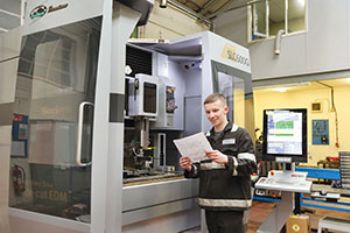
Oldbury-based Voestalpine Metsec plc (
www.metsec.com), the UK’s largest specialist cold roll-forming company, has acquired a new Sodick SL600G CNC wire erosion machine from Coventry-based Sodi-Tech EDM Ltd (
www.sodi-techedm.co.uk).
The machine was chosen because it has the ability to use lower-cost wire and consumables than the 15-year-old EDM (from a different manufacturer) that it has replaced.
The Sodick, with its linear-motor drive technology, is also allowing the company to cut workpieces some four-times faster, thus quadrupling capacity.
As a specialist in the provision of cold roll-formed products to industries that include construction, yellow goods, sustainable energy, storage, transportation, office furniture and marine, Metsec, which has been part of the Austrian-headquartered Voestalpine group of companies since 1998, today has 380 employees and an annual turnover of around £85 million.
Technical manager Peter Richards said: “We acquired our first wire EDM for the tool-room around 15 years ago. Late last year, we reviewed how much the spare parts, repairs and down-time were costing us. Together with the fact that the machine required the use of expensive wire, and that we could only achieve relatively slow cutting speeds, we decided to put in a capital expenditure request for a replacement machine.
“Because the new machine can run using conventional lower-cost brass wire, the cost of consumables has fallen by 50-60%. Furthermore, the Sodick linear drives mean that we can run up to four-times faster, thus quadrupling our capacity. The machine also has a larger bed than our previous model, which allows us to load multiple jobs simultaneously for unmanned running at the weekends; 20kg wire spools can be accommodated to ensure extended periods
of ‘lights out’ operation.”
Installed at the end of July, the SL600G runs almost constantly, producing tooling such as press tools, die sets, cut-off tools and blades, typically from D2 tool steel. Although the tools are complex and call for tight tolerances and high surface finish, these requirements are well within the capability of the Sodick SL600G.
Mr Richards added: “We’re extremely pleased with the performance of the machine. Jobs that would previously require two or three days of cutting time can now be completed within a day. This has created a lot more capacity and allowed us to recall many jobs that were previously subcontracted, saving yet more cost.”