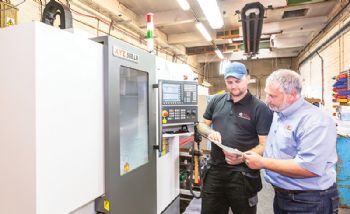
When Sheffield-based Air Accessories — a distributor of fluid-power products — was established in 1967 by pneumatics expert John (Jack) Bushby, customer service was at the heart of everything the company did, and this is still true today under current owner and managing director Nick McKee.
The business aims to deliver products that meet customer needs precisely; as such items do not always come from a standard catalogue, it was necessary to introduce an in-house machining capacity.
Mr McKee said: “Jack saw the value in manufacturing — not just re-selling — and that is something we have continued and expanded upon.
“We are constantly developing products, either for new applications or to meet existing scenarios, some of which may be 30 years old.
“We can improve old products or meet obscure requirements by developing things in-house, which gives us a competitive edge.”
Turnover doubled
This ‘edge’ has led to a doubling in turnover since Mr McKee took over the reigns of the company and decided to extend its in-house machining capacity.
It was already the user of an XYZ ProtoTrak-controlled mill, so an update in that area seemed to be the obvious route for the company to take, as the ProtoTrak control was considered ideal for the one-off and low-volume work that Air Accessories had planned.
However, production manager Ian Malpass and CNC setter operator Clive Glossop had other ideas.
They suggested bringing in new capacity in the form of an XYZ 500 LR vertical machining centre.
Mr McKee said: “My first reaction was ‘no’; we needed lots of things, but a new CNC machine was way down my list.
“However, after spending about 30min talking to Martyn Jones from XYZ Machine Tools (
www.xyzmachine tools.com), discussing the benefits of the machine, plus payback and finance options, I was convinced.
“At the back of my mind was the fact that we are pneumatic engineers — not production engineers — and my thought was that a machine of this type was a luxury, not a necessity; but I also recognised that to get the best out of people you need to have better equipment.
“Now that we have the machine, we may well become production engineers, as it gives us the flexibility we need; it is like having another member of staff.”
The new machine has reduced Air Accessories’ reliance on putting work out to sub-contract; it has also opened up opportunities for new business.
A further benefit to Mr McKee was a financial one — in the form of R&D tax credits.
“With much of our machining consisting of proving out development work, it was becoming harder to pass on those costs to customers.
“For years, I was against things like this, as it was accountant-driven, but we’ve looked into it since having the 500 LR, and it is an eye-opener to realise how much time you invest in R&D.
“With this in mind — and prompted by Mr Jones to work out the true hourly rate for running the machine — we created a template that allows us to claim what we can from the Government. In reality, it is a straightforward process — with our claims either being accepted or rejected.”
‘One-stop-shop’
The change from the ProtoTrak-controlled mill, which remains in situ, to the Siemens 828D-controlled 500 LR was straightforward.
Mr Glossop, while already familiar with the control, took advantage of the free training at XYZ’s Sheffield showroom, so the new machine was quickly producing parts.
Mr McKee concluded: “Having this additional machining capacity helps us to be a little bit different from our competitors, as we feel it is important to have the ability to make products, not just supply them.
“We are now seen as a ‘one-stop shop’ and can cater for more customers and their individual needs.”
The 500 LR is the entry-level machine in XYZ’s range of linear-rail machining centres.
It has an 8,000rev/min 18hp (13kW) BT40 spindle, with 10,000 and 12,000rev/min units available as options.
The feed rate in all axes is 20m/min, the X/Y/Z axis travels are 510 x 400 x 450mm, and a 12-position carousel-type tool changer is fitted as standard.