Glenn Poleykett, owner and managing director of Stellar, with his latest sliding-head lathe acquisition — a Cincom L20-VIIILFV from Citizen Machinery UKGlenn Poleykett began his career in manufacturing in 2006 at his uncle's firm, making components for darts on Cincom sliding-head and Miyano fixed-head mill-turn centres. The machines are built by Citizen in Japan and sold in Britain and Ireland through subsidiary company
Citizen Machinery UK, which is based in Bushey.
Mr Poleykett quickly realised that sliding-head lathes with driven tooling were capable of producing virtually any part, provided that it was from 32mm diameter bar or smaller, whereas fixed-head models were incapable of machining shaft-type components to tight tolerances.
Fast-forward 12 years to when he first started
Stellar Precision Components in Bishops Stortford, and he went to the same supplier to purchase two Cincoms, an L32-VIIILFV and an A20-VII. The company has since been joined by a third sliding-head lathe, an L20-VIIILFV, which arrived on the shopfloor in April 2020.
Mr Poleykett said: “In the intervening years I worked at a number of sub-contractors on various makes of sliding-head lathe, but I always regarded Citizens as the best machines. My opinion was reinforced when a few years ago the manufacturer introduced its patented LFV (low frequency vibration) operating system software in the Mitsubishi control.
“It is programmable via G-codes to start and stop during any program, breaking what would normally be stringy swarf into smaller chips that cannot wrap around the tool or component and damage them.”
He witnessed LFV in action at Citizen’s UK headquarters and technical centre in Bushey before he bought the first two lathes and described the functionality as “incredible”. When machining short-chipping metals such as mild steel, 303 stainless and brass, he does not employ the function as it is not needed and the extremely short periods of air cutting slightly lengthen cutting cycles.
However when turning and drilling 304 or 316 stainless, aluminium, copper and plastics, he always turns on the function for at least part of the cycle. It has the effect of greatly improving production output through not having to stop the lathe to clear swarf and by being able to leave the machine to run unattended with confidence.
He would have ordered an LFV version of the A20-VII, but it had not been introduced on that model at the time, which is why the machine is devoted to producing components from free-cutting metals.
Shortening cycle timesLFV oscillation of the tool by tens of microns not only breaks the swarf but also allows coolant to penetrate the cut more efficiently for the brief periods when the tip lifts clear of the component surface, reducing heat and prolonging tool life. Depth of cut may be increased substantially, even when processing tough materials, significantly shortening cycle times.
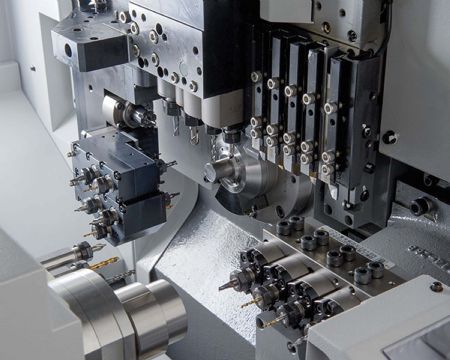
Swapping between the two modes of LFV is a simple matter, according to Mr Poleykett. If the second, more vigorous chip-breaking action is required, for example when cutting plastics, and the other mode has been inserted in a program by Citizen's Alkart CNC Wizard off-line part=programming software, manual insertion of a single line of code at the start and finish is all that is necessary.
It is noteworthy that, as is the case on more and more Cincoms and on some Miyano lathes, the most recent L20-VIIILFV delivered to Bishops Stortford has the chip-breaking functionality on both the main and sub spindle, whereas on earlier models it is applied to the main spindle only. Pictured (left) is the working area of the Cincom L20-VIIILFV, which deploys 37 tools in the machining area for versatility of production.
This latest machine at Stellar was purchased for manufacturing ventilator parts for the NHS. Funding through Citizen UK Finance and a six-month payment holiday smoothed the acquisition process at a difficult time.
Much of the sub-contractor’s throughput is destined for the aerospace, medical, electrical connector and pneumatics industries. Batch size ranges from 10 to 40,000 pieces and the factory operates 24/7, with two manned shifts per day and three hours of lights-out operation during the early hours of the morning.
The security of operator attendance for a majority of the time is needed, as many of the components that the subcontractor produces are of very high accuracy, from a general tolerance of ± 0.1 mm right down to ±5µm.
Components up to the maximum bar size can be produced on both L-series lathes either when the guide bush is in place or in guide bush-less mode, the latter being a standard feature of the machines.
The L32 was installed with an optional extension kit that allows bar up to 38mm diameter to be accommodated, higher than the lathe's nominal capacity of 32mm. This additional capability is regularly used and has allowed new business to be won.
Mr Poleykett takes full advantage of non-guide bush operation when producing shorter components, as it avoids having to use expensive ground stock. Plastic rod, which is always over-size, can be accommodated as well as unground bar of harder metals on which high spots can catch in the guide bush, alarming out the machine. A further benefit is material savings due to much shorter remnants.