Daewoo Puma 12L CNC lathe at Bromford IndustriesAs part of the
Bromford Group, Leicester-based Bromford Industries Ltd is a Tier One manufacturer that specialises in the Industrial Gas Turbines (IGT), power generation and aerospace sectors. Supplying customers in some of the most-demanding industry sectors and OEMs, the Bromford Group has to balance the delicacies of continuous improvement, innovation as well as the scrutiny of year-on-year ‘cost-down’ pressure.
That is why the company has a long-term contract in place with
MSC Industrial Supply Co, a specialist in metalworking and maintenance, repair and operations (MRO).
With its access to thousands of brands and hundreds of thousands of product lines, MSC has continually driven impressive ‘cost down’ results and productivity improvements for each of the four Bromford Group sites in the UK.
With integrated vending stations, continuity of cutting tool supply is guaranteed, but MSC doesn't rest on its laurels — it always strives to innovate and improve performance at Bromford.
One recent aerospace engine component arrived in Bromford’s Leicester facility from another Bromford Group facility in the USA and the company had to demonstrate the competence to manufacture the part at speed while adhering to the stringent quality requirements — all with very little cutting data.
The Leicester site specialises in the production of aero engine, landing gear and marine IGT components for blue-chip clients including Rolls-Royce, Pattonair, ITP, GE, Siemens and Messier Bugatti Dowty.
MSC steps up to the challengeTo manufacture the initial batch of four Inconel 718 aerospace engine components, MSC applied its technical expertise, drawing from the industry’s largest team of application engineers, to ensure the complex components could be manufactured to specifications, and on time.
With cutting tool datasheets from the USA being obsolete due to fact the tools were no longer available, MSC started from scratch and identified a rationalised tooling portfolio from a variety of suppliers, mitigating any special tooling to undertake the three operations and meet the specified deadlines.
Machining the four components on a Doosan Puma 12L turning centre, the MSC solution succeeded in meeting the Bromford deadline for the initial tests.
With the first batch complete and the competency to machine the parts proven, MSC application engineer Rob Smith was convinced that even better results could be achieved. With the second batch of eight parts pending, he revisited the engine components, the cutting tools and respective machining strategies and recommended a switch to ceramic cutting tools for the rough turning and grooving operations.
He said: “At the start of 2020, MSC formed a relationship with world-leading Japanese ceramic tooling brand NTK, and we knew the different physical properties of ceramic tooling would yield impressive results on heat resistant aerospace grade alloys.
“By nature, ceramic tooling is more brittle and susceptible to breakages if not managed with the correct machining strategy – but on the other hand, it can machine at speeds and feeds 10- to 15-times higher than carbide tooling.
“We collaborated with Simon Huxtable from NTK and the proposed strategy was to first remove the CNMG and SNMG carbide inserts and replace them with a round RNGN insert from NTK’s SX9 portfolio. The SiAlON grade that combines silicon nitride ceramic and alumina ceramic is claimed to be perfect for machining heat-resistant alloys at parameters way beyond carbide, so we put it to the test.”
Continuous improvementAndrew Moore, Bromford engineering and product quality manager, said: “We chose to partner with MSC six years ago, and ever since then they have been an extension to our business. As continuous improvement is important to us, we are always looking to make our processes better.
“With MSC, we know their engineers have the knowledge and expertise to help us achieve our goals. Having witnessed on-site trials in which cost-savings are documented and seeing how they leverage their extensive network of suppliers, assures me that MSC will always recommend the most efficient processes and tooling.
“This project is one of the many ways MSC has worked with us to seek innovative opportunities for improvement; they are a supply partner who wants us to succeed, as much as we do.”
After increasing the surface speed from 43m/min to 250m/min with a feed rate increase from 18mm/min to 106mm/min, the results soon followed. Rough turning the face and diameter of the 150mm diameter workpiece, the NTK SX9 RNGN insert not only replaced two previous carbide tools and eliminated the respective tool changeover, but it also slashed cycle times from 180 to 27min for the roughing operation.
While the previous carbide tooling method delivered a significant improvement on the original parameters from the overseas plant, the application of NTK’s SX9 ceramic inserts made a huge step forward from the method initially instigated by MSC.
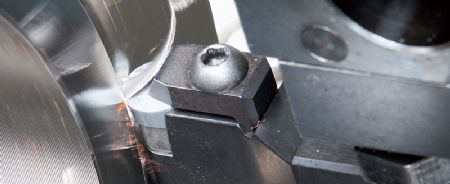
Mr Smith continued: “At MSC, we conduct extensive benchmarking analysis and we have calculated that Bromford would require 312 SX9 inserts to complete a run of 312 parts compared to a requirement of 470 CNMG carbide inserts and an additional 78 SNMG inserts.
“The NTK insert is achieving a tool life at least 2.5-times better than the previous carbide grade while accelerating cycle times to levels never before seen at Bromford.”
MSC also revisited the previous grooving operation that had been instigated with a world-leading carbide tooling brand, and once again implemented improvements with NTK’s SX9 grade.
Technical expertise Mr Smith explained: “We looked at the grooving operation as it was contributing to 22min of the overall cycle time for each part. While extended machining times are commonplace on materials like Inconel 718, we were confident we could make improvements.
“By applying a smaller RCGX09 insert, we profiled the two grooves in a cycle time of 3min 30sec, a huge reduction from the previous time of 22min. Again, this was achieved by maximising the properties of the NTK SiAlON grade to increase surface speed from 30 to 250m/min, the spindle speed from 64 to 530rev/min and the feed rate from 13 to 106mm/min.”
Lewis Evans, MSC national account manager for the Bromford Group, said: “Our engineers have demonstrated both our extensive portfolio of available solutions with the recent inclusion of NTK, but also the technical expertise to integrate relatively new brands into MSC accounts where they will make significant impacts.”
“We have completed the initial batches of four, then eight and now 41. On the batch of 41 parts, we have created a significant five-figure financial saving for Bromford and this has arrived by reducing annual tooling costs by 67%, machining costs by 85% and tool changeover costs by 34%.
“While these statistics are extremley impressive, one of the most stand-out points is that we have reduced machine hours for this single part by 85% from 1,060hr to just 158hr. This gives the customer additional machine capacity for undertaking other projects.”
He concluded: “These significant gains are only on one component and one machine. The opportunities for our engineers to go further at Bromford are vast. We will always continually strive to achieve the very best results for our customers.”