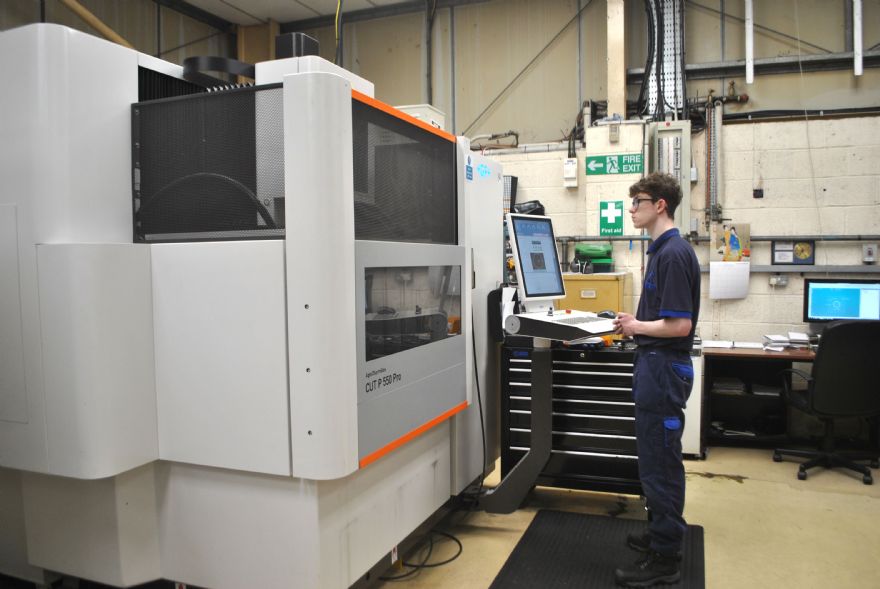
Birmingham-based
Bedestone Ltd, a leading wire erosion and jig grinding specialist, has recently taken delivery of a ‘state of the art’ wire EDM machine supplied by
GF Machining Solutions, the milling, EDM, laser and additive manufacturing (AM) machine tool manufacturer and automation and tooling systems specialist.
The machine, an AgieCharmilles CUT P 550 Pro, was delivered and installed in Bedestone’s 6,500ft
2 temperature-controlled machine shop facility in June 2021 and has taken its place alongside two, previously acquired, large capacity wire EDM machines and two EDM hole drillers, to create a high-precision wire EDM resource for its growing customer base.
The new CUT P 550 Pro has significantly increased Bedestone’s wire EDM capacity and capabilities and was acquired, as part of the company’s five-year ‘rolling’ Capex plan.
Richard Stanley, Bedestone co-owner and director, said: “The new machine has replaced an older Charmilles 330F wire eroder which, while still able to meet our accuracy and surface-finish requirements, was relatively slow by today’s standards, and was experiencing some reliability issues that, if left unchecked, would likely impact on our ability to meet customer lead times in the future.”
The company had originally intended to replace the Charmilles 330F in late 2019/early 2020 but the outbreak of the pandemic meant that Bedestone’s investment plans (over the short term at least), were put on hold.
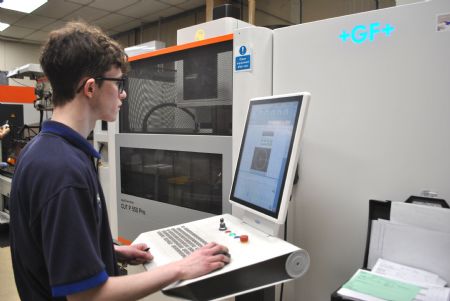
Mr Stanley added: “We, like many companies, were in limbo when Covid-19 struck and when the first national lockdown, in March 2020, came into force. Being a prudent company, we decided to postpone the planned wire EDM investment and wait to see how things panned out.”
The company didn’t have to wait long because a number of existing customers operating in essential industry sectors, most notably nuclear and defence, significantly ramped up their requirements for high-precision jigs, fixtures, tooling and components which continued throughout the lockdown periods.
He reflected: “We didn’t need to furlough any staff during the pandemic. In fact, demand for our wire EDM and grinding services reached an all-time high – so much so that employees were actually working overtime.”
With business booming, the previously postponed wire EDM machine investment plan was resurrected, as Mr Stanley explained: “We spent time identifying the key features and characteristics of the new machine we needed and approached a number of EDM machine tool manufacturers with our plans. We had also devised a challenging test cut (machining a precision spline) that we asked the participating machine tool manufacturers to undertake as part of the new machine procurement process.”
