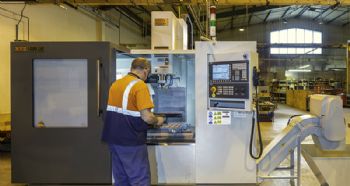
Sheffield-based Eclipse Magnetics — familiar for its magnetic chucks and lifting equipment — now encompasses a much wider product range, with magnetic filtration and separation systems accounting for around 50% of its turnover.
These systems are used in a diverse range of applications, including machine shops (to remove swarf) and the food-processing industry (to eliminate metal contamination in high-speed production lines).
The growth of this side of the business recently prompted the decision to replace a 25-year-old vertical machining centre that was considered to be ‘on borrowed time’.
The nature of the company’s work, producing a mix of standard catalogue and bespoke systems, meant that any new machine had to be versatile, easy to set up and easy to program — plus have the required Y-axis travel.
Design engineer John Parker (
www.eclipsemagnetics.com)said: “In addition to the size of the machine, price/performance was also a major driver in our decision-making, when it came to the new machining centre.
"We looked at lots of machines, but after discussions with one of our sub-contractors — Impact Toolroom Services, which uses XYZ machines, we settled on the XYZ 1000 LR vertical machining centre.
“While the machine size and specification matched our needs, one concern that we had was the 25-year step in control technology. Our old machine had a Fanuc control that we programmed using G-code, so the switch to the latest technology with the Siemens 828D Shopmill control was a little daunting.
"However, the simplicity of programming on the Siemens control means that we now program most jobs at the machine, with off-line 3-D software on the PC as back-up if needed.”