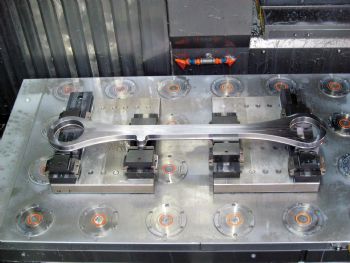
A new zero-point clamping system has been introduced by Leader Chuck Systems Ltd, Tamworth
(www.leaderchuck.com). Designed to significantly reduce set-up times and increase machining efficiency, the patent-registered ZeroClamp provides an effective route to producing more components, quicker and at a lower cost. A number of features set this work-holding solution apart from similar systems.
Using the face-and-taper HSK spindle tooling principle, ZeroClamp can achieve a repeatability of ±2.5µm — around 10-times more accurate than most similar systems. As the hollow, tapered-shank bolt is drawn into the clamping pot, the elastic properties of the seating ring mean that it can expand slightly, allowing the taper to locate positively and the faces of the pot and the pallet or raw material to engage and locate solidly. As a result, each fixing point has a break-out force of between 12.5 and 60kN (depending on the clamping-pot diameter).

This principle also removes any machining-induced vibration, minimises all thermal effects and compensates for hole misalignments up to ±0.1mm, as the tapers always compensate towards the centre of the clamping position. The tapered bolts are produced from case-hardened 42CrMO2 steel, allowing the workpiece or raw material to stand on them for storage.
Moreover, only one design is used, avoiding the confusion caused by ‘fixed’ systems, which usually require three different bolt designs and can magnify thermal errors. Another advantage of the taper bolt design is that it allows the pallet or workpiece to be tilted during loading and unloading without fear of damage, making heavy and unbalanced workpieces easier to handle. It also means the units can be fitted at any angle, so they can be used in conjunction with tombstones or similar fixtures on horizontal machining centres. Moreover, the units are around half the height of alternative zero-point fixtures.