The key performance indicators of the test cut were part accuracy (holding tight geometric tolerances) and part cycle time. On both measures, as it transpired, the CUT P 550 Pro wire EDM machine from GF Machining Solutions came out on top.
Mr Stanley continued: “The CUT P 550 Pro was the best performing machine in the test cut, but our decision wasn’t just based on the results of the test. We also liked and responded positively to the business approach adopted by GF Machining Solutions.
“From the outset they were interested in what we were doing and where we wanted to get to. It felt more collaborative rather than merely a supplier providing a new machine to a customer.”
Following the installation, the CUT P 550 Pro has been in continuous action machining prototypes, one-offs and small batch series of precision parts for Bedestone’s defence, motorsport and nuclear customers.
The last eight months have provided ample opportunity for Bedestone to become familiar with its new machine, to understand its key strengths, and recognise the contribution it makes to the company’s future growth and success.
Mr Stanley said: “The CUT P 550 Pro is a compact machine. This was an important consideration for us because space is at a premium in the machine shop.”
The machine, despite its compact size, has a working envelope of 550 x 350 x 400mm. It also has a stable and rigid design and, among its many strengths, features integrated thermal compensation systems (water cooling and air conditioning) that help maintains temperature consistency within ±0.2deg, and enable high accuracies and repeatability’s to be maintained — even during long periods of operation.
Mr Stanley continued: “Our customers expect and demand exacting precision. The CUT P 550 Pro is equipped with a range of innovations and technologies that enable us to meet, and surpass, customer requirements.”
Central to the CUT P 550 Pro’s speed, versatility and accuracy is its Intelligent Power Generator (IPG) technology and a number of embedded ‘EXPERT’ and SMART systems.
He added: “The IPG digital generator delivers fast processing speeds, improved accuracies and repeatability’s, and enables us to achieve superior surface finishes (down to Ra 0.08um), in fewer passes. The EXPERT and SMART systems are equally impressive. They help make us more efficient and increase our flexibility.”
One of the many advantages of the CUT P 550 Pro machine is its onboard SMART wire technology. By combining EDM wire with RFID technology, the whole EDM process is made more reliable, secure and traceable.
The machine automatically recognises and configures itself to work with the wire installed, and operators and programmers, through the machine’s HMI, can see, at a glance how much wire remains on the spool and whether that is sufficient to complete the job(s) in hand.
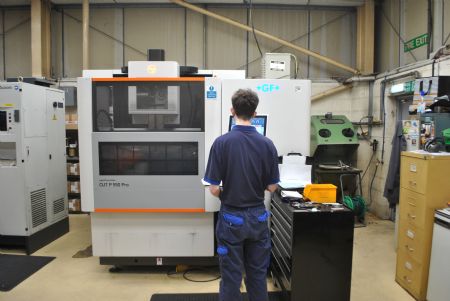
Mr Stanley continued: “You don’t want to start jobs and run out of wire half-way through. That is just being inefficient. SMART wire technology in conjunction with the Wire EXPERT system, which monitors, and controls wire use and wear in real time to ensure continuous and consistent geometrical accuracies, have significantly improved our productivity, and our performance, and have helped us reduce consumable (wire) costs.”
In addition to the power and speed of the generator technology, other particular strengths and highlights of the CUT P 550 Pro machine, according to Bedestone, include the ergonomically designed and intuitive 19in vertical touchscreen HMI that enables quick and easy job set ups, fast access to all machine functions and straightforward and real time monitoring of all machining operations.
Also, the powerful and secure Industry 4.0 communications platform, rConnect, gives customers, through its Messenger System, the ability to observe, remotely and in real time, their machine’s status and performance.
Another element of rConnect is the Live Remote Assistance (LRA) facility that enables quick and easy dialogue between a customer and technical support engineers within GF Machining Solutions support centres.
The facility enables a range of diagnostic and preventive maintenance operations to be performed remotely and in real time.
To get the best and the most from their new EDM investment, Bedestone opted for Renishaw probing in order to achieve in-process measurement and inspection and also invested in Fikus Visualcam – a powerful and precise CAD/CAM system.
Mr Stanley concluded: “The investment in Renishaw probing and a new CAD/CAM software makes economic sense and enables us to fully capitalise on the CUT P 550 Pro machine’s strengths.”