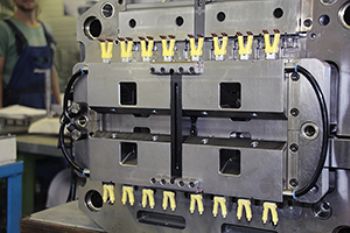
Toy manufacturer Playmobil (
www.playmobil.co.uk) releases many new figures every year, and this places high demands on the company’s in-house mould-making shop.
To ensure maximum machine efficiency, its numerous machining centres use LaserControl measuring systems from Blum-Novotest Ltd, Burton on Trent (
www.blum-novotest.com).
While Playmobil figures are designed for creative play, they rely on the use of high-tech engineering in their design and production. They incorporate a number of parts that are designed to precisely match their mating component. For example, when a hand is rotated in an arm, a specific torque has to be applied to ensure that it does not rotate back. This requires all components to be manufactured with an appropriate degree of precision.
Furthermore, the mouth and eyes are not printed on. The head is injection-moulded from two different-coloured plastics, in a complex process whereby the brown plastic eyes are injected into precision-fit recesses in the head blank. As a result, the demands placed on the mould-making process are very high.
A total of 77 designers and technicians are working continuously to produce new figures and sets, for which new injection moulds have to be made. Attila Britting, head of the in-house mould-making shop, says: “We require as many as 1,200 new moulds a year, of which some 45% are made in-house. To increase our in-house capacities, our mould-making shop was relocated last year to a new building that quadrupled our size, allowing us to undertake more injection moulding in-house.”
Playmobil aims to ensure that its moulds produce finished plastic items that require practically no reworking; this is vital when one considers that the company makes about 10 million parts a day and over 100 million figures a year. Consequently, mould separation must be a high-precision operation which ensures that no burrs occur on any part or the finished figure.
For two-colour items such as the legs, onto which different-coloured shoes are injection-moulded, it must be ensured that the shoe mould precisely fits the pre-moulded legs and that no gaps appear after the plastic cools. Additionally, moulds are specified for extremely high volumes — some 200,000-300,000 pieces — without the need for attention.
Several of Playmobil’s machining centres are fitted with pallet changers and tool magazines that can accommodate up to 120 tools. Marco Mendl (CAD/CAM/NC team leader) says: “The machines even keep running unmanned over the weekend; that degree of automation would not be possible without the Blum laser systems fitted to our nine automated DMG five-axis machining centres.”
The laser automatically measures the length and radius of the tool prior to machining; after machining, it checks for breakage and wear. This saves operators having to pre-set the tool in a pre-setting device. A new tool is simply shrink-fitted into the holder and measured at machining speed after fitting. This ensures that the tool data in the machine is correct, and that numerical errors or mistakes from misreading data can no longer occur.
Other features include high-speed automatic compensation for the thermal expansion of the complete machine and for spindle displacement. “Five years ago, I would have said it is impossible to incorporate the complete tool measurement process in the machine, but now it works like a dream,” says Mr Mendl. “The accuracy of the LaserControl system is also astounding; based on our experience, it is repeatable to less than two thousandths of a millimetre.”
Without a monitoring system to detect worn or broken tools, automated production cannot be implemented. At Playmobil, as many as four examples of each key tool are held in the tool changer, so the automated overnight jobs can be run with a high level of reliability.
“High-chrome steel is mostly used, because it wears less when injection-moulding large quantities. However, it does cause considerable tool wear during cutting, which is why it is necessary to keep an eye on the running times of the individual tools. The Blum laser measuring systems enable us to do that.”
To protect the laser’s optic from being soiled, the measuring system is mechanically sealed off from machine coolant by a pneumatically operated shutter during machining. The rotating tool is also cleaned with compressed air prior to measuring, to ensure that the measurement is not influenced by swarf, dirt or coolant.