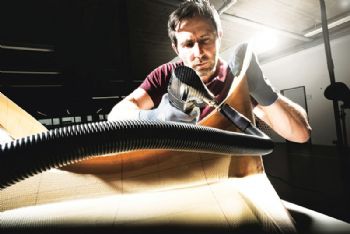
Luton-based Trumpf Ltd (
www.uk.trumpf.com) has developed a new nibbler that is said to be the first of its kind world-wide.
The TruTool FCN 250 is designed to cut various fibre composite materials up to 2.5mm thick; unlike saws, milling cutters and angle grinders that have been traditionally used to cut this type of material, it generates minimal dust, so personal protective equipment is no longer essential.
Furthermore, by comparison with other slitting processes, the company says that its cost per metre is as much as 50% lower.
Trumpf has modified the cutting geometries and cutting tools of its established nibbler design to make them suitable for fibre com-posites.
The TruTool FCN 250 can cut thermosetting plastics and thermoplastic polymers, as well as carbon-fibre reinforced plastics (CFRP), glass-fibre reinforced plastics (GFRP) and aramid-fibre reinforced plastics (AFRP).
Nibbling is a cold process that cuts a contour by producing a series of overlapping slits or notches. Thanks to the coated cutting tools featured in the TruTool FCN 250, users can create clean cut edges without the danger of delamination or fraying.
The easy-to-operate TruTool FCN 250 achieves a working speed of 1.9m/min.
As the tool gives users a clear view of the work surface, they can make precise cuts along a scribed line or template, or any contour that involves a tight radius.
The tool carrier can also be rotated through 360deg, simplifying tasks in hard-to-reach areas.
In terms of tool life, one die will typically process 300m of 2mm-thick GFRP or CFRP before replacement is required. Trumpf says that the cost-efficiencies are even greater for thinner materials.
Punch replacement is recommended after 150m and is accomplished in a matter of seconds without the need for additional equipment.