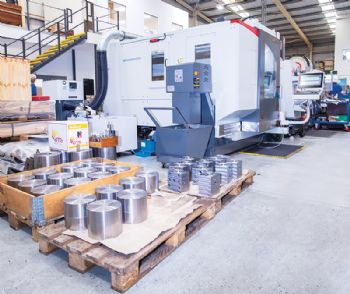
Originally set up in 1979 to make press tools for companies in its local area, Newcastle Tool & Gauge (NTG) has gradually evolved into a precision engineering machine shop — and a preferred supplier to customers in a wide range of industry sectors, including oil and gas, power generation, sub-sea and thermoforming.
As its customer profile continues to change, so does its requirement for machine tools; last year, it identified the need to adopt full simultaneous five-axis machining.
Mark Withycombe, operations manager (
www.ntg-ltd.co.uk), said: “We have a varied mix of CNC machining centres, turning centres, grinding and wire erosion machines, but we knew that a five-axis machine had to be an integral part of the mix.
"A group of us visited MACH 2018 with the brief to look at every five-axis option, and we all came back with the same opinion — that the XYZ UMC-5X was the right option for us.”
Among the features that impressed NTG were the use of a trunnion table to provide the weight-carrying capacity needed, the ease of access for loading, the overall build quality of the machine and the highly competitive price.
Seeing a UMC-5X equipped with a Siemens 840DSL Shopmill control on a visit to XYZ Machine Tools’ Burlescombe showroom (
www.xyzmachinetools.com) was described as a ‘lightbulb moment’ by Mr Withycombe.
“We have broad experience of a number of control systems, but having seen how easy the Siemens was to program and the overall user-friendliness of the control, the entire team pushed for that.
“All that was left was to specify the rest of the machine to suit our needs, which included a 60-position tool changer and a 15,000rev/min in-line spindle.”
With the machine now installed, the initial expectations of the team at NTG are being fully met, with the build quality and accuracy of the machine helping to reduce cycle times.
One particular job that would normally have taken six operations to complete is now down to two, and the cycle time has been halved.