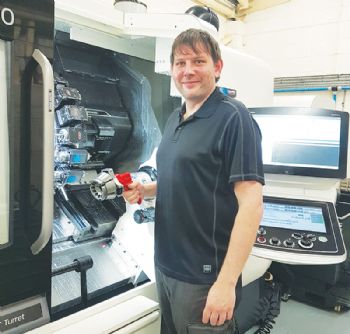
Just over three years ago, deep-sea welder and fabricator Ben Goodwin gave up his dangerous day job to start a sub-contract machine shop called BRG CNC Machining (
www.brgcnc.co.uk).
He started with a Hurco three-axis machining centre and more recently, he installed a DMG Mori turning centre fitted with work-holding equipment from Cannock-based Hainbuch UK (
www.hainbuch.com).
Based in Market Weighton (in the East Riding of Yorkshire), BRG CNC has achieved significant success and now has customers in Formula One, motor-sport, agriculture, utilities, offshore and general sub-contracting.
Mr Goodwin says he has always strived to put the profits back into the business — hence the early purchase of Open Mind CAM software to drive the Hurco VM10 and the later purchase of the DMG Mori NLX2500-700 turning centre.
“I was turning work away and missing opportunities by not having a CNC turning capability. I wanted a twin-spindle turning centre with a capacity for bar up to 80mm in diameter that could be bar-fed.
"I spent an age reviewing the options before selecting the DMG Mori machine; I also spent thousands on optional extras such as the sub-spindle, Y-axis milling, 70/30-bar coolant and 20-tool-position turret to get the most productive turning solution for my business.
A further key area of investment was the work-holding solution for the main spindle — a Hainbuch Spanntop Nova Combi collet chuck.”
The new DMG Mori NLX2500-700 is used to machine a huge variety of parts. When interviewed, Mr Goodwin said: “This week, we are machining a batch of 48 parts for the utilities sector, 68 35mm-diameter components for a rape-seed drill, and motor-sport components that are needed urgently.
"These parts are manufactured from 7075 aluminium alloy, S155 steel and EN24 steel respectively. Most of our work involves aluminium, stainless steels and various grades of steel.”
Workpiece clamping
Recalling the reasoning behind selecting the Hainbuch Spanntop Nova Combi chuck, Mr Goodwin said: “We really did our homework on workpiece clamping, as we appreciate the impact that rigid, robust and precise clamping can have on both the finished quality of the parts and the performance of the machine and the cutting tools.
"In addition, the engineers at DMG Mori recommended the Hainbuch clamping system. We spoke with Hainbuch engineers, and it was their appreciation of our needs, the available options, the support and service available that were all key reasons behind our decision to buy the Spanntop equipment.
“We are regularly machining batches of 76mm-diameter parts from 304 stainless steel and rely on the high clamping forces offered by Spanntop. Using the milling turret, we are rough-milling parts with a Seco HF end mill at a feed rate of over 6,000mm/min and a depth of cut of 0.8mm.
Clamping the parts on less than 30mm of material, the Spanntop is achieving clamping forces of over 3.5mpa; the hydraulic three-jaw chuck on the sub-spindle only achieves a clamping force of 1.6mpa. The result of the high clamping force is excellent surface finishes, as well as extended tool life — and we are using speeds and feeds greater than we imagined were possible.”
The Hainbuch Spanntop Nova Combi can be used with or without an end-stop. This provides the flexibility for turning both chucking parts and bar that is fed from the LNS bar-feeder.
Moreover, the Hainbuch Spanntop Nova Combi stabilises the workpiece by using an axial draw force to pull it against the end-stop.
In conclusion, Mr Goodwin said: “We rarely turn anything below 20mm in diameter, so I currently have the 25, 60 and 76mm collet adaptors.
"These cater for almost all my needs, but I will be buying further adaptors in the near future; and when we start getting more work that requires back-end working, we’ll definitely be adding a Hainbuch system to the sub-spindle too.”