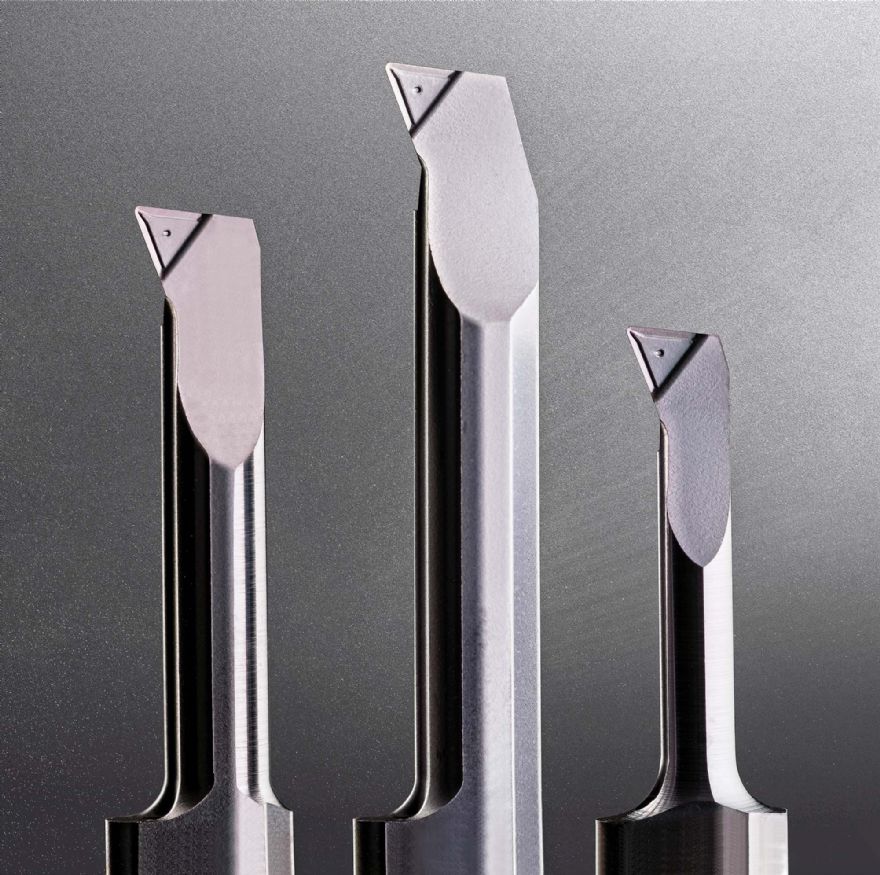
Adding lead to metallic materials has a positive effect on machining processes, but due to the European Union’s increasingly stringent REACH and ROHS regulations aimed at protecting human health and the environment from hazardous substances, these free-machining alloys are being discontinued, as lead is highly toxic. At its recent
Technology Days open house in Tübingen, southern Germany, cutting tool and insert manufacturer
Paul Horn GmbH explained the measures it is taking when producing its latest products to mitigate the difficulties that its customers face due to the phasing out of lead as an alloying element.
The main problem when machining lead-free alloys, whether steel or brass, is a lack of reliable chip breaking. During machining, the presence of the soft metal creates predetermined breaking points, as lead forms small inclusions in the alloy structure, promoting the formation of small, discontinuous chips rather than long, stringy ribbons.
This effective chip-breaking is accompanied by low cutting forces, while lead also acts like a lubricant, which reduces tool wear. The changeover to machining harder, tougher, more abrasive lead-free materials was initially a challenge, as the previous benefits were lost; in particular, wear on the cutting edge increased significantly.
Non-ferrous alloysHorn engineers remedied this for grooving and longitudinal turning by taking laser-cut chip-breaker geometries normally reserved for cutting steels, adapting them and applying them not only to those materials but also to lead-free brass and other non-ferrous alloys that no longer have their free-machining properties. Extensive investigations showed that this works very well.
For boring, geometries were again adapted to ensure reliable chip breaking. One of the biggest challenges in internal machining is the generation of long swarf that wraps around the tool, clogs the hole or, in the worst case, leads to tool breakage. Previously, laser-cut or ground chip breaker geometries were employed but such carbide inserts tend to be expensive.
With Horn’s new Type 105 Supermini and now the Type Mini with I geometry, Horn has succeeded in developing boring tools with a chip breaker form that is pressed into the insert’s rake face as the green tungsten carbide blank is being manufactured. After the blank has gone through the high-temperature sintering process, the chip breaker shape is permanently fused into the final, hard insert. Such geometries are cost-effective, can be used universally for different material groups, and are suitable for internal, face, copy and back turning. Chip control is good, even when the in-feed rate is low.