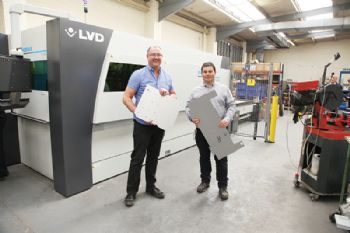
For brothers Darren and Ashley Churchill, going to work each day is more than just a job. Their company, Reading-based JC Engineering Products Ltd, was started 51 years ago by their father John, who is still very active within the business.
Darren said: “We are still a traditional small family business, and we have a good team of people who take great pride to ensure customer satisfaction.”
Some two years ago, the company acquired a local competitor, Just Precision Sheet Metal; last year, it installed a new LVD Phoenix 3015 4kW fibre laser machine (
www.lvdgroup.com).
It also invested in the complete refurbishment of its 10-year-old Easy-Form press brake, bringing it up to the specification of a new machine with the latest CADMAN Touch-B intuitive touch-screen control.
Darren says the decision to buy Just Precision was partly driven by the difficulty of finding skilled staff, adding that the upgraded press brake also helps with regard to staffing matters, as it allows a less skilled operator to use the machine.
JC Engineering (
www.jceng.co.uk) became a customer of Shape Machines in the early 1980s, and it remained a customer when Shape became part of LVD in the 1990s.
It bought its first CNC machine from LVD (a Delta 1000 turret punch), along with an LVD press brake. In 2005, the company added a second CNC punch press and an Easy-Form press brake with CADMAN B software.
Explaining why the company waited until last year to install a laser, Darren said: “We hadn’t bought a laser earlier because we felt that the technology wasn’t right for us.
We were carrying out a lot of second and third operations on the punch press, including countersinking, forming and putting on part identifications.
This meant we could keep the parts on the punching machine for all these operations and keep our labour costs down.
“We also undertake a lot of work in aluminium, which again suited the punching technology.
That said, if stainless steel had been a big part of our business, we would probably have bought a laser 10 to 15 years ago, but until last year we felt that the tech-nology and running costs for cutting aluminium were not going to give us any benefit over what we had.”
In-depth research
Ashley says that all changed with the purchase of the LVD fibre laser, which followed a significant amount of time researching fibre laser technology.
“We are generally working with materials up to 6mm thick, although most of our work is with materials that are 3mm or thinner. Today, the fibre laser is cutting these at such a rate that I don’t see how we could work any other way more cost-effectively.”
Once it had been established that the technology was right, one of the key drivers for JC Engineering’s investment decision was gaining control over its production processes.
Ashley says: “We were sub-contracting work to laser companies, but we felt that we weren’t getting the quality we required and that we were losing control of what we were offering our customers. We knew the next step for us was to bring control in-house, so that we would no longer be reliant on sub-contractors.”
When it came to buying a laser, Darren was initially attracted to LVD’s Electra, a high-speed machine for the fast cutting of thin materials; but knowing the type of products JC Engineering manufactures, LVD suggested that a Phoenix would be both more suitable and more cost-effective.
“For us, quality is the priority rather than pure speed. The better the part that comes off the machine, the less time we have to spend ensuring that the customer gets a good product.”
JC Engineering’s LVD Phoenix laser can cut aluminium up to 12mm thick, stainless steel up to 15mm thick and steel up to 20mm thick. The machine can also cut copper and brass, which the company could not previously offer; and with a punching and a laser cutting capability, it can select the technology best suited for each job.
Darren said: “Having both the laser and the punch presses gives us the flexibility to decide what is the most cost-effective way of making any part. The laser is best at complex profiles, while the punch is best at internal details and formed features. We now have the flexibility to get parts out of the door in the most cost-effective way.”
In conclusion, Ashley said: “We cover a lot of areas: aircraft, the computer industry, point of sale — almost anything, in fact.
"We never know what the next job is going to be; and while there have been jobs that we have shied away from in the past, the laser is allowing us to take these on.
"Indeed, it has transformed the way we do things. One of the biggest factors that influenced our decision to buy the Phoenix was the great relationship we have with LVD, both here in the UK and in Belgium. Buying a machine is one thing, but continued support after the investment is invaluable.”