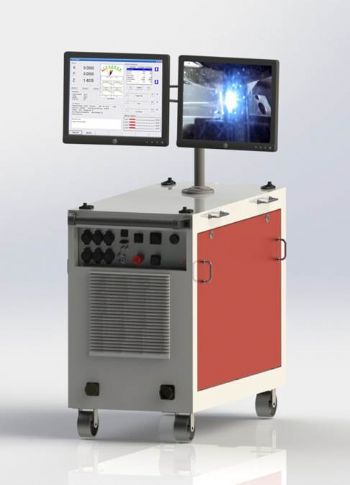
Walsall-based Hydratight, a global machining specialist, has become the first company to use electrical discharge machining (EDM) for maintenance work on a live nuclear-reactor pipeline system.
It completed the technically challenging project for an energy company at a power station in the USA, as part of its post-Fukushima upgrade. The use of EDM avoided a costly shutdown of the reactor.
Hydratight’s EDM process used a heated solid electrode to accurately cut a hole in the reactor feed water line and then removed the microscopic cuttings using back-flushing and vacuums. It prevented 99.5% of the cuttings from entering the reactor.
Mike Riordan, Hydratight’s nuclear specialty services manager, said: “This was a milestone achievement on a live nuclear-reactor pipeline system, resulting in safety enhancements in line with the industry’s post-Fukushima requirements.
“The work has created another way to feed water into the main line, if there is ever a power loss to the reactor.
“Material contamination is a major concern for most facilities, and electrical discharge machining is a highly accurate and safe way of machining.”
“Tool pressure was also a concern on this particular project, so we were able to use a method that was completely contactless.”