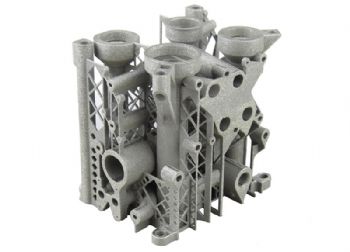
The fact that additive manufacturing (AM) is highly suited to the design and manufacture of manifolds — due to its ability to build internal features and passageways — was highlighted by a recent project that saw Renishaw (
www.renishaw.com) collaborate with a customer to redesign a hydraulic manifold block with the aim of reducing the mass of the component while retaining its robustness.
Furthermore, with the increased design freedom associated with AM, the two companies knew that they could also increase the efficiency of the flow-paths within the redesigned manifold.
Renishaw says that its customer traditionally makes hydraulic manifold blocks from an aluminium alloy or stainless-steel billet, which is first machined to size and then drilled to create the flow-paths.
Specialised tooling is often needed, due to the complex drilling that is required, and some passages need blanking plugs to direct flow through the system.
The nature of this manufacturing process results in abrupt angled junctions between flow-paths, which can cause flow separation and/or stagnation — a major contributor to efficiency loss.
Aluminium alloy manifolds are generally less costly, due to lower material costs and ease of machining, but because they have a low resistance to abrasion, any loose particles in the flow will wear the internal surfaces.
For this reason, stainless-steel manifolds are sometimes more desirable, but the material’s higher density and hardness compared to aluminium mean that stainless-steel manifolds weigh more — and cost more to machine.
Regarding the benefits offered by AM when designing and manufacturing hydraulic manifolds, Renishaw highlights a number of factors, including: optimised flow-paths via the use of computational fluid dynamics (CFD) for more-efficient functionality (improvements in flow efficiency of up to 60% are readily achievable); a reduction in the requirement for fixturing during manufacture; a significant weight reduction (up to 79%); and a more compact product.
The customer gave Renishaw certain design and function guidelines that had to be considered when redesigning the component. The first step was to de-construct the part into just the essential passageways that dictate the manifold’s function.
The flow-paths of the original cross-drilled design were extracted using CAD software, and any drilled areas not required for the flow-path were removed to leave only the essential flow network.
Each hydraulic circuit was then reduced and simplified in preparation for CFD analysis using SolidWorks Flow Simulation. Next, the flow-paths were optimised after identifying areas of flow separation and stagnation, then the appropriate wall thicknesses (based on the customer specification) were added (this could have been done by using finite element analysis — FEA — stress modelling based on pressure readings taken during CFD analysis).
Finally, permanent support structures were designed and added to the CAD geometry, creating a self-supporting and hydraulically efficient structure.
The manifold based on this first design iteration resulted in a reduction in material volume of 52% compared to the original block manifold, as well as improvements in flow efficiency of up to 60%.
The original block manifold was designed so that multiple units could be installed in series; and because individual hydraulic block manifolds occasionally need to be removed for servicing, it was necessary to include threaded ‘block extraction passages’.
The first AM manifold included features that allowed it to be removed manually without the use of tools, thereby negating the need for the extraction passages, which had been retained.
However, because removing these passages from the CAD model disrupted the intricate network of supporting structures, this was seen as an opportunity to further develop the design — particularly as it had been suggested that the first manifold might flex and promote chatter during machining.
The second iteration of the AM manifold saw an increase in its overall stiffness, while using just 21% of the material volume of the original block manifold.
This significant reduction in volume allowed version two to be made in 316L stainless steel (preferable to the use of aluminium alloy) while still achieving an overall weight saving of 37% (8gm/cm3 for stainless steel compared with less than 3gm/cm
3 for aluminium alloy).