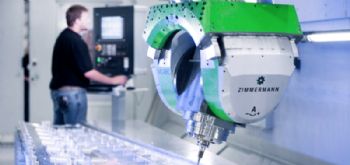
Large composite components for the Airbus A350 family of wide-body jet airliners are being machined on two German-built Zimmermann FZ33 portal machining centres at a specialist sub-contractor in England.
Supplied by sole sales and service agent Geo Kingsbury Ltd, Gosport (
www.geokingsbury.com), each machine has a work envelope of 16 x 3 x 1.5m and an installed weight of 168 tonnes.
The carbon-fibre epoxy matrix parts are some of the largest composite components in the world, up to 12m long, 25mm thick and weighing as much as 200kg.
The five-axis machining cycles — involving edge trimming, face milling and drilling — take up to 16hr in two operations; these include a significant amount of on-machine probing, first of the vacuum fixture position and then of the secured component during set-up, followed by post-machining inspection.
Dimensional accuracy over a full 12m span is within ±0.2mm. All parts then go for ultrasonic inspection before being shipped to the Airbus plant in Broughton.
Each Zimmermann FZ33s is fitted with a Weiss 45kW 25,000rev/min HSK-A63 spindle mounted in a slim-line head that provides 220deg of A-axis rotation and a direct-drive rotary C axis.
The X, Y and Z axes feature rack-and-pinion drives (with twin motors in X), along with linear scales; control is via a Siemens CNC, and two video cameras allow the operator to monitor the large working area.
Kingsbury says that composite machining results in high cutting loads and rapid tool wear, so carbide and poly-crystalline diamond cutters are used.
Dry-milling and drilling such materials create a lot of dust, which the FZ33 removes via the extraction and filtration unit at the rear of the machine and through a brush enclosure around the spindle head.