produrre, Riccardo Rosa, during the Members’ Meeting, which was also attended by Antonio Gozzi, the president of
FEDERACCIAI (Federation of Italian Steel Companies).
According to the actual data processed by the Economic Studies Department and Business Culture Centre of Ucimu, in 2024, the Italian production of machine tools, robots and automation systems amounted to 6,327 million euros — a significant 16.9% reduction on 2023. The outcome was due to the heavy reduction in the deliveries of Italian manufacturers on the domestic market, falling by 39.5% to 2,054 million euros, weighed down by the collapse in domestic consumption, which did not exceed 3,707 million euros (36.3% less than in the previous year). Imports also suffered, standing at 1,653 million euros (-31.8%).
A different performance was highlighted by Italian companies in export markets, as confirmed by the data of exports, which moderately grew by 1.2% to 4,273 million euro, achieving a new record for the sector.
Main export marketsIn 2024, the main export markets for the Italian product offering were: the USA (629 million euros, +10.9%), Germany (365 million euros, +1.6%), China (240 million euros, -16.3%), France (204 million euros, -17.6%), Turkey (190 million euro, -10.3%), India (185 million euros, +58.3%), Mexico (176 million euros, -9.9%), Poland (169 million euros, -21.5%), Spain (157 million euros, +21.1%), Sweden (92 million euros, +71.4%).
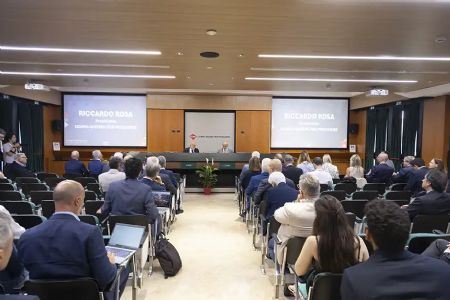
A decrease was also reported in the utilisation rate of production capacity, whose annual average changed from 86.2% in 2023 to 77.3% in 2024. The same trend was also recorded with regard to the order portfolio, which stood at 6.5 months of guaranteed production versus 7.3 months in the previous year.
As shown in the forecasts provided by the Economic Studies Department & Business Culture Centre of UCIMU, in 2025 the Italian machine tool, robot and automation industry should experience a slight recovery. All indicators should return to positive territory, but the increases are likely to be extremely small. Production should reach 6,490 million euros (+2.6%). Exports are expected to grow again (+1%) and achieve a new record of 4,315 million euros.
Deliveries on the domestic market should increase again (+5.9%), accounting for 2,175 million euros, supported by the slow recovery of domestic consumption, which will should rise to 3,910 million euros (+5.5%). Imports should also show a positive sign, attaining 1,735 million euros (+4.9%).
Improving competitivenessAt his first Members’ Meeting, Riccardo Rosa, president of UCIMU, said: “After a complicated 2024, this year should give us more satisfaction, but now more than ever, we must use the conditional mood, considering the succession of really worrying phenomena, from trade to military wars. All this makes our work more difficult and requires companies to make a great effort to improve their competitiveness. To do this, we must keep on investing in innovation, contextual knowledge and professional training.
“Thanks to interconnection, data management, sensors, remote vision and control systems and artificial intelligence (AI), ‘state of the art’ machine tools are real enablers of the digital and ‘green’ transformation of factories. We are proud of how much and how our little world, mainly made up of SMEs, has contributed to the advancement of the Italian manufacturing industry, but we are aware that this development was also possible thanks to the 4.0 and 5.0 measures that supported and stimulated the market.
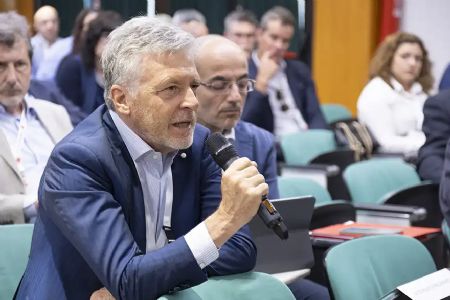
“In a crucial moment like this, with extremely weak domestic and foreign demands, incentive tools measures are indispensable to support the progressive and necessary change. Another reason is that Germany, our first point of reference in Europe, will soon have a plan to support and relaunch its industry.
