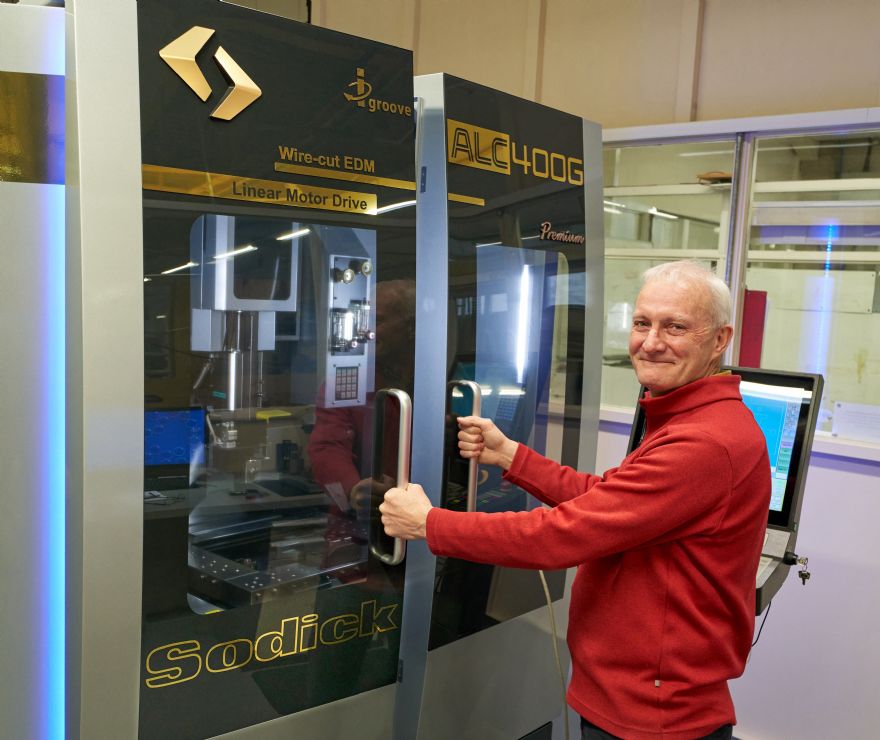
A leading manufacturer of high-quality products for model railway enthusiasts has placed an order for a fourth Sodick EDM machine. Devon-based
PECO, which supplies its products to shops across the UK and around the world, is about to enhance its toolroom with the addition of a Sodick ALC400G ‘i Groove edition’ wire-erosion machine from Warwick-based
Sodi-Tech EDM. It will join three existing Sodick machines already on site.
Established in 1946, PECO (Pritchard Patent Product Co Ltd) has its headquarters and manufacturing plant in the Devon coastal town of Beer, where the 150-employee business produces model rolling stock and track across eight different scales (from Z to G), as well as lineside/scenic and electrical accessories. Manufacturing in-house is clearly important to this progressive business, which is why the company runs a fully-equipped toolroom.
PECO innovations manager Paul Hitchcock, said: “Until 10 years ago, wire EDM was a new technology for us. Before our first wire machine we would split our dies and undertake form grinding, which was quite labour-intensive. At that time we had a Sodick AQ35L die-sinker, a very accurate and reliable machine, so we already had a relationship with Sodi-Tech EDM when we began thinking about a wire eroder — we ended up buying a Sodick AG400.”
PECO bought the wire EDM to eliminate the need for form grinding and maximise the accuracy of its press tools and their fine details using 0.1 mm diameter wire. However, uses for the Sodick machine soon evolved.
