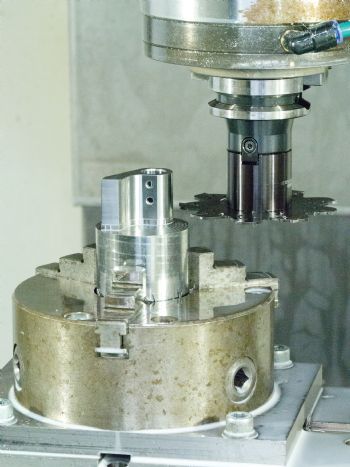
By using Horn Type M101 disc milling cutters (
www.phorn.co.uk), precision engineering company SRD Engineering Ltd has gained significant improvements in part-off/cut-off operations, reducing overall cycle times per component by around 10min.
In addition, the inserted-carbide tooling can process large quantities of components before the inserts need to be changed, whereas an HSS saw required re-sharpening after each component.
Moreover, a single insert geometry and coating combination can be used on a wide variety of exotic materials, rationalising the requirement for different geometries/coatings for different material specifications.
Family-owned and based in Bicester for 23 years, SRD has profited from an ‘open door’ policy regarding tool try-outs; the company has also been a regular investor in high-performance machine tools and equipment — a necessity given the variety of ‘difficult’ materials that it processes, including stainless steel, titanium and Inconel, as well as other ‘exotics’.
The company specialises in high-precision machining for applications ranging from medical to agricultural and motor-sport to satellites — typically in batches of 10 to 100-off.
Confirming SRD’s success was its move to new premises in 2014, followed earlier this year by the acquisition of an adjacent factory unit that doubled the overall shopfloor space. The use of the Horn Type M101 disc milling cutter has played a significant role in this success.
An in-house ‘contest’ to improve on the performance of HSS slot-cutting saws saw the Type M101 demonstrate substantial superiority over inserted-carbide disc mill solutions offered by other well-known tooling brands.
Key advantages include the design of the cutter body/blade, which allows machining close to the job/material interface. Moreover, the inserts are designed to generate low positive cutting forces, thereby allowing the cutters to be used across a wide variety of exotic materials.
Further flexibility of application is provided by the availability of S101 inserts in 1.6 and 2.0mm widths.
SRD milling team leader Chris Bryant says: “The types of component for which we use these cutters are machined from a billet mounted in a vertical machining centre with a fourth-axis table. Using the disc milling cutter allows almost complete machining, whereas previous tooling options produced a compromised finish on the part-off face and required lengthy cycle times.”
Cutting data for the 128-tooth HSS tooling was 75rev/min, with a feed rate of 8mm/min. By comparison, the 100mm-diameter nine-insert Horn Type M101 operates at 378rev/min and a feed rate of 68 mm/min, which gives a cutting speed of 120m/min and 0.02mm feed per tooth.
Each cutting edge is provided by a single-ended Horn S101 insert, located and secured by a quick-change self-clamping system. Moreover, the 2mm-wide sintered insert incorporates a moulded chip-breaker and is available in a variety of grades and coatings.
SRD machinist Michael Reading noted from the off that the S101 insert was a well-developed product. “One of its notable qualities — and one that you associate with a smooth, efficient cutting tool — is the sound it generates. Another positive feature is the flat surface provided by the assembled tool, so that minimal preparation of the cut face is needed for further machining.”