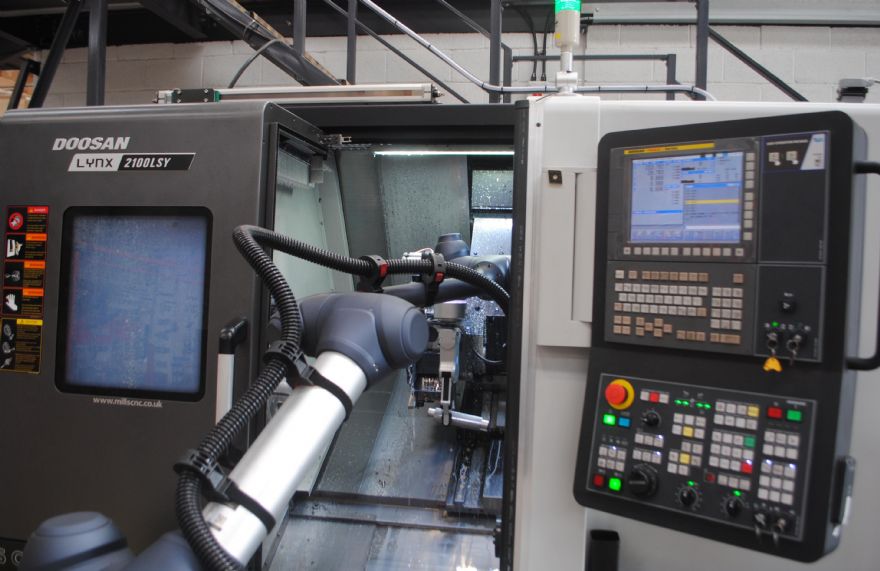
Somerset-based
Watson Gym Equipment, a leading manufacturer of specialist strength training equipment used in high-end gyms, has recently invested in two new Doosan machine tools and a Doosan collaborative robot (cobot) from Leamington Spa-based
Mills CNC — the exclusive distributor of Doosan machine tools in the UK and Ireland.
Watson Gym Equipment, established by owner and managing director Simon Watson in 1999, acquired its first Doosan machine — a large-capacity Puma 4100MB lathe — in March 2020.
The 15in chuck box guideway Puma 4100MB is a rigidly designed and built machine suitable for a range of heavy-duty machining operations including interrupted cutting. The Fanuc 0iT-controlled machine is equipped with a high-torque 30kW/2,000rpm spindle, a servo-driven 12-postion tool changer and 7.5kW/4,000rpm driven tooling capability.
Since being installed the lathe has been used to machine the company’s Pro Olympic weight plates (the flat discs located at either end of a weight bar to create a barbell or dumbbell used for weight training) which are made from solid marine-grade stainless steel.
In late 2019 Watson Gym Equipment had approached its existing CNC machine tool supplier to discuss the best way to ramp up production of its weight plates in order to meet increased demand. Initial discussions centred around the acquisition of a new large-capacity vertical turning lathe to machine the components but, with an anticipated delivery time approximately six months after order placement, the company decided to consider alternatives and as a result approached Mills CNC.
Mr Watson said: “We were already aware of Mills CNC and knew that the company had a good reputation in the market for the technology it sold and the after-sales services it provided.
“We approached the company to see if it could help with our specific machining capacity issue and, after an in-depth discussion, Mills recommended the Puma 4100MB - a large-capacity horizontal lathe that was available from stock, and which could be delivered and installed immediately.
“Mills took the time to understand our business and bought into our business model and what were trying to achieve. It pointed out potential tooling interference issues that could occur by going down the vertical turning lathe route and, instead, demonstrated the productivity and flexibility benefits that we could expect to gain from investing in the Puma lathe — all of which have proved correct.”
Weight plates
Watson weight plates can be supplied to customers in a range of standard sets (150kg, 250kg, 350kg and 500kg) with individual plates weighing between 5kg and 25kg. They are machined to high accuracy and exacting surface finishes. The plates feature powder coated end plates that can be customised with a customer's logo or brand if required, and are supplied with a lifetime warranty.
A quick look at Watson’s weight plates, just one product range in its extensive portfolio, demonstrates the company’s commitment to quality and continuous improvement, and goes a long way in explaining its continuing growth and success.
Mr Watson continued: “It’s relatively easy, and cheap, to manufacture weight plates from mild steel and then zinc- or nickel-plate them to give a professional looking finish. However, after a short period of time, and through constant use, they will lose their lustre and the coating will peel, chip or discolour.
“Our business model is focused on manufacturing high-quality, high-performance and competitively-priced premium products and equipment that look the part and that stand the test of time. That is why we use stainless steel for our weight plates.”
