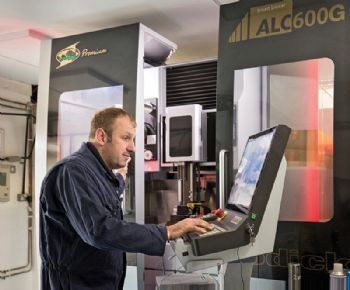
Foremost Specialist Products, a Derby-based sub-contract manufacturer of precision-engineered components, recently bought a new Sodick ALC600G CNC wire-erosion machine from Coventry-based Sodi-Tech EDM Ltd (
www.sodi-techedm.co.uk) to help it take on the “complex and awkward parts that no else wants to tackle” — such as stainless-steel tubular stem guides for power-generator turbines.
To compete as a “complex parts specialist”, Foremost has a range of CNC machine tools.
These include multi-axis machining centres, turning centres, horizontal borers (with capacities up to 2.5 tonnes) and EDM machines; and as a matter of course, any machine approaching the end of its ‘natural working life’ is replaced by the latest technology — as was the case recently with one of the company’s two wire-cut EDM machines.
Engineering director Joe Walker says: “We had won a contract for a particularly tricky part, but our existing EDM machine didn’t have the four-axis cutting required — nor enough memory to take on this work.
"The job necessitated producing a number of cross-holes in stainless-steel stem guides for turbines used in power generators — holes that are angled in two planes and must be held to extremely tight tolerances.
“We needed a new machine; and while Foremost had never owned a Sodick EDM before, I immediately took a liking to the Sodick ALC600G; its capabilities made us feel that we would be moving from a small hatchback to a super-car.”
The ALC600G wire EDM machine is a recent addition to the Sodick line-up and has a number of notable features; these include linear drives, absolute linear scales, the manufacturer’s Smart Pulse Wire control and Smart Pulse Generator, high-speed automatic wire threading, advanced corner control, an integral CAD/CAM system and an ‘intelligent’ automatic programming system.
Mr Walker says: “The machine is making particularly easy work of the stem guides, some of which have six or eight holes from 1.3 to 3.0mm in diameter, although one of the latest guides has 28 holes; and with the backlash-free linear drives, we have noticed a real difference in the tolerances we can now hold reliably, as well as vastly improved surface finish.
“I would also say that, compared to the one it replaced, the new machine is up to 50% quicker on many jobs.”