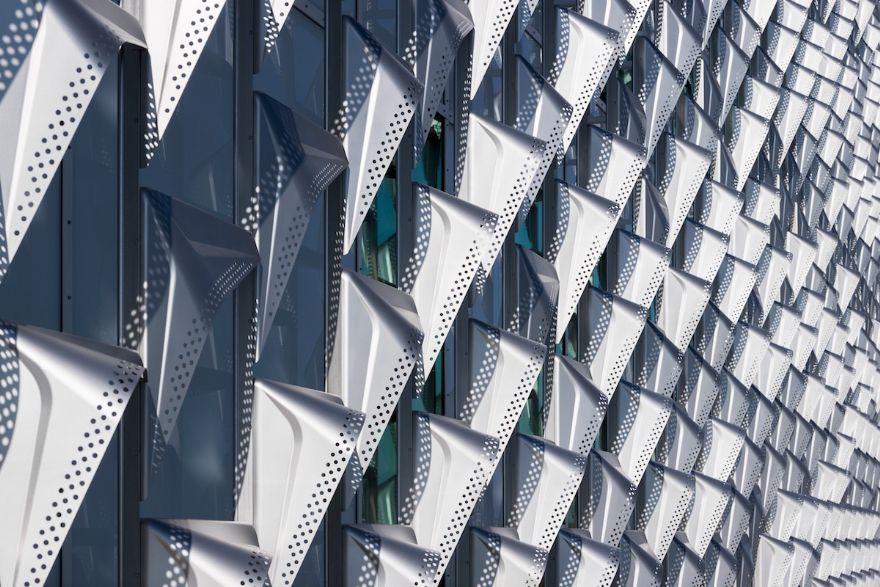
German fabricator Edelstahl-Mechanik, supported by the global thermal processing services company
Bodycote, has manufactured the world’s first hydroformed architectural facade. Designed by Behnisch Architekten, the newly constructed Science and Engineering Complex at the Harvard University campus in Boston, Massachusetts, is said to be ‘a fine example of balancing sustainability and aesthetic goals’.
A total of 12,800 stainless-steel panels in 14 different profiles were precisely fabricated and sculpted by Edelstahl-Mechanik using hydroforming, which is commonly used within the automotive and aerospace industries and uses water pressure to ‘shape thin metal plates against a mould’.
The panels were subsequently annealed by Bodycote, a heat treatment process that ‘alters the microstructure of a material to change its mechanical or electrical properties’.
In keeping with the university’s focus on sustainability, the exterior stainless-steel facade panels were designed to minimise solar heat gain in warm weather months, capture thermal energy in cold weather months, and provide natural light to the interior spaces.
Stainless steel can be used in all aspects of architecture, building, and construction and is widely used due to its ‘attractive appearance’, corrosion resistance, strength, ease of maintenance, low life-cycle costs, and lightweight properties.
Stephen Harris, Bodycote Group’s chief executive, said: “We are very pleased to have contributed to this project where sustainability has been at the forefront in all design aspects. The project demonstrates the value of how our thermal processing solutions can be applied to not only aerospace and automotive industries but also for architectural applications, by providing durable and sustainable solutions.”