The Zimmermann FZU400 five-axis machining centre, with roof retracted, installed at the Bognor Regis facility of GTR Composites. The next-season F1 race car chassis on the table has been covered for confidentialityWest Sussex-based
GTR Composites, which operates out of four sites, is best known for supplying Formula One (F1) teams with high-quality carbon-fibre components and assemblies.
However, the company has an ever-increasing reputation for special projects and all things automotive. The highly specialised sub-contractor has produced lightweight chassis and other large components from composite materials for a long time, but at the beginning of 2021 it started final-machining them to tolerances measured in tens of microns.
Introduction of this new service followed the purchase of a German-built Zimmermann FZU400 five-axis machining centre, installed at GTR’s Bognor Regis facility at the end of 2020 by UK sales and service agent
Kingsbury. Having a 4,000 x 3,000 x 1,250mm working envelope, the portal machine was selected from a shortlist of three due to its ability to hold very high accuracy.
For example, a positional tolerance of 50µm is achieved on features across a full chassis, while holes and counterbores are held to within 10 or 20µm. As the components being produced are of high value, GTR adopts a policy of having an operator permanently in attendance, even when the FZU400 is running overnight.
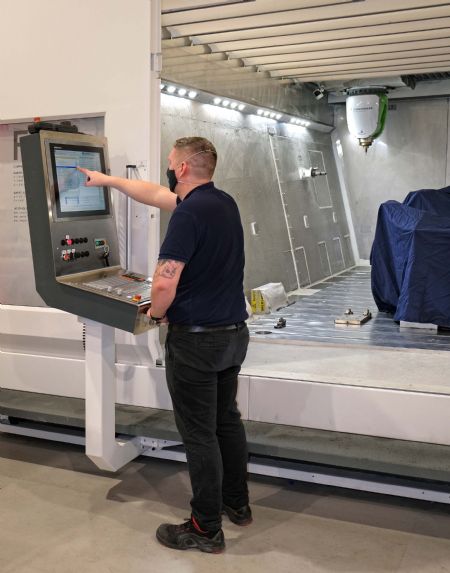
Simon Kingdon-Butcher, joint owner of GTR, said: “The investment has allowed us to expand our business not only in the motorsport sector but also on special projects and into more production chassis work for road-going supercars. We are presently producing 14 chassis for the research and development phase of such a vehicle.
"The Zimmermann machine stood out in terms of its rigidity, which translates into the tight tolerances we are able to hold when cutting carbon fibre. We are able to impress our customers by hitting really tight limits that our competitors cannot achieve. This investment has quite literally moved us ahead of the rest.
“High spindle power — 34kW continuous/41kW peak — enables us to rough aluminium moulds, while spindle speeds up to 24,000rev/min means their surfaces can be finish-machined to a very high standard using minimum quantity lubrication. MQL also enables us to mill and drill carbon fibre components containing titanium or aluminium inserts in the presence of a specific type of coolant approved by our customers.”
He added that their other large-capacity five-axis machining centres are focused on pattern making and while carbon fibre can be cut on them, the components would typically be of less demanding accuracy than the Zimmerman FZU400 is capable of delivering, despite its much larger working envelope. However, the machine is also used for large pattern work and he regards the versatility of the new capacity as an ideal fit for GTR.
The company is no stranger to making big components in large quantities, having produced 250 chassis in recent years for the MoD’s Foxhound patrol vehicle. Transition to final machining of larger structures and assemblies in carbon fibre, which entails cutting cycles of up to 60hr, is therefore proving seamless for the sub-contractor.
The addition of production volumes for supercars is seeing work for the motorsport sector, although remaining at a constant level, fall gradually from 90% of turnover to probably around two-thirds as the company expands.
The HSK-A63 spindle head of the thermo-symmetrically designed Zimmermann FZU400, which is fitted with extraction to manage the carbon fibre dust, has ±300-deg C-axis rotation and an A-axis swivel of +125/-95deg, resolution being 0.0001deg. Tools are exchanged automatically from a 61-station magazine. Acceleration at up to 3 m/s
2 to 60m/min feed rate in the linear axes ensures high productivity and short non-cutting times.
Mr Kingdon-Butcher concluded: “Kingsbury’s local engineering support, service and parts availability could not be better. Back-up has been impressive since the company installed a pair of smaller five-axis machining centres of a different make a couple of years ago, and it is proving to be so again.
“Kingsbury understood the high-knowledge level our machinists they were instructing, after the Zimmermann was commissioned, and tailored the training to suit. It was a good all-round experience."