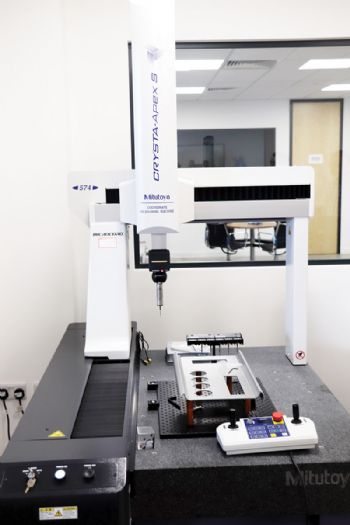
In 1936, Pittsburgh’s Great Flood crippled Western Pennsylvania, leaving thousands without electricity. In an effort to help restore the city’s power, Donald Ross started the Allegheny Electric Co; later — having noted the wiring method used by overhead cranes within manufacturing industry was particularly dangerous — he took steps to address this.
In the 1980s, the company introduced the Track Busway for supplying power to stationary equipment; in the 1990s, it changed its name to Universal Electric Corporation (UEC) and created two separate divisions — U-S Safety Trolley and Starline Track Busway.
The latter now provides electrical power distribution systems for the data centre, retail, industrial and higher education markets.
To better support a European customer base, UEC’s UK division moved into a new 60,000ft2 factory in Reading last year; and being both UL and ETL listed (both are nationally recognised testing laboratories), as well as CE marked for use anywhere in the world, the quality of the company’s Busway product lines is a critical factor for the business.
Clive Larke, quality director at the UK facility, said: “When I joined Starline about three years ago to help set up the company’s global quality programme, it became apparent that we needed to upgrade our metrology capability, particularly in light of our ‘aggressive’ growth in both Europe and Asia.”
Referring to the relationship that the company has established with Andover-based Mitutoyo (UK) Ltd (
www.mitutoyo.co.uk), Mr Larke said: “I have been in quality assurance for around 25 years, and I have worked with a number of equipment providers in that time.
The things that set Mitutoyo apart from its competitors are its global reach and its after-sales support. As part of our ‘global strategy’, we wanted our operations here in the UK, in the USA and in our other hub in Asia to be ‘mirror images’ of each other.
"We control all three QA labs from our hub here in Reading, so we can ensure that all customers world-wide get the premium Starline product they expect.”
Standardised facilities
Tasked with implementing a standardised measurement facility on three continents that would allow for seamless global integration and conformity, Mr Larke approached Mitutoyo.
Trevor Stubbs, the company’s southern-area technical-sales engineer, said: “I had previously supplied Mr Larke with Mitutoyo products when he was at a different company, so when he joined Starline, he got in touch to see how we could best undertake his metrology project.
"Initially, he brought a number of parts to our Andover headquarters, where we conducted extensive trials and conformance reporting.
“As a result of these trials, we recommended a number of products. These included a Crysta Apex 574 three-axis CMM, a Quick Vision Active QVL-404 two-axis CNC vision-based measuring system, a Quick Image QI A2010 image-recognition and measuring system, and an LH600E height gauge — plus a selection of hand tools, a granite table and a number of other ancillary products.”
Mr Larke said: “Following our acceptance of his recommendations, Mr Stubbs ordered the equipment not only for the Reading facility but also for those in the USA and Singapore, thereby ensuring that UEC has complete uniformity across all its manufacturing sites.
"The Crysta Apex CMM is used for measuring critical dimensions, as well as the dimensions on mating parts that require an optimal fit; and because the company manufactures thousands of components and assemblies, this CMM will also be used to measure sections of extruded aluminium prior to them being entered into production and assembly. Additionally, the QVL-404 measures extrusions with exceptional speed and efficiency.”
Contributing to this speed and precision are an automatic edge-detection function and an automatic image focus facility; these combine to allow automatic measuring with ‘nothing more than rough positioning on the surface
of the machine’.
Mr Larke added: “This overall capability allows Starline to automate a lot of its metrology departments’ functions. For example, the CMM and the QV can be set up to run automatically, allowing one of the staff in the quality department to undertake other tasks, such as measuring extrusions on the height gauge.”
Steve Roddy, who oversees the metrology departments in the UK and at the overseas sites, said: “We measure each individual sub-component that comes into the business, to ensure that we meet all the drawing tolerances specified, so the really good relationship we have with Mitutoyo is essential.
"Whether I am in the UK, the USA or Singapore, I can contact Mitutoyo engineerss in the UK and have a response within an hour, either by e-mail or phone. Moreover, all the machines have designated training programmes, and advanced courses are available.”