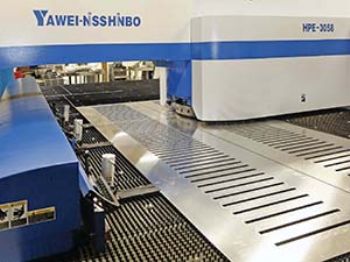
A servo-electric CNC turret punch press built by Yawei-Nisshinbo has raised productivity dramatically at the Cannock factory of Weldall Architectural Fabrications (
www.weldall.co.uk) — a sub-contractor best known for its high-end work in the building industry.
Supplied by the machine manufacturer’s sole agent, Tamworth-based Press & Shear Ltd (
www.pressandshear.com), the machine cost considerably less than equivalent models on the market and was the first of its type to be installed in the UK, following its certification for use in Europe.
Incorporating technology from premium turret punch press manufacturer Nisshinbo, Yawei turret punch presses are manufactured at its 160,000m2 facility in Jiangsu Province, China, using high-quality components from Japan and Germany. The company produces some 3,000 machines a year.
Jointly owned by Andy O’Farrell and Alan Blower, Weldall was established in 1988 and originally specialised in welding exotic materials such as titanium, nickel alloys and stainless steels for a range of industries including oil, gas, defence, cryogenics, nuclear and medical.
In 1992, its work centred on producing prototypes for the BR90 project — a family of bridges built from aluminium alloy for the British Army. During this period, the fabricator was sub-contracting out its sheet metal-working but decided to bring it in-house, installing its first press brake and guillotine following the acquisition of a supplier.
By the time the BR90 project came to an end in the late 1990s, Weldall had been planning for the transition and had entered the building and architectural sectors. Work in these industries continued side-by-side with other general
fabrication projects.
Mr O’Farrell says: “We are now best known for this work, particularly the manufacture of high-quality fabrications, bracketry and aluminium flashings for curtain walling — at competitive prices and with short lead times.” Over the past six years, the founders’ sons — Matt O’Farrell, Gareth O’Farrell and Ryan Blower — have all joined the company. The family-run firm set about increasing its architectural business, which resulted in a succession of prestigious contracts.
An early success was supplying the builders of Quebec House (a development of 252 one- and two-bedroom units in Kingston-upon-Thames) with 2mm-gauge aluminium pods to finish each of the windows. Other significant projects include a weather-beater wall for Guy’s Hospital in London, new aluminium detail for the upgrade to the pier in Weston-super-Mare and window reveals for the Hilton hotel at Heathrow’s Terminal Five.
During this time, Weldall was using a six-station CNC turret punch press equipped with a manual tool change carousel, which meant that a lot of operator intervention was needed and non-productive time was high. The company began looking for a replacement machine.
“The Yawei-Nisshinbo servo-electric punch press was the obvious choice, due to its high specification and competitive price,” said Mr O’Farrell. “The use of thick-turret tooling means that we will be able to produce accurate components on the machine for many years to come. Additionally, the optional 5m length capacity of the brush table is more than enough for our needs, as we have standardised on 4 x 1.5m sheet”
Since it was installed in November 2014, the Yawei-Nisshinbo HPE-3058 punch press has fulfilled numerous contracts, and three sporting venues have been refurbished using the subcontractor’s components — the training ground at Chelsea FC, and the rugby union clubs of Leicester Tigers and Northampton Saints. Also recently completed was a 12m-long lion logo for the wall of Birmingham University. It was designed in SolidWorks 3-D CAD and produced in sections from 3mm J57S anodising-quality aluminium.
Meanwhile, nearly 6 million 5.5mm-diameter holes have been punched through 2mm-thick stainless steel for the production of engine intake louvres to protect military vehicles used in UN peace-keeping missions. A special punch-and-die set was sourced from Wilson Tool; this featured an Optima Coating on the punch, which greatly extends tool life by increasing the hardness of the tool.
A current project involves feature panels for student accommodation in the Eastside Locks area of central Birmingham. This project requires the manufacture of over 1,000 grilles from 3mm aluminium.
In conclusion, Mr Blower said: “Our use of the new punch press, coupled with the purchase of Jetcam software — also through Press & Shear — has resulted in an increase in productivity. The parts we now manufacture are more accurate than we could previously produce, so our customers do not have to worry about on-site fit-up. As a consequence, we have been able to win a lot of new business — and retain existing customers.”
Weldall is currently being assessed for compliance with EN 1090 Parts 2 and 3 — the European standards that regulate the fabrication and assembly of steel and aluminium structures for the construction industry. The company hopes that these standards will be in place early this year.