“If the German locomotive restarts, we — at the first wagon of this train that has never stopped until now — must be ready and remain coupled to it, in order to be able to continue working in the production chains of Made in Germany, which, leaving aside the issue of tariffs, travels on very long routes, distributing our production all over the world.”
Mr Rosa continued: “We urge our government to take immediate action on Transition 5.0 this year, in order to have an extension of its applicability beyond the deadline. But if it were not possible, we ask at least to convert the still available funds into new measures. In this connection, we consider it is necessary to reflect, as of now, on the national policies that will have to accompany the development of the industry from 2026 onwards.
“Based on experience, we believe that structural measures are needed to enable companies to plan their investments with confidence, thus avoiding unsustainable work peaks for Italian manufacturers, who specialise in production to order. Indeed, all too often, SMEs risk losing orders, even important ones, because the lead time of a super-customised product like ours does not ensure delivery within the timeframe envisaged by the incentive, which benefits imports, among other things. It is substantially a double damage.”
Much-dreaded tariff policyWith regard to the context, there are two big questions that European companies must ask themselves: “What will happen or what do we want to happen to the automotive production Made in the EU and all its suppliers and satellite activities? And what will we do about the much-dreaded tariff policy that could trigger a domino effect on all areas of the world?”
Mr Rosa added: “Regarding powertrain electrification once again, we stress the need to enforce the principle of technological neutrality. Not least because the sustainability of this transition process must take into account not only the environmental impact, but also the economic and social consequences. As European entrepreneurs and citizens, we know very well that the interest of young people in cars is infinitely lower than that of previous generations, but we are deciding to leave our entire market to Asia and we are risking the desertification of a fundamental part of the Eurozone economy, a premise for the impoverishment of the population. This cannot happen.
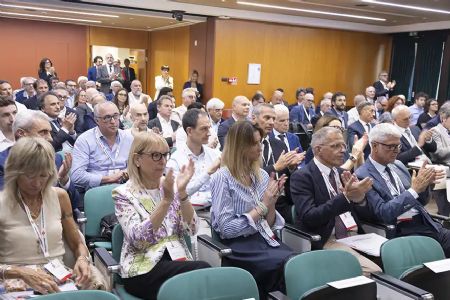
“New EU policies are needed to accompany the reconversion of plants toward different types of production. Moreover, the funds and development plans for rearmament, defence and aerospace can indeed give new impetus to the Eurozone industry but, in these sectors, one should not improvise. Entering the galaxy of big players in these worlds means undergoing strict evaluations and certifications. The requirements often represent a significant hurdle for many small and medium-sized companies right from the start.
“Talking about tariffs, the USA were our first export market in 2024, with more than 600 million machines sold. Our products are very appreciated and US factories need to import machines, as their domestic production is not sufficient to meet demand. For this reason, we can assume that entry tariff barriers will not be particularly penalising for us. A more problematic issue could be the indirect effect of tariffs on products in whose supply chains we are involved.”
Uncertainty“On the other hand, what is extremely penalising is uncertainty, the real deterrent to investment in production technology, whether linked to the trade war long threatened by President Trump or, even worse, linked to instability in the Middle East.
“All this proves how geopolitics has now forcefully entered our daily lives and the activities of our enterprises. We all must get ready to learn how to read the change and interpret the events through exchange of views and dialogue with colleagues, institutions and also by relying on the representative organisations to which we belong.”
Mr Rosa said: “We must invest in the professional training of our staff and of young people, who are the future of our companies. ‘State of the art’ machines need people capable of managing, programming and using them. Therefore, UCIMU has strengthened, and will do so even more in the future, its commitment to UCIMU Academy, a project that concerns all the initiatives dedicated to reducing the mismatch between job demand and supply.
He concluded: “These include the development of partnerships with high schools, universities, ITS (Higher Technological Institutes) Academy Foundations related to the world of metalworking, talent hotbeds for our factories.”