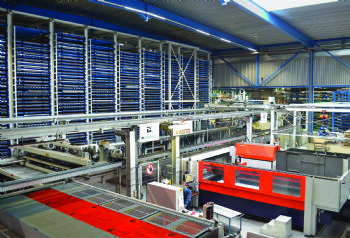
De Cromvoirtse, a Netherlands-based steel stockholder and contract manufacturer of small batches of semi-finished sheet-metal components, has invested in two interlinked, automated storage systems and connected them to three sheet-metal laser cutting machines to help shorten delivery times.
The Uniline store and Unitower B from the German company Kasto, which has a UK subsidiary in Milton Keynes (
www.kasto.com), ensure fast, accurate and damage-free material handling, while the supplier’s warehouse management system keeps track of stock and ensures smooth order processing.
Kasto says that manufacturers are increasingly ordering materials on-line, because it saves time and cuts costs by allowing different offers to be compared easily.
However, the increased competition means that for a vendor to be successful, it must not only have a broad range of products at attractive prices but also be able to make fast deliveries and provide a comprehensive array of services.
Founded in 1982 and with headquarters in the town of Oisterwijk, De Cromvoirtse spotted this trend early.
The company has operated an on-line portal since 2008, which today accounts for about 70% of orders.
Customers can use the company’s Web site to upload drawings and specifications; and within 2min, they receive an automatically calculated quotation for production of the component, based on a manufacturing capacity that includes press brakes and laser cutting machines.
About 90% of the products are made from steel, stainless steel and aluminium sheet; the remainder are from pipes and sections.
Janwillem Verschuuren, one of the company’s two managing directors, said: “Most of our 1,200 customers are small and medium-size companies that include agricultural-machine manufacturers, car body makers and machine builders.
“For them, it often doesn’t pay to buy machines of their own and hire expert personnel to make parts, because they only need limited quantities.
“Generally, we can deliver laser-cut components in 24-48hr; folded sheet-metal parts can be supplied within a week.”
Automated systems
To serve the needs of its growing customer base reliably and quickly, De Cromvoirtse has automated not only its ordering process but also most of its production.
Its metal-working machines operate round the clock, and 400-500 tonnes of material are usually held in stock.

The double-sided Uniline store from Kasto has nearly 1,000 storage locations, with special pallets for different materials and sizes, as well as pallets for remnants.
A stacker crane travels between the two rows of the facility, storing and retrieving material automatically.
Mr Verschuuren said: “When we invested in our new warehouse, we investigated various storage options, but Kasto quickly emerged as the front-runner.
“Other manufacturers offered us standard solutions that were unsatisfactory, but Kasto worked with us right from the planning phase to develop new ideas for the design. They told us clearly what wouldn’t work and what would.”
For example, it proved possible to connect two flat-bed laser cutting machines seamlessly to achieve continuous material flow.
To facilitate this, Kasto installed two manipulators at the Uniline’s output station. With vacuum suction units, the manipulators lift sheets from storage, place them on the shuttle tables and then remove the finished parts and remnants.
In this way, De Cromvoirtse has substantially increased the production capacity of its machines and shortened throughput times.
Ronnie van den Hurk, the other managing director at De Cromvoirtse, said: “The KASTO solution allows fast, efficient and safe handling of our materials.
“The stacker crane is equipped with two pallet stations to shorten cycle times and avoid empty runs. For each storage operation there is always a retrieval operation happening at the same time.”
Owing to De Cromvoirtse’s booming on-line business and the growing number of orders, even this system eventually reached its limits. In 2016, the company asked Kasto how to increase the store’s performance.
Additional capacity
The first thought was to add a second stacker crane to the existing Uniline system; but as this reconfiguration would have interfered with the store’s operations, Kasto devised an alternative solution involving the installation of a separate Unitower B store next to the existing in-line system to provide additional capacity.
The latest storage system, which was installed in a few weeks without interrupting the stockholder’s operations, consists of a double tower and stacker crane.

Some 8.5m high and with a compact footprint, it has space for almost 80 pallets, each capable of holding sheets up to 3,000 x 1,500mm; and because only the pallet that has been called up needs to be moved, access times are fast.
For maximum flexibility, the Unitower is connected to the Uniline store at the top by a bridge with a longitudinal, rail-mounted carriage.
In this way, pallets move automatically from one area of the storage facility to another without losing valuable space below.
An additional laser cutting machine is connected to the Unitower, with loading and unloading being performed automatically.
Moreover, by using various grippers, it is possible to handle whole sheets as well as cut parts and remnants, increasing both productivity and flexibility.
Mr Verschuuren says another advantage of the Kasto solution is that it allows metal-working machinery of any make to be integrated easily, thereby allowing De Cromvoirtse to source production equipment from more than one supplier and use machines that are most suitable for the given requirements.
Both the new and existing stores are controlled by Kasto’s warehouse management software, KastoLogic, which has been programmed to treat the two areas as a single connected system to facilitate operation and increase stock transparency.
It is connected with the stockholder’s ERP system, ensuring consistent data flow and smooth order processing; and as with the machine tools on-site, both the Uniline and the Unitower can be monitored remotely.
Indeed, if necessary, Kasto engineers can access the facility on-line from Germany and rectify any problems, although Mr van den Hurk says this has rarely been needed.