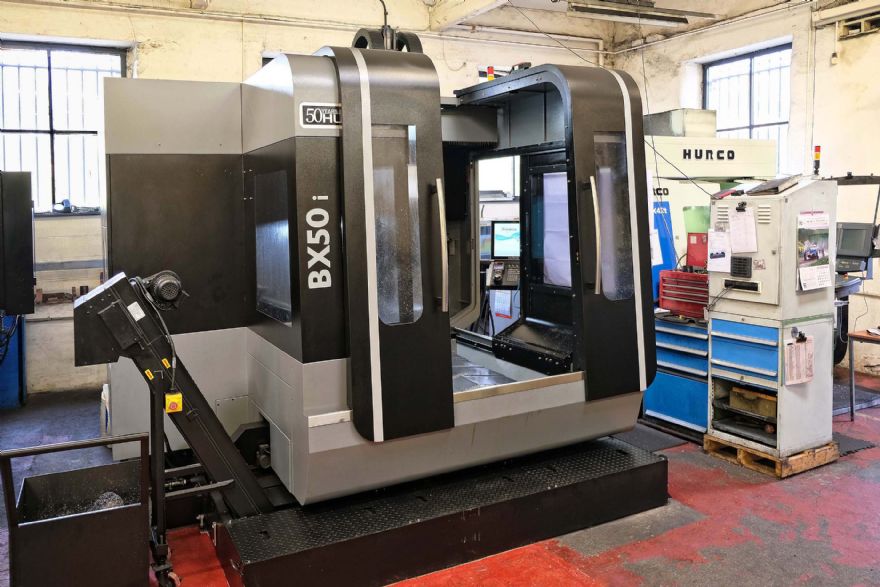
West Yorkshire-based Moorland Toolmaking has been a user of Hurco machining centres since 1985. It was first attracted by the supplier's Ultimax twin-screen control fitted to a KMB1x knee-type mill, on which a program could be created conversationally at one screen while a graphic of the part was automatically generated on the other.
Toolroom manager David Gibson reflected: “Its ease-of-use was perfect for a toolmaking environment, where one-offs are the norm. 35 years on, we now operate 10 Hurco three-axis CNC machining centres due to their reliability, good performance and competitive price.
“All of them feature a similar control, although now the software - WinMax - is Windows-based and much more updated in functionality."
He pointed in particular to the patented Ultimotion feature with up to 10,000 blocks of dynamic variable look ahead, which automatically determines the optimal trajectory for the cutter around the workpiece.
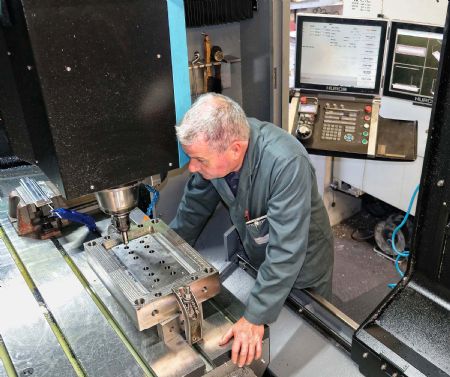
It keeps the programmed feed rate consistent and increases speed when machining around corners, reducing cycle times and improving surface finish. It is better than the smoothing features offered by CAD/CAM software and improves upon CAM output by providing better machine kinematics.
Even today, with mould tools being considerably more complex than in the past, the toolmaking and refurbishment specialist's operators still write three in ten programs at the control, mainly the simpler ones for producing bolsters and plates. The remainder are prepared off-line in Autodesk CAM from customers' CAD models.
The largest Hurco machine on-site is a VMX64Ti with a 1,625 x 864 x 762mm working volume. In March 2020, the toolmaker invested in a slightly smaller BX50i double-column, bridge-type machining centre with a 1,350 x 950 x 600mm envelope for producing big tools weighing up to 2.5 tonnes to even higher accuracy.
It is also used for producing other large components sub-contracted out to the firm, a part of the business that currently accounts for 10% of turnover and involves not only milling but also turning, sparking, wire erosion and deep-hole drilling.
On the toolmaking side, which accounts for the other 90&, around two-thirds of output goes to trade moulders serving the automotive industry and the rest to sectors such as white goods and garden ware.
The new, 13-tonne machine represents a step up in accuracy and performance compared with the other prismatic machining equipment in the 16,000ft
2 Batley factory.
The HSK-63A spindle speed is 18,000rpm, up 50% on the previous maximum on site, scales rather than encoders provide feedback of linear axis positions and thermal compensation measures have been incorporated throughout the machine.
Mr Gibson continued: “We saw the BX50i on the Hurco stand at the last
MACH show and were impressed at its robust construction. Since the machine was installed, we have been holding dimensional tolerances of better than ±25µm and we expect that level of precision to be long term.
"We also find that moulds coming off the machine have a better surface finish that typically needs 30 percent less polishing. It is a big saving, especially on large tools that can take up to a month to machine and then a further week to hand finish."
He added that the higher spindle speed is a further advantage, as smaller diameter cutters can be used so fewer features need to be sparked out, saving the time and cost involved in transferring tools to a die-sink EDM machine and of making copper and graphite electrodes on the other Hurcos.
In any case, milled features like deep ribs are quicker and easier to polish than if they are sparked, as the latter operation leaves a hard recast layer.
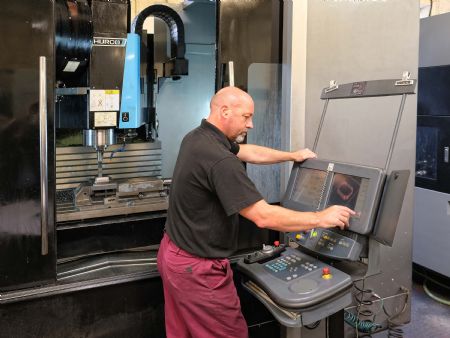
Despite being a satisfied, long-time Hurco machine user, Moorland Toolmaking considered two bridge-type machining centres offered from other potential sources.
What really swung the decision in favour of the incumbent supplier was the generous 950mm Y-axis travel on the BX50i, 150mm more than was available on other machines of equivalent footprint (approximately 4.5m
2) that were reviewed.
Consequently, the table will accommodate a 1m-wide workpiece, extending the size of component that can be produced in one hit rather than having to reposition it on the table. It also extends the size of part that can be tackled in two hits.
Mr Gibson concluded: “The BX50i was delivered the day the country was locked down due to Covid-19. Hurco engineers did a great job installing the machine in difficult circumstances, with some of their staff on furlough.
"Since then the machine has run faultlessly during the day and we have full confidence in taking advantage of extensive lights-out running for finishing our moulds through the night, which we do frequently.”