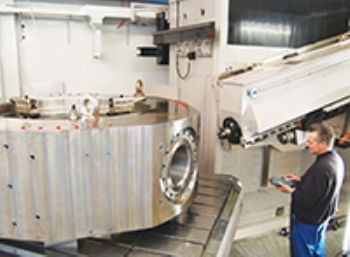
Mollart Engineering’s in-house-developed five-axis bed-type combination deep-hole drilling machine/machining centre is undertaking large-component production at its Chessington headquarters and sub-contract machining operation (
www.mollart.co.uk).
Weighing in at more than 22 tonnes, the Mollart Prismabore machine provides a single-cycle production capability that combines milling sequences on components weighing up to 8 tonnes and requiring deep-hole drilling and boring.
Typical components being machined are multi-feature Inconel and titanium parts that incorporate extended-depth cooling holes and milled features on complex mould plates.
Mollart’s sub-contract operation supplies the semiconductor, nuclear, aerospace, medical, metrology, oil and gas, telecoms, sub-sea and special-materials industries, and most parts produced present new challenges relating to feature relationships, geometry, tolerances and material types.
Indeed, the deep-hole capability spans gun drilling, BTA drilling, ejector drilling, trepanning and special tooling applications in diameters from 0.5 to 410mm using high penetration rates while maintaining high orders of roundness, concentricity and straightness for bores up to 3,000mm deep.
The Mollart Prismabore has a 1,250 x 1,250mm B-axis rotary table and axis strokes of 2,000mm in X and 1,000mm in Y; a ram-type slide provides a Z-axis stroke of 800mm, while a fully independent U-axis governs the penetration of the gun drill to a depth of 1,500mm.
The ISO 50 machining-centre spindle is powered by an 11kW 6,000rev/min motor and supported by a 20-tool magazine with a swinging arm tool changer. Both the milling and drilling spindles are controlled by a single Fanuc 31i Model B unit.
The 11kW gun-drill drive has a two-speed gearbox to give either high speed or high torque — depending on the application. Comprehensive tool monitoring is used to protect tooling and components, and there is a refrigerated 80-bar coolant supply to both spindles (a sub-micron Micromag filter unit is incorporated in thecoolant circuit). The X, Y and Z axes feature Heidenhain glass scales.
Previous examples of Mollart’s ability to combine deep-hole drilling and conventional machining-centre-type applications within a single cycle include its five-axis Centreplex (pictured), which can incline (tilt) both the
gun drilling and milling spindles by 15deg (the spindles are mounted under/over — shotgun style).
This arrangement allows compound-angle features to be machined in cycle in conjunction with the rotary table.
In one particularly challenging application, Mollart had to produce 36 compound-angle oil-feed porting holes 20mm in diameter to individually specified depths in a 7.5 tonne nickel chrome steel forging for a marine bearing, which also required the taper thread milling of 30 holes to 3/4NPT.
The machining concept used by Mollart allowed it to produce the part in under three days.