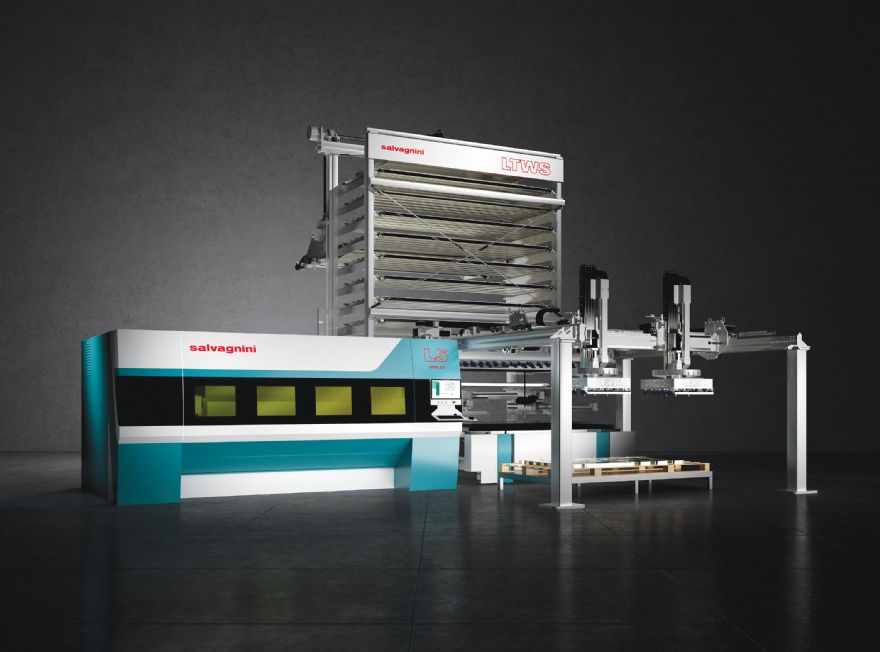
The cutting speeds being achieved by the latest laser machines have shifted the attention of many companies to the loading and unloading operations, as these are increasingly becoming production bottlenecks, but selecting the system that best suits a company’s requirements is far from a trivial matter. Pierandrea Bello, the product manager for laser technologies at
Salvagnini gives an insight to some of the matters to be considered.
“Mr Bello said: “To give some perspective on these matters, we have used LINKS, our IoT solution that continuously monitors the data from systems connected all around the world, to assess the efficiency of different configurations, analysing the many variables that come into play — such as the type and weight of the sheet metal used, and the material handling and waiting times.
“The results of this study show that while stand-alone solutions have an average efficiency of around 60%, automated systems — such as those based on our LTWS store-tower — have efficiency values of up to 90%. LTWS is an extremely compact high-end solution that is available in configurations from 6 to 38 trays and combines ultra-rapid cycles with high levels of autonomy.
“This Salvagnini solution is available in compact, single-tower or double-tower versions, with wooden pallets, without wooden pallets, or a mix of these. With the single- or double-tower versions, the loading and unloading devices are independent, increasing process efficiency, even in extremely rapid cutting programs; the compact version offers smaller dimensions and shorter cycle times, which can be further reduced with an extra bay.
“Autonomy is guaranteed by the availability of multiple materials, and by the ‘STORE’ software, which identifies the empty loading trays as new stations on which to stack the processed material.”
Mr Bello also says that an in-depth feasibility study is always the starting point for Salvignini’s discussions with customers, with considerations including: the maximum possible dimensions that can be accommodated; the required levels of autonomy and operational flexibility; whether or not it is necessary to incorporate an automatic sorting device; the need to access the pallet changer; and the investment which will be required.
“If the customer is looking for a compact system and has a limited budget, an LTWS Compact is probably the best solution. If the customer has restrictions in terms of space but needs a good level of autonomy and good operational flexibility while incorporating an automatic sorting device, the best choice will probably be an LTWS.
“If there are no limitations in terms of the size of the store-tower and the highest level of autonomy is required, a double-tower LTWS could well be recommended.”
Automated sortingMr Bello continued: “Without an automatic sorting device, our LTWS will return the sheet metal to the store-tower, and the operatives will then have to separate and stack the parts.
“In this kind of situation, our software will always offer three different strategies for managing unloading: fill mode requires an unloading tray to reach its maximum capacity before being changed; material mode involves the unloading tray being replaced on the basis of the material to be unloaded; while order mode involves all the sheets in the same production order being unloaded onto the same unloading trays. The operator can choose and modify the unloading strategy independently as required.
“That said, an LTWS store-tower can achieve even higher efficiency if it is equipped with a sorting device. Salvagnini offers the TN manual sorting device, which assists operatives in separating the cut parts from the skeleton and runs in parallel with the cutting job; the company also offers the MCU automatic sorting device, which is a solution for easily stacking parts with different geometries, sizes and weights.
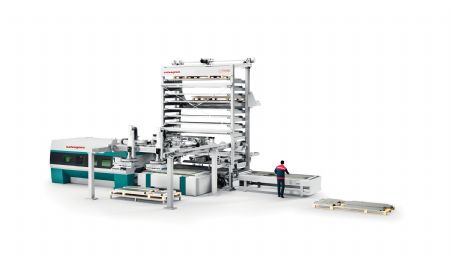
“In addition to the standard sorting strategy, MCU can work in multi-gripping mode, picking up several parts in sequence with the same gripping device; it can also work in double-picking mode, thereby reducing the time needed to pick up the parts.”
The MCU can pick up thicknesses of between 0.5 and 12mm and weights up to 65kg for each manipulator, or 130 kg when the two gripping devices work together; and while the gripping devices can pick up any part, whatever its maximum size or shape, the minimum size is 100 x 200mm.
However, to overcome this dimensional limitation, and to prevent automatic sorting from reducing the sheet yield, Salvagnini now offers a new ‘smart cluster’ function; this is used to micro-joint parts together quickly and easily, without using a cutting frame and without making programming more complicated in the office.
MCU and softwareThe MCU is managed by the Salvagnini CM software, which automatically defines the grips, automatically generates the unloading sequences, and positions the stacks of parts in the unloading areas.
Mr Bello added: “Furthermore, the MCU integrates with the whole range of Salvagnini automation options, significantly reducing waiting times between the end of the cutting and the start of the next processing sequence. It can make single parts immediately available for downstream processing in urgent cases, or physically integrate the laser with downline panel benders, press brakes, or robotised bending cells.”