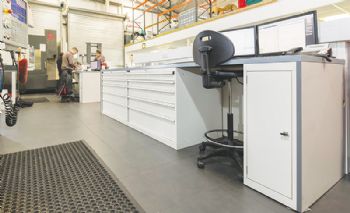
Built around its successful motor-sport team, the Jota Group has used the skills and experience that winning at Le Mans brings to develop a business that comprises: Jota Sport, which designs, builds and supports race-winning GT-, LMP2- and LMP1-class cars; Jota Aviation, a successful aviation charter business; and Jota Advanced Engineering, a sub-contract machining operation.
Key to the Group’s success is the effort put into everything it does, which includes focusing on attention to detail and delivering on its promises; and while Jota Advanced Engineering is the latest name to join the Group, machining has been a part of the business for many years.
Initially, the race-team technicians used manual machines to create one-off bespoke parts, and they had soon developed a small machine shop in their workshop.
The growth in demand for more-complex parts for its own cars, along with opportunities in the sub-contract machining sector, saw a need for expansion, and Jota Advanced Engineering was created.
It is already accredited with ISO9001 and is working towards further accreditations (in the automotive sector) that will assist in expanding its already nation-wide customer base in the automotive, motor-sport, aerospace and power generation sectors.
Ryan Goodger, director of Jota Advanced Engineering, said: “We have built the business on our precision engineering skills and undertaking tight-tolerance work, often in difficult-to-machine materials — and in many cases taking on work that others did not want to tackle.”
This has seen the company invest in a range of high-tech machine tools, including multi-axis turning centres with live tooling and a five-axis machining centre; these are supported by the latest in CAD/CAM and production control software — and a team of highly skilled engineers.
With the growth in the machining business and the number of machines came a requirement for more tools and work-holding equipment, which in turn needed to be stored in a planned and efficient manner.

Jota Sport was already a user of Fami storage equipment in its race bays, so Jota Advanced Engineering called in the Fami supplier — Ashford-based System Store Solutions Ltd — to design the workshop storage layout (
www.systemstore.co.uk).
Mr Goodger said: “Organisation and image are key in the sectors that we operate in, so having a consistent look running through the race team and engineering division makes perfect sense.
“Not only that, but to ensure that we can respond quickly to customer requirements, we need to be confident that we can locate tools and fixtures quickly; with the Fami solution, we know ‘everything has a place and everything is in its place’.
“Furthermore, the workshop environment is more manageable; it has also become second nature to keep things neat and tidy.”
System Store Solutions worked closely with Mr Goodger and his team to develop a layout that met their exact needs.
This included a series of Fami drawer systems with variable partitions that can be adjusted to store anything from paperwork, small hand tools and cutting tools through to large fixtures and jaws for the machine tools.
Workstations were built into this run of drawers, allowing technicians to work on computers while next to the machines.
Worktop tool storage was also integrated into the system, with the finishing touches a series of shelving for larger items and partitioning to separate the machining area from assembly and administration in what is an open-plan workshop.
Fighter aircraft
Increases in the production rate of the Lockheed Martin F-35 Lightning II single-seat single-engine stealth multi-role fighter aircraft at BAE Systems’ Samlesbury site have resulted in significant investment in the F-35 facility, where parts for the aft fuselage, as well as vertical and horizontal tails, are machined.
This facility is the result of a £150 million investment to support increased production, which in turn placed greater emphasis on the tool pre-setting required to keep the many machine tools running efficiently.

Gareth O’Beirne, operations manager for machining at BAE Systems, also turned to System Store Solutions for assistance.
“The effectiveness of our cutter pre-set area is key to our operational efficiency. Our machines have to be kept ‘fed’ with cutting tools, so we needed to ensure that this would be achieved.
“We looked at potential solutions with a Formula One pit-stop mentality — ones where cutting tools come in and are turned round very quickly.
“The tooling area, which covers the size of a standard swimming pool, needed to be organised in a way that would ensure a high level of efficiency.”
System Store Solutions, which was given ‘a blank sheet of paper’, provided a solution that has resulted in the operators having everything to hand, with individual operator stations for tool assembly, storage for the kanban system and general racking for tooling.
“What we have now is a highly efficient and ergonomic working environment that allows the machining facility to meet our production targets,” said Mr O’Beirne.
David Price, the managing director of System Store Solutions, says that working across many industry sectors gives the company the experience needed to create better and more-efficient working environments for its customers.
“The opportunity to work with BAE Systems on this project — and others — is down to the quality of products that we supply and the knowledge that we have of storage and workshop layouts to deliver the most effective solutions.”