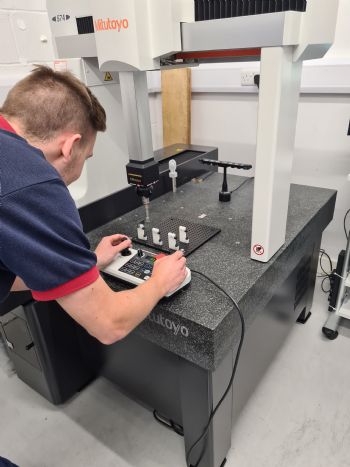
As final inspection is usually the last process undertaken before manufactured components are dispatched, delays in this activity can squander any time savings and efficiencies gained through the use of highly-productive CNC machine tools.
Similarly, when performing in-process inspection routines, hold-ups in the reporting out of tolerance situations can result in the continued manufacture of faulty or scrap parts.
To help address these situations, Andover-based
Mitutoyo UK Ltd recently introduced the Crysta-Apex V series of CNC co-ordinate measuring machines (CMMs).
Among the early users of these new CMMs is ADP Precision Engineering, a sub-contract machining business that is based in Newcastle upon Tyne and was established in 1999 by Anthony Ingledew and Peter Cornish.
To satisfy the quality and precision demands of its customers, the BS EN ISO 9001:2015-certified business regularly invests in advanced high-yield CNC machine tools and the latest IT systems.
Mr Cornish said: “Given our beliefs in producing premium-quality components and ensuring that we achieve maximum efficiencies in all of our activities, when we recently searched for a new CMM, the launch of Mitutoyo’s Crysta-Apex V series proved to be perfect timing, as the new CMMs high levels of speed and precision exactly matched our needs.
“Now installed, this CMM is helping to guarantee the quality of the components that we produce. Furthermore, its rapid CNC action is helping to fast-track the throughput of inspection work in our busy quality department. Its speed is also proving very useful when we are faced with challenging lead-times.”
Crysta-Apex V series CMMs feature a robust bridge-type construction, high-rigidity air-bearing guiding on each axis, and Mitutoyo’s ABS scales; these offer a high-resistance to adverse environmental conditions and allow these CMMs to operate efficiently and accurately within shopfloor locations. Further aiding use in less than perfect environments, the new Mitutoyo CMM range features an advanced temperature compensation feature.
Stephen Cross, ADP’s quality manager, said: “The speed of our new Crysta-Apex V CMM means that we can load a large batch of components onto the machine’s bed and initiate a quick and fully automated measuring sequence. On completion, data related to each individual component is then generated and if required we can print-out detailed inspection reports or archive all relevant inspection data.
“Indeed, the speed of this CMM is such that in addition to inspecting our current levels of production we are confident it will be able to handle any future increases in production.”
Another Crysta-Apex userEstablished in 1965 to help meet the sub-contract component machining needs of the burgeoning UK aerospace industry, Summit Engineering (Birmingham) Ltd has considerably expanded its range of machining competencies and diversified into other equally demanding sectors, although the production and assembly of precision aerospace components remains its main activity.
To ensure its output could be efficiently inspected, Summit Engineering recently installed a Mitutoyo Crysta-Apex CNC CMM— an S-series type — in a new environmentally controlled inspection facility at the company’s Solihull-based production facility.
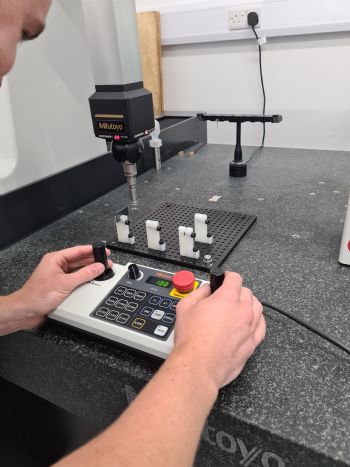
Explaining the reason behind the CMM purchase, Summit Engineering director Kevin McCormick said: “The company’s continuing success is due to our wide range of precision manufacturing and assembly capabilities, our flexibility, rapid response times and, not least, the exceptional quality of our manufactured components.
“Quality permeates every aspect of our activities. Besides our skilled production staff making regular in-process checks, our inspection team support their work with rapid feedback related to the status of each individual processes. In addition, thorough final inspection routines are performed — hence our extremely low rework and scrap figures.
“When we recently searched for a new CMM, we not only took into account the proposed machine’s capabilities but also other factors such as the ease and speed of operation and the depth of support provided, including training; and while the Crysta-Apex cost marginally more than the other machine that made our shortlist, it satisfied our long list of required criteria and we were happy to place an order for a machine with a work envelope of 705 x 1,005 x 605mm.”
Stephen Smolak, a Summit Engineering quality engineer, said: “Following its installation, our new Mitutoyo Crysta-Apex CMM soon began to make a significant contribution to ensuring the premium quality of our output.
In addition to inspecting large one-off components, we also load multiple smaller parts onto the CMM’s bed, recall the relevant program, then perform a rapid, fully automated CNC mass inspection routine.
“Moreover, the specification of our new Mitutoyo Crysta-Apex CMM means it can inspect our most complex components, as well as those with with extremely challenging accuracy requirements.”