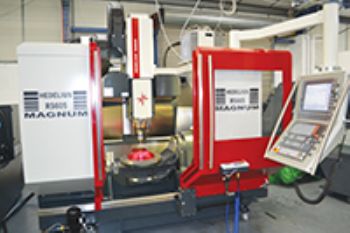
While researching five-axis capability, Mark Newcombe — director of the Plymouth-based wax injection and mould tool manufacturer Tooltech Ltd (
www.tooltech.co.uk) — discovered that a job similar to one taking two days to complete on one of his company’s three-axis machines was being done in 25min on a five-axis machining centre.
“Also at that time, we produced a tool using 10 set-ups on the block, as it had some extremely complex features on it. We took three weeks to manufacture this tool; a five-axis machine programmed using Edgecam software’s five-axis module would have completed it in a week — with only three set-ups.”
Tooltech designs and manufactures wax pattern tooling for the investment casting industry, along with all the auxiliary tooling required for a full tooling suite; this includes cut-off and power-grind fixtures, along with all types of CMM fixtures required for the power generation and aerospace products.
“Customers come to us with a part model, and we design and manufacture the tooling for them. We have a good reputation for solving all issues regarding how to structurally manufacture the tool.”
Tools range from a 1.8-tonne aluminium mould tool that is 1.8m long x 800mm wide, to those just 50mm square. The average wax pattern tool is around 1.2-1.3m long. Tooltech’s first five-axis machining centre — from the
German company Hedelius — joined eight three-axis Taiwanese YCMs and Bridgeports in a recently extended 6,600ft2 factory.
These are used to produce large wax pattern dies, along with all the gating and auxiliary tooling.
Most of the company’s contracts are for aluminium wax pattern tools, which are either hinged or straight-lift types, producing a wax pattern of the casting that eventually goes into an engine. “Using the investment casting process means we get perfect definition in the wax to turn it into the casting.
“Because we are in a niche market, we had to expand, both in terms of increasing the size of our factory and adopting five-axis machining. Customers are demanding more and more work from us, and we need to respond quickly. The only way we could manufacture the tooling was to work extremely long hours.
“Now, we are saving so much time with Edgecam’s five-axis tool-paths and the Hedelius.”
The customer model of the component that the tooling is required to make is loaded into Tooltech’s CAD system, and Mark Newcombe’s son Andrew designs the tooling around it. Once the design and assembly are approved, he imports parasolids into Edgecam (
www.edgecam.com).
“We also make the jig plates for holding the components, so they are imported too; Edgecam then does the full programming for everything.”
Mark Newcombe says that CAM engineer Lance Jobe generates the programs, along with tooling sheets and information for the shopfloor. “Tooling is usually produced from aluminium, sometimes with brass slides, while a lot of fixtures are stainless steel.With Edgecam being easy to use, this does not cause any problems.”
He says Edgecam is a fully integral and invaluable part of Tooltech’s manufacturing process, adding that its five-axis capability brings numerous additional benefits — for example, reduced cycle time by machining complex components in a single set-up. In addition, dimensional accuracy can be significantly improved through the elimination of positioning errors between set-ups, while improved surface finish and extended tool life are achieved by orienting the tool to maintain optimum tool-to-part contact at all times. Meanwhile, improved access to undercuts and deep pockets by tilting the tool or component allows shorter tooling to be used, thereby eliminating the need for secondary set-ups; and because a cutter can be presented to the component at any angle, fixturing requirements can be significantly reduced.
Because Andrew Newcombe has operated CNC machines, he takes CAM requirements into consideration when designing the tools in CAD. “The only issue we had was trying to machine undercuts. That is why five-axis is so important for us. It means we no longer have to turn the block for another set-up.
“Once Andrew completes the design with CAD, we are 100% confident that Edgecam will produce it accurately, economically and fast. I promote our services to customers by showing them we have a five-axis CAM system that can manufacture anything they ask us to.” Programs are created using a bespoke post-processor that runs all Tooltech’s machines, including the latest five-axis Hedelius. “The advantages of running a bespoke post are huge in terms of preventing errors. The one post is written for all our machines, so we have no variables.”