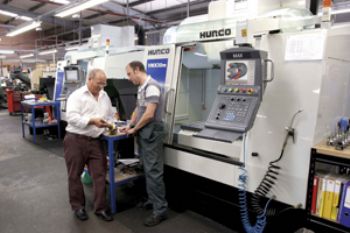
There are a number of purpose-built five-axis/five-sided machining-centre designs on the market, including types with a rotary table and either a trunnion support or a swivelling B-axis head to provide the fifth CNC axis.
Many companies — including High Wycombe-based Hurco Europe Ltd (Tel: 01494 442222 – www.hurco.co.uk) — supply such machines, but neither configuration suited Brunswick Tooling, Brighouse, which manufactures reamers and special cutting tools (both solid-carbide and indexable-insert types). Instead, it asked Hurco to supply an alternative five-axis configuration, based on a three-axis VMX30m machining centre fitted with a two-axis NC tilting rotary table.
Many machinists regard such a solution as inferior to a custom-made five-axis machine, sometimes referring disparagingly to a lack of rigidity associated with ‘bolt-on attachments’. However, for making Brunswick Tooling’s products, which are essentially rotational components, the arrangement has proved to be optimal.
The rigidity issue was tackled at the outset by selecting a Kitagawa TT182 hydraulic two-axis table with a -35/+110deg tilt angle and a table rotation of 360deg. According to Brunswick Tooling’s managing director, Paul Briggs, the attachment is so robust that machining performance is just as good as that of purpose-built five-axis machines. Indexing accuracies of 20 and 60arc-sec respectively for table rotation and tilt, together with 4arc-sec repeatability, ensure top precision metal-cutting when combined with Hurco’s ±0.005mm linear positioning accuracy and ±0.0025mm repeatability.
The real advantage of this particular machine configuration is that Brunswick Tooling can clamp the rotary table in its vertical position and fit a tailstock to the left-hand side of the machine bed. In this way, the tools that it manufactures can be positioned between centres and clamped securely for prismatic machining operations to be carried out (such as the milling of indexable-insert pockets).
Complex features

The first Hurco machine installed at Brunswick Tooling (in March 2010) has been operated in this mode for a large part of the time. However, the tailstock is removed for certain jobs, and the Kitagawa table is inclined upwards, to position the component at a compound angle for the three-axis machining of complex features on some tooling products. Both rotary axes are currently used in this way (indexed and clamped), but they could be interpolated with the linear axes in future, as the Hurco Max CNC system can control full five-axis cycles.
It was the flexibility of being able to use the machine either in turn-mill mode or as a five-sided/five-axis machining centre that convinced Mr Briggs to choose the Hurco/Kitagawa option. The merits of the decision were underlined by the purchase of a second, identically equipped VMX30m one year after the first. Even the tools in the magazines are identical. Programs are stored on the factory server, allowing any job to be downloaded to — and produced on — either Hurco machine, with certainty that the most up-to-date cutting cycle is being used.
Mr Briggs said there is a particular functionality within Hurco’s WinMax conversational programming software that lends itself well to five-sided machining applications, during which the part is tilted upwards at an angle. The function is called ‘transform plane,’ and it is used in a rotary program to re-establish part zero to any plane for non-rotary three-axis milling or drilling. This facilitates the machining of repeating features on several sides of a component, as the tool automatically moves so that it is always perpendicular to the transformed plane.
Mr Briggs says: “Essentially, whatever angle the part is at in one or two rotary planes, the Hurco software always knows where the datum is, allowing us to increase productivity on complex, high-added-value products.”
Five-axis programming
His lead machine tool programmer, Andrew Bell, also commented on the software. “With WinMax, it is easy to program a part without any need for a costly five-axis CAM system. We take the DXF file from the 3-D model we create in Autodesk Inventor and load it directly into WinMax. The data is then used to generate the cutter paths using conversational routines, quickly and accurately, without the risk of introducing G-code errors.”
Mr Bell, who uses WinMax software daily, says he also likes the way a graphic of the part being programmed is generated concurrently in background, thereby allowing any potential errors in component geometry to be spotted quickly. “This is especially useful when programming a cylindrical part, which is difficult to visualise from a 2-D drawing.”
Brunswick Tooling manufactures reamers in batches of up to 300 for world markets, but its special cutting tools are normally produced in ones and twos, for which WinMax software is ideal. Often, the company is asked by firms to design and produce a tool from scratch — from a CAD drawing of the end component. Customers include Ford, JCB, Airbus, Agusta Westland and BAE Systems, from which it recently received the Chairman’s Silver Award for reducing the lead time for a Joint Strike Fighter titanium machining operation from three days to 5min.
In conclusion, Mr Briggs says: “The Hurco machines are good value for money and have a large working area for the factory space they take up. Their accuracy is fantastic; we easily hold 50µm on indexable insert pocket dimensions and position, despite sometimes machining a long component held at one end. We still operate a number of universal four-axis tool-room machines that have a manually tilting table and require long-hand G-code programming. They will continue to have their place for manufacturing reamers and some repeat special tools, but for particularly complex tooling designs, which are becoming more and more frequent, the Hurco/Kitagawa configuration is the future for our business. Avoiding expenditure on CAM software and an operator to use it is an added bonus.”