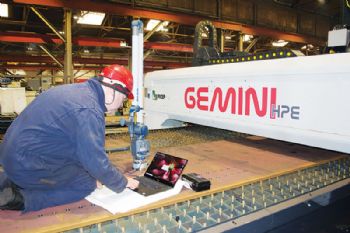
To enable the efficient completion of a challenging project in a nuclear plant, Watson Towers Ltd — a leading UK engineering and steel service provider — recently bought a 3.5m-capacity version of Faro’s QuantumE ScanArm fitted with a FaroBlu Laser Line Probe SD and supported by Faro’s CAM2 metrology software.
The equipment was supplied by Rugby-based Faro Technologies UK Ltd (
www.faro.com).
The tasks in question were to very accurately reverse-engineer large fabricated parts located inside a nuclear plant, produce new parts that were precise duplicates of the originals, and fit them.
Established in 1971, Watson Towers began life at Wishaw in North Lanarkshire, Scotland.
After two decades of notable growth, the company relocated (in 1991) to its current site in Coatbridge, near Glasgow.
Its move to the former steel foundry gave it the required larger facility, as well as access to highly skilled steelworkers and engineers.
Now run by Neil Watson and Fraser Towers (the sons of the company’s founders), Watson Towers continues its commitment to ensuring that the business maintains and grows its position as a major UK steel plate and engineering service centre.
Explaining the recent Faro purchase, general manager Iain Hussey said. “Watson Towers boasts some of the best technical resources and expertise currently available in the UK, and these assets allow us to meet all of our customers’ steel and engineering requirements.
“That said, having won a major contract from a client involved in the nuclear power industry, we realised that we needed to invest in a laser scanning system that would allow us to perform in-depth non-contact scans of the large elements that needed to be reverse-engineered.
The captured point-clouds could then be used to create the CAD models we needed to duplicate the various fabrications.
“Having considered several laser scanning devices, we concluded that the QuantumE FaroArm fitted with the FaroBlu Laser Line Probe SD was the ideal system for our needs. We are impressed by the system’s high-speed point-cloud capture and high resolution.
"We also realised that the QuantumE could undertake many of our other on-site and off-site scanning and measuring tasks.
“After the QuantumE and CAM2 software were delivered, our operators were quickly trained; and although the use of our ScanArm on the nuclear power site was the first time we had used it on such a major project, its ease of use was such that the required laser scans were made without a problem and the resulting CAD models were used in the manufacture of the new fabrications.
"These perfectly matched the originals, which meant no alterations or adjustments were needed, and they were quickly installed without a single problem.”
Portable benefits
Although the new equipment was originally purchased for the nuclear-industry reverse-engineering application and to perform on-site scanning tasks at other customers’ premises, its portability and robust nature mean that it is also regularly used on a wide range of applications at the vast Watson Towers facility.
For instance, it is used as a quality control aid on the company’s recently installed Ficep Gemini large-plate CNC drilling, milling and thermal cutting system.
Mr Hussey said: “In addition to the nuclear industry, Watson Towers serves a wide range of other industries, including the oil and gas and marine sectors.
"To enable us to consistently win contracts and to satisfy the exacting needs of our customers, we pursue twin policies of providing cost-effective quotes and applying the most stringent quality-control standards, which include guaranteed traceability — from steel mills to the end user.
“By using our new QuantumE ScanArm on — for instance — our new Ficep Gemini thermal-cutting machine, we can ensure the quality of its high-volume output.
“The speed, ease of use and high precision of our QuantumE with a FaroBlu Laser Line Probe mean that it has quickly made a significant contribution to both our operational efficiency and our inspection functions.”
For more than 35 years, Faro has designed, developed and delivered arm technology as a portable 3-D measurement solution for factory metrology.
Available in three different models with varying accuracy specifications, the company says the new Quantum FaroArm is the first arm on the market that can be verified against the international certification standard for articulated-arm co-ordinate measuring machines — ISO 10360-12:2016 — thereby ensuring maximum measurement consistency and reliability
in a wide range of work environments.