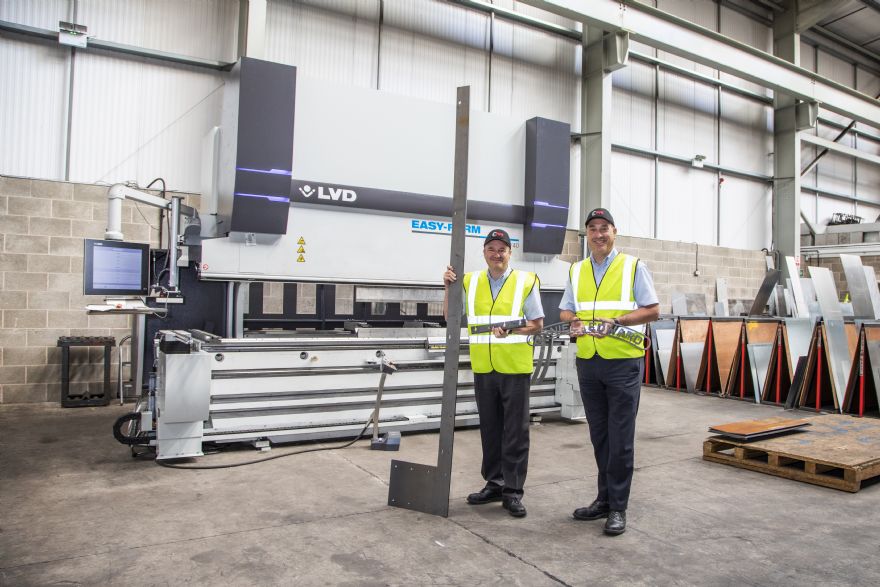
Derby-based Eggleston Steel, a family-owned stockholder, has invested in a 6kW LVD Phoenix fibre laser sheet metal processing system with a 4 x 2m capacity and automatic nozzle changer, along with a 4m 220-tonne Easy-Form press brake and a 6mm-capacity guillotine. The machines were supplied by Banbury-based LVD UK Ltd (
www.lvdgroup.com).
Founded in 1809, Eggleston Steel has grown significantly since moving to its current site 16 years ago. The company now employs 56 people and has a turnover of around £8 million, with customers typically in the fabrication, construction and DIY markets.
Managing director Richard Hewitt said: “We have grown rapidly after our move to the new site, thanks to a number of factors, including increased efficiencies, more space and better buying. However, one of the most important factors has been the company’s move into processing — profiling and bending — in addition to its traditional stockholding activities.”
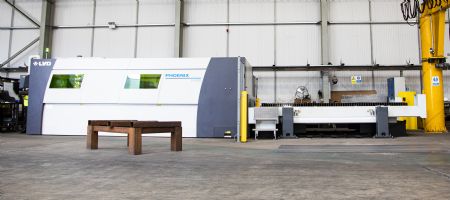
“Operations director John Ready said: “Processing is our special skill, and along with short lead times, that is where we tend to win work. Our customers tell us we are much quicker and more flexible, as we will take on the jobs that our larger competitors don’t want to do.
We offer general steel products; but now with the laser, a customer can purchase a beam from us with the end plates and cleats — all delivered on the same day on one vehicle. This capability certainly gives us an advantage.”
Mr Ready also pointed out that, until recently, the company operated a five-year-old 6kW CO2 laser and a second-hand fibre laser, but it realised that it was losing laser work to competitors on price. “We knew that the main cost of a job is the steel; and because we were buying as well as we could, it had to be that our competitors were able to produce things more cheaply than we could. We realised that a lot of them were using machines that were faster and more efficient than ours.”
Accuracy and repeatabilityEggleston Steel decided that it was time to replace the second-hand fibre laser, along with the 10-year old press brake and the even older guillotine. Mr Ready said: “The three customer demands that we always have to meet are quality, lead time and price — and usually in that order.
That means we need machinery that offers the accuracy and repeatability required to meet those demands, while being efficient in terms of energy usage and consumables, for example, to make sure that we can compete on price.
“We wanted to place a single order with one company, and over a period of eight months spoke to all the major players in the laser and press brake markets. LVD stood out straight away as the front runner as, like us, it is an independently owned family business.”
Mr Hewitt said a trip to LVD’s headquarters in Belgium clinched the deal. “When we saw the LVD factory, we were immediately reminded of our own company — the attention to detail, the pride in the workmanship and the feeling that the staff really seemed to enjoy working there. Moreover, we felt that they were giving us honest advice, rather than just a sales pitch.”
Mr Ready said that the key talking points regarding the Phoenix laser are speed, accuracy, quality and running costs. “It is not only twice as energy-efficient as the fibre laser it replaced but also significantly faster — both factors that make a big difference to cost and lead times and allow us to be much more competitive in a fast-paced and sometimes very tight market. Having the Phoenix allows us to compete with much larger national steel companies.”
On some jobs, the processing time has been cut by as much as 3-4hr. For example, a project for a portal-frame building with numerous base plates, cleats, connecting plates and related components — in materials from 3 to 10mm thick and with lots of bolt holes — would previously have been a 9-10hr job; that could now be 5-6hr, making a big difference to the price.
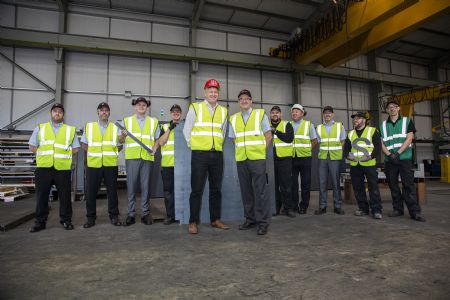
Eggleston Steel has also gained significant benefits with the new Easy-Form press brake. Previously, the company suffered problems with accuracy and repeatability, which necessitated cutting extra blanks and additional operations to ensure that a job could be completed.
Now, every bend is ‘right first time’, with no need for re-bending or adjustment and no need to cut extra blanks for test bends.
Mr Ready said: “The operator just enters the desired bend angle in the machine, and we know that when he takes the part out it will be right. This has allowed us to produce more-accurate parts first time and significantly reduce the number of rejected parts.
“The nature of our business means that we often do two and three-offs, so getting ‘right first time’ parts without having to scrap any is very important.”
Positive differenceMr Ready also said that LVD’s CADMAN B off-line programming software has helped Eggleston Steel to increase productivity and produce more-accurate complex parts.
“The off-line software means that we can simulate tricky parts on a PC — based on our actual press brake configuration and tooling — and check for errors that may occur due to clashes.
“Previously, we would have cut parts to test on the press, so other jobs going through would have to stop until those test parts had been completed. That has definitely made a positive difference to us.”
The machine is also fitted with sheet follower arms; these make the handling of large parts safer and allows large work to be undertaken by a single operator.
“With regard to the guillotine, we just needed a newer machine; and as we were buying the other two machines from LVD, it made sense to buy this from them too. The key thing was that LVD could supply the complete package.”