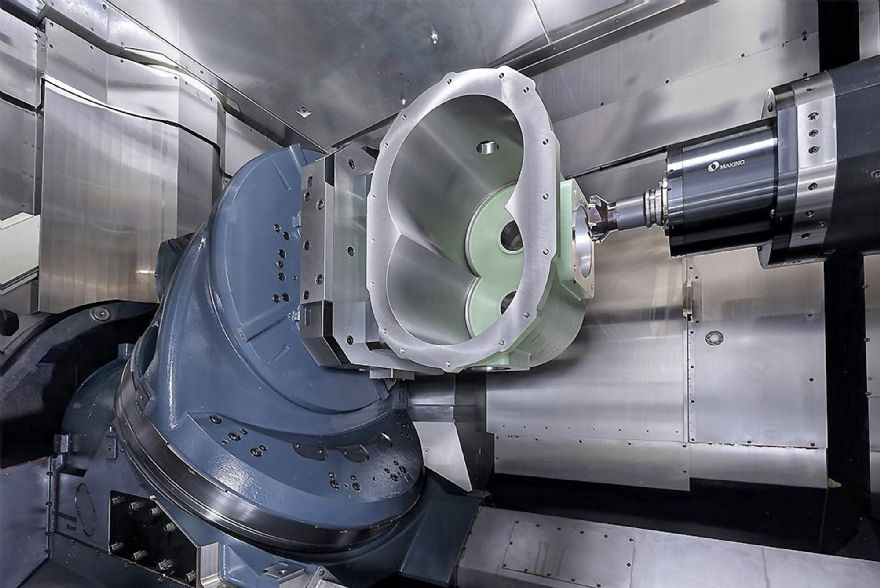
Japanese machine tool manufacturer
www.makino.eu Makino has introduced a new, five-axis, horizontal-spindle machining centre (HMC), which made its debut at
EMO 2021 last month in Milan.
Productivity on a five-axis machine is sometimes lower than on a four-axis model, but not with the a800Z, according to Surrey-based
NCMT Ltd, the sole agent for the UK and Ireland.
The jacket-cooled spindles provide the same power as on a Makino a81nx four-axis HMC. The standard 10,000rev/min BT50 (HSK-A100 optional) spindle takes just 2.7sec to reach maximum speed and is rated at 55kW (25% DC), 27kW (continuous), while torque is 721Nm (10% DC), 305Nm (continuous). An optional 8,000rev/min spindle provides uprated power at 75/37kW and higher torque at 1,199/552Nm.
By raising the rear X-axis guideway above the one at the front, the column travels over a slanted plane. It allows high cutting forces to be transferred efficiently during heavy-duty machining and maximises the rigidity of the machine structure.
The design also reduces the weight of the moving column, minimising jerk during acceleration and deceleration. The machining envelope is defined by axis travels of 1,280 x 1,200 x 1,325mm, actuation being by cooled, large-diameter ballscrews.
The agile rotary tilting table and fixtured workpiece have their centre of gravity close to the centre of rotation of the 180deg tilt axis. As a result, inertia is minimised and positioning movements can be performed accurately at high speed.
Productivity and short idle times are ensured by up to 50m/min cutting feed rate and 60m/min rapids. Maximum weight of the fixtured workpiece on the 630 x 630mm pallet is one tonne, excluding the weight of the pallet.
The a800Z also has a high capacity chip management system. The interior, near-vertical walls in the working area are stainless steel to minimise chip adherence and promote swarf evacuation via three channels in the machine base.
An agitator in the coolant tank prevents fine metal particles from settling and accumulating. The suspended particles are removed from the coolant by means of a cyclonic filtration unit, from where they can be safely discharged from the machine.
The 32-tonne HMC can be easily connected to various automation options including a pallet magazine or robotic workpiece load/unload system. It may also be incorporated into existing automation facilities such as a Makino MMC2 linear pallet pool, in combination with other machines such as an a81nx.