
BT Lerson, which operates from a brand-new 15,000ft
2 facility near Stansted Airport, is working in partnership with DMG Mori and benefitting not only from the capabilities of the latter’s machine tools but also the technical support, training and contacts that the collaboration brings, thereby achieving a step change in its business.
Some 70% of BT Lerson’s work is for the aerospace and defence sectors, but the company also serves the oil and gas, and pharmaceutical industries. Started in 1980, it made the move into CNC in the early 2000s, changed its business model in 2010 to concentrate on higher-value parts and achieved AS9100 status in 2014.
The company’s first five-axis DMG Mori machine — a DMU 50 — was bought pre-owned, and collaborating with Coventry-based DMG Mori UK Ltd (
www.dmgmori.com) helped it get to grips with the five-axis technology. The machine was subsequently refurbished by DMG Mori, and this marked the beginning of a ‘close partnership’.
The DMU 50 was soon followed by a DMU 40 Evo with Erowa automation in 2014, a DMU 60 Evo linear with 3R automation in 2016, and two NLX 2500/700 turning centres — in 2018 and 2019.
Julian Bedford, BT Lerson’s managing director, said: “Five-axis technology can be quite demanding, and it was a big learning curve for us.
“However, we soon saw the benefits of these investments, with cycle times slashed
and product quality increased dramatically. We also recognised the need for automation, to enable us to get more from the machines, people and skills that we have.
“The cost of the automation was easily recovered within two years; and without it, we would have needed three conventional machines to produce the same output — along with the associated extra labour, floor space
and work in progress. We now consider automation to be essential, particularly as
our automated machines run at over 90% OEE.”
The 3R automation system accommodates up to 60 pallets, the Erowa system up to 24 pallets. BT Lerson will set up a series of different jobs to match demand; it also sets up sister tooling where long machining times are called for — and uses the DMG Mori tool-life management to switch tools automatically, enabling the machines to run unmanned for extended periods.
Turn mill capabilityThe two DMG Mori NLX 2500/700s replaced existing machines; they have a bar feeder and a parts catcher for producing parts up to 80mm in diameter, while the use of chucks allows parts up to 366mm in diameter to be machined.
Mr Bedford said: “These machines have changed the way we turn-mill; and with them being robust and thermally stable, there is very little deterioration in tolerance. Indeed, we can run unmanned for 24hr and maintain tight tolerances.
We have also invested in DMG Mori gear-cutting software for these turning centres, allowing us to often cut as many as five separate operations to two.
“All our DMG Mori machines are covered by a five-year service and preventative maintenance plan, which we are planning to extend to other machinery in the factory. We also used DMG Mori finance for the NLX machines, as it was very competitive and offered options such as deferred payments and balloon payments.”
Formerly BTL Precision, BT Lerson acquired Lerson Fabrications (a preferred supplier to Stansted Airport and its supply chain) and moved to its new location at the end of 2019.
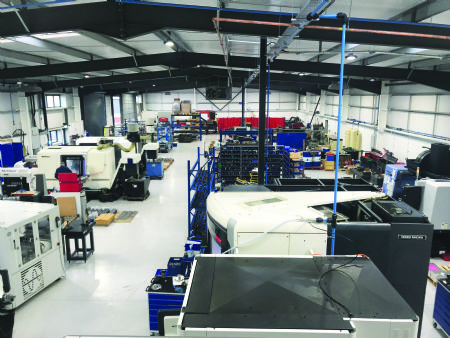
Mr Bedford said: “The move to the new factory provided several steps up in our working environment, and it has a big impact on customer confidence. Aerospace customers see that we have DMG Mori machine tools — properly monitored in a professional environment — and are immediately reassured.
“These customers are building long-term relationships with competent companies as part of their supply chains, and our aim is to establish in-depth and early involvement with these customers, for whom high quality and competitive pricing are the key considerations.”
BT Lerson is building on its relationship with Stansted Airport and bringing its fabrications business up to AS9100 standards too. Mr Bedford is also a governor at Harlow College, which is currently involved in a project at the airport; he is also involved in a digitalisation project at Cambridge University and is evaluating how this could be implemented at BT Lerson.
In conclusion, Mr Bedford said: “Working in partnership with DMG Mori has definitely led to new business and is enabling us to reinforce long-term relationships with our customers.
“A strategy of collaboration and co-operation at all levels of the business, combined with technical excellence from DMG Mori, has transformed how we operate.”