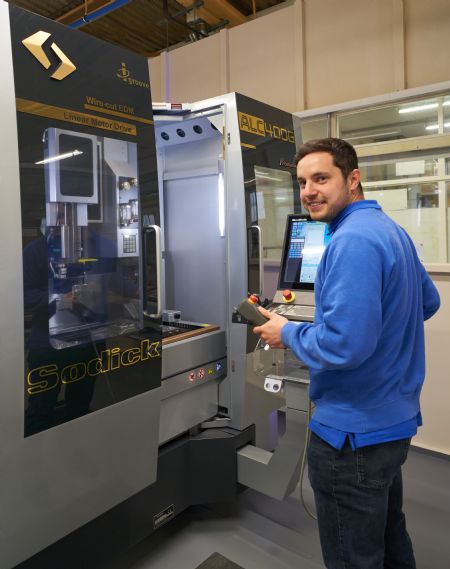
Mr Hitchcock added: “Until you have a new process on site you don’t actually know what influence it will have. Over the past decade we have gradually migrated to using the wire EDM for lots of different work that we never considered initially. Now, every time we look at a new press tool, mould tool, jig or fixture, we always ask: what parts can we do on the wire EDM?”
With 10 staff, the PECO toolroom currently has around 1,600 mould tools, press tools, jigs and fixtures available for use, mostly made from high-quality tool steel.
Mr Hitchcock explained: “When we make a new product it rarely drops out of our catalogue, so it is always there for customers if needed. We have a few mould tools that are around 40 years old, although they are subject to scheduled refurbishment using our Sodick wire EDM to ensure continuous product quality.”
With its existing Sodick wire EDM passing a decade of service – and despite its ongoing excellent performance – PECO decided it would be prudent to look at a second wire EDM.
He continued: “It was only ever going to be another Sodick. Not just because of machine quality, accuracy and ease-of-use, but also the support and relationship we have with Sodi-Tech EDM. We saw a press article about the Sodick ALC400G with its ‘i Groove’ rotating wire mechanism and decided to undertake some trials.”
Enhanced finishingApplying rotation to the wire reduces wire consumption and allows the constant use of new wire surface for enhanced finishing and accuracy from the top to the bottom of the workpiece. This capability brings further peace-of-mind regarding precision and reliability, which is vital to a busy company such as PECO. The plant works a single shift but often leaves its Sodick machines to run overnight unattended.
Mr Hitchcock said: “In the days of form grinding we had to have someone operating the machine, but with Sodick machines you just set them going and walk off to do something else. It’s a real benefit.”
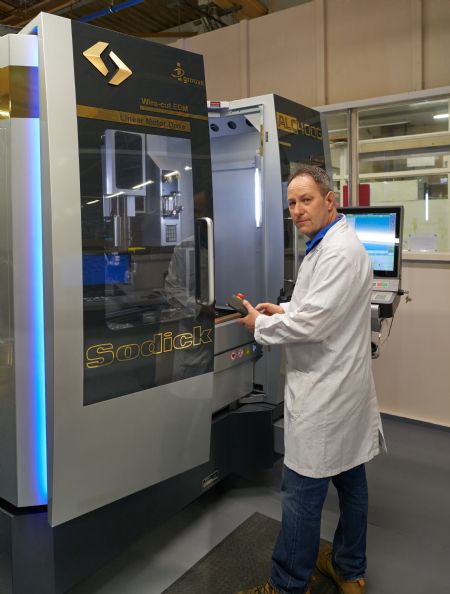
At present, sales of PECO products are “through the roof” due in some part to the pandemic, which has curtailed holidays and prompted hobbyists to invest in home-based activities.
“Having all of our manufacturing in-house is a huge market advantage, something that is very apparent in the current pandemic as we are not reliant on overseas suppliers. Of course, it’s important that we continue investing and innovating. Our aim is to bring out a new product every month, each one of which will need a new tool.”
PECO has a target to double its turnover in the next three to five years, which is not inconceivable given current demand. The real challenge will be keeping pace. For this reason, the company is still recruiting and has recently opened 260m
2 of newly-equipped factory space at its site in Beer, in turn creating space within its main production hall. PECO also has plans to expand its toolroom in the coming months, building on the imminent arrival of the Sodick ALC400G i Groove.
Mr Hitchcock concluded: “We have Sodick-exclusive EDM capability in our toolroom. The reason we have gone that way is the reliability of the machines and the relationship we have with the applications and maintenance teams at Sodi-Tech EDM.”