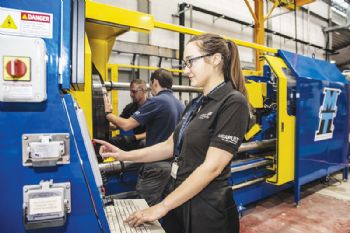
The University of Strathclyde’s Advanced Forming Research Centre (AFRC) is currently exploring innovative ways to reduce materials wastage and production time using two rotary friction welding machines — the largest of their kind in any UK research centre.
Rotary friction welding is a solid-state process in which a metallic part is rotated at high speed and pressed against another part that is held stationary.
The resulting friction heats the parts, causing them to forge together; the process is fast and very energy-efficient.
The AFRC’s staff will integrate this new capability with other advanced manufacturing techniques used at the centre, which could have significant implications for UK industry.
Until now, rotary friction welding has only been used in niche manufacturing areas in the aerospace and oil and gas sectors.
One of the first projects using the new equipment will see rotary friction welding used alongside other capabilities at the centre to develop a high-performance component for aerospace applications — significantly reducing materials wastage and production time.
AFRC research associate Laurie da Silva (
www.strath.ac.uk/research/advancedformingresearchcentre) said: “Welding is often regarded in the manufacturing industry as an easy place for a material to fail, but that isn’t the case for rotary friction welding. In fact, it generates a very strong high-integrity joint for metallic materials.
"We’re working with our members and partners on an industrial research programme that will demonstrate the considerable potential of this technology.”