Stainless steel is also used for the company’s range of popular and best-selling dumbbell handles.
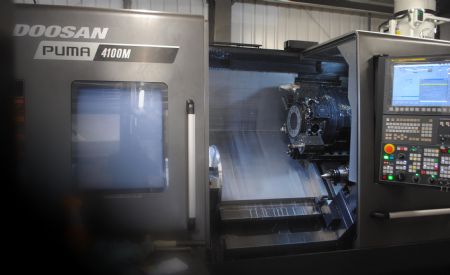
In early 2020 Watson Gym Equipment, with demand for its dumbbells at an all time high, made the decision to increase its in-house production capacity and once again approached Mills CNC for guidance.
Of particular concern was how to increase production of the company’s heavy-duty dumbbell handles which are available in different lengths (12in to 22in) with a 30mm grip.
Mr Watson continued: “Dumbbell handles are not complex components. They are machined from bar and cycle times are short and to meet increased customer demand we needed additional turning capacity — and we needed it fast.
“Having already established a good working relationship with Mills through the acquisition of the Puma 4100MB we approached it again with our requirement, and they recommended the purchase of a Doosan Lynx 2100LSYB lathe and a Hydrafeed bar feeder.”
The 8in chuck/65mm bar capacity Lynx 2100LSYB is a compact, multi-axis turning centre equipped with a high torque main spindle (11kW/4500rpm), a sub-spindle (5.5kW/6,000rpm), a Y-axis (+/- 52.5mm) and driven tools (3.7kW/6,000rpm).
The machine is considered ideal for small part production and is fast, accurate and reliable.
The machine and bar feeder were installed at Watson Gym Equipment’s facility in early May 2020 and its production capabilities have recently been significantly increased still further with the recent addition and integration of a Doosan M1013 collaborative robot (cobot) which was delivered and installed later in the month.
The cobot, with its 10kg payload and 1.3m reach radius, is positioned in front of the Lynx lathe and is programmed to unload the finished parts (dumbbell handles) once machining operations have been completed.
Mr Watson explained: “The job and machining process were ideal for automation. We can set up the job and leave the machine running unattended and overnight. As a consequence we have improved our productivity significantly and, because we have effectively removed the labour component from the process, have reduced the cost per part as well.”
Future developments
Watson Gym Equipment is constantly innovating and improving and plans are currently underway to increase the company’s floorspace by an extra 22,000ft
2 with the building of a new machine shop adjacent to its existing factory in Frome.
The new facility is expected to be completed by the end of the year and will house all the company's CNC machining operations, including a new Mills CNC ‘SYNERGi 25’ automated manufacturing cell.
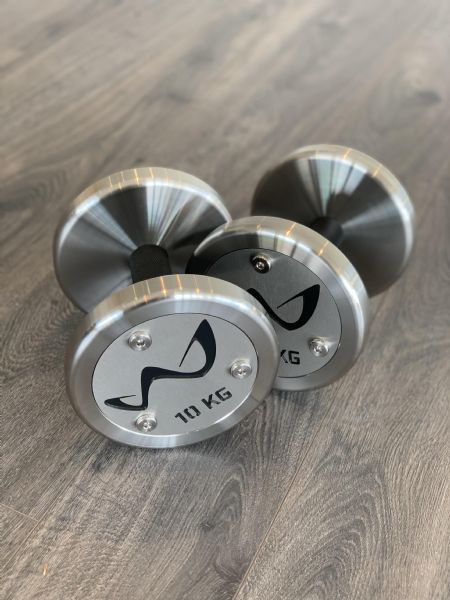
The cell comprising a Puma 2600SY lathe (with Y-axis and sub-spindle capabilities), a 25kg high-capacity industrial robot, an automated two-way drawer system (for stacking storing and loading workpieces and finished components), a 17in touchscreen HMI, locating plates, pneumatic grippers and SICK safety systems has been specified and ordered to help the company meet growing demand for its dumbbells.
Mr Watson concluded: “Automation is the key to increased productivity, operational efficiency and improved competitiveness. The SYNERGi 25 cell will help us increase throughput and reduce bottlenecks, and enable us to further exploit lights-out, unattended operations.
“We will be working with Mills CNC’s automation specialists in the next few weeks and months to create and prove out a bespoke manufacturing process at the company’s Automation and Turnkey Centre in Leamington prior to installation in our new facility.
“In the past six months we have developed a strong and positive working relationship with Mills CNC based on integrity and trust. The technologies it is able to supply and the added value consultancy it provides are helping us optimise our performance — making us fitter for